-
- News
- Books
Featured Books
- smt007 Magazine
Latest Issues
Current IssueWhat's Your Sweet Spot?
Are you in a niche that’s growing or shrinking? Is it time to reassess and refocus? We spotlight companies thriving by redefining or reinforcing their niche. What are their insights?
Moving Forward With Confidence
In this issue, we focus on sales and quoting, workforce training, new IPC leadership in the U.S. and Canada, the effects of tariffs, CFX standards, and much more—all designed to provide perspective as you move through the cloud bank of today's shifting economic market.
Intelligent Test and Inspection
Are you ready to explore the cutting-edge advancements shaping the electronics manufacturing industry? The May 2025 issue of SMT007 Magazine is packed with insights, innovations, and expert perspectives that you won’t want to miss.
- Articles
- Columns
- Links
- Media kit
||| MENU - smt007 Magazine
The EMS Skills Gap Epidemic
August 18, 2017 | Steve Williams, The Right Approach Consulting LLCEstimated reading time: 5 minutes
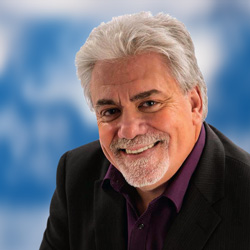
Interviews with EMS industry executives across the country are united in their top concern for their businesses: finding new talent. Manufacturers can no longer afford to wait. It is time to educate and train the next generation of manufacturing.
The Results Are in
Is this really a problem? The short answer is yes; actually, it’s hell yes! According to the U.S. Bureau of Labor Statistics, every dollar spent in manufacturing adds $1.37 to the U.S. economy, and every 100 jobs in a manufacturing facility creates an additional 250 jobs in other sectors. Yes, Virginia, manufacturing matters.
A recent survey by Career Builder, an online service that matches job seekers with open positions, highlights one of the most frustrating aspects of the current job market: Why can’t employers fill their positions when approximately 7.5 million Americans are unemployed, and millions more are working part-time because they can’t find full-time positions or have given up looking for work altogether? Looking at the following survey data, 68% of employers who said they were increasing their number of full-time, permanent employees in the first quarter (January 1– March 31, 2017), currently have open positions for which they cannot find qualified candidates.
This is consistent across company sizes:
- 1-50 employees: 49% unfilled positions
- 51-250 employees: 74% unfilled positions
- 251-500 employees: 72% unfilled positions
- 501+ employees: 71% unfilled positions
The manufacturing skills gap is real.
Deloitte recently did an analysis of the skills gap from 2015–2025 that shows alarming results. The analysis showed that over the next decade nearly 3.5 million manufacturing jobs will need to be filled, with 2 million (60%) of those jobs going unfilled directly due to the skills gap. With industry executives around the globe identifying talent-driven innovation as the number one factor in establishing competitive advantage, it is very easy to draw a direct negative correlation from skills gap to growth and profitability. Deloitte reported that 82% of executives responding indicate they believe the skills gap will impact their ability to meet customer demand, and 78% believe it will impact their ability to implement new technologies and increase productivity.
In addition, executives indicate the skills gap also impacts the ability to provide effective customer service (69%), the ability to innovate and develop new products (62%), and the ability to expand internationally (48%). The sobering takeaway from the data is that the skills gap is real—and so are the consequences. An overwhelming number of American executives (92%) believe that American workers aren’t as skilled as they need to be, and American workers agree, with 1 in 5 saying their professional skills are not up to date. What does this mean in bottom-line dollars? Almost $1 million in lost business for most companies.
This is a wake-up call for the industry.
College is a path, not a right!
A changing society is as much to blame as anyone for the lack of bench strength in our U.S. manufacturing companies. Ask any young person and they will probably tell you that college is not a privilege, it is a right! (If you really want to blow your mind, ask them who they think should pay for it.) Not to paint all young people with an overly broad brush as there are plenty of hard working kids with their heads on straight, but compared to past generations, they are a bit of an entitled bunch. Remember the aforementioned hard work, dues paying and understanding that you must earn what you want? Not so much with today’s youth. Right out of college they expect a cushy desk job, with an office and a high-paying salary because they “paid their dues” simply by just going to college.
I don’t blame the kids; first, I blame the educational system that teaches them from a very early age that college is the only choice, and that they are entitled to it. Remember when college was just one of three potential paths that high school graduates could pursue? The other choices were the trades or to enter the general workforce, both providing just as many opportunities, if not more, then the college path.
Contrary to what our children are being taught, college is not for everyone, and certainly not for every job. What we have now is an awful lot of college educated 20–30 somethings asking, “do you want fries with that?” or choosing to live in mom and dad’s basement because getting their hands dirty in a factory job is beneath them. I remember guidance counselors that actually helped students determine what to do with their life, not just what to do in college.
Second, I also place blame with the parents! We have been seeing the “participation trophy” generation entering the workforce for a while now, and the results are not pretty. Parents that push kids into college to earn a degree that there is little market for are part of the problem. Encouraging their kids to stay at home far longer than ever before is enabling the entitlement syndrome that has created the situation we are in relating to the next generation of manufacturing craftsmen and women.
Page 1 of 2
Suggested Items
Zollner Completes Full Acquisition of Bluechips Microhouse
07/01/2025 | Zollner Elektronik AGZollner Elektronik AG has successfully finalized its com- plete takeover of Bluechips Microhouse Co., Ltd., in Thailand. In the future the company will operate as part of the Zollner Group of companies under the leadership of Thomas Kiefl – strategically networked, technologically focused and internationally oriented.
Inission Acquires the Lithuanian Company Selteka
07/01/2025 | InissionInission AB has signed an agreement to acquire 100% of UAB Selteka. Selteka is a well-respected EMS (electronics manufacturing services) company with operations located in Kaunas, Lithuania.
Kitron Strengthens Order Backlog with EUR 11 Million Contract for Defense Communication
07/01/2025 | KitronKitron has received an order valued at EUR 11 million to produce advanced military communication products destined for the European market.
IMI Wins Gold Award for Best Managed Technology Company at FinanceAsia’s 29th Asia’s Best Companies Awards
07/01/2025 | IMIIntegrated Micro-Electronics Inc. (IMI) has been awarded the prestigious Gold Award for Best Managed Technology Company at the 29th edition of the Asia’s Best Companies Awards, hosted by FinanceAsia.
Compal Announces Completion of New Automotive Electronics Facility in Poland, Signaling Strategic Growth in Europe
06/30/2025 | Compal Electronics Inc.Compal Electronics is proud to announce the completion of Phase One of its new manufacturing facility in Czeladź, Silesian Voivodeship, Poland, marking a major milestone in its strategic expansion into the European automotive electronics market.