-
- News
- Books
Featured Books
- pcb007 Magazine
Latest Issues
Current IssueSales: From Pitch to PO
From the first cold call to finally receiving that first purchase order, the July PCB007 Magazine breaks down some critical parts of the sales stack. To up your sales game, read on!
The Hole Truth: Via Integrity in an HDI World
From the drilled hole to registration across multiple sequential lamination cycles, to the quality of your copper plating, via reliability in an HDI world is becoming an ever-greater challenge. This month we look at “The Hole Truth,” from creating the “perfect” via to how you can assure via quality and reliability, the first time, every time.
In Pursuit of Perfection: Defect Reduction
For bare PCB board fabrication, defect reduction is a critical aspect of a company's bottom line profitability. In this issue, we examine how imaging, etching, and plating processes can provide information and insight into reducing defects and increasing yields.
- Articles
- Columns
- Links
- Media kit
||| MENU - pcb007 Magazine
Estimated reading time: 3 minutes
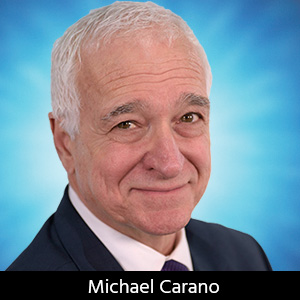
Contact Columnist Form
Trouble in Your Tank: Moving into Microvias—The Interaction of Materials and Processes, Part 1
In the first part of a series of columns focused on microvias, the importance of adopting HDI technology as a strategic initiative for the PWB fabricator is presented. The major drivers for HDI are listed.
Introduction
Let’s face it. If you are in the printed circuit board fabrication business (and want to stay in—assuming you want to make money as well), acquiring HDI capability is very important. Part and parcel to this is adopting enabling processes and technologies that encompass design, material selection, improved wet processes and imaging technology, laser formed microvias and equipment packages. If designed with the proper architecture, printed circuit boards with microvias offer the most significant opportunity to reduce the layer counts and overall board thickness. In addition, the cost may be reduced while improving electrical performance and density of the interconnect.
Design for HDI
Blind microvias are a surface feature. With the optimum architecture, routing densities are increased and some of the layers in a traditional through hole designed multilayer board layers can be removed. An example of this is illustrated in Figure 1.
Figure1: Various layer assignments available when using HDI and microvias (Source: Happy Holden).
First priority is to reduce and eliminate through-vias. These block routing channels on the innerlayers. By eliminating 25% of the TH, 2-3X as many traces can be routed on the innerlayers. One way to do this is to move the ground plane (that is usually on layer 2) to the surface and use the microvias as via-in-pad (VIP) or near-via-in-pad (NVIP). This eliminates the most abundant vias on the boards- the ones to ground. As a consequence blind vias will have more conventional aspect ratios. More on this in a futue column.
Drivers for HDI
One needs to fully understand end user requirements prior to making capital investments for HDI production. It is a given that electronic systems and packages are becoming denser. All one has to do is look at the latest smart phones and tablets. However there are other drivers for this miniaturization trend that may not be obvious to the reader. Fine-pitch packages (QFPs and BGAs) and increasing pin counts of packages are driving the interconnect designs for military-aerospace, medical, telecom and industrial electronics. HDI, when properly designed into the PWB structure, improves signal integrity as well as via reliability.
Again, let’s list the main drivers for HDI:[1]
- Integration of high-I/O and fine-pitch devices
- Higher component density and component I/Os
- Reduction in layer count for thickness control and RoHS compliance (LF assembly)
- Improved electrical performance and SI (reduced noise, EMI and RFI)
- Effective integration of embedded passives
- Lower costs through less layers and smaller boards
Figure 2: The IPC HDI Type I to Type III are the most common microvia structures used—from the simplest (Type I) to the most complex (Type III with stacked vias)[2].
So why is this important? First, don’t look at HDI as something “just for mobile phones.” When you hear someone capitulate to that way of reasoning, that person is not looking at HDI from a strategic point of view. And this is not to say that all fabricators should simply rush into HDI for to be fashionable! This is all about technology and go-to-market strategy for the business. So think it through and assess one’s capabilities. Don’t expect that the fabricator already possesses the competencies to successfully implement an HDI manufacturing technology.
That would be a mistake. Thus, it is important to remember that there are several disciplines to master including material selection, blind via and microvia formation, circuit formation, lamination and metallization. Even though microvias are the primary feature for HDI constructions, thinner dielectrics, ultra-thin copper foils and finer lines and spaces are key features as well. There is also a movement to coreless lam dielectrics and dielectric build-up materials in place of copper clad laminate. These last two are also enablers for finer lines and spaces. Basically, getting into HDI requires changing one’s thinking about PWB fabrication. And that must first start with getting familiar with standards.
HDI Standards
As one decides to adopt HDI, the IPC-2315 HDI Design Standard will be required reading. This critical document outlines the simplest architectures for HDI (Figure 2).
Keep in mind that there are tradeoffs when designing interconnects with blinds vias. In addition, PWBs with only through-holes designed in limit the density one can achieve. Without microvias, layer counts and costs will increase to support higher pin counts.
References
1. Holden, H., “Introduction to HDI Substrates and Microvia Technology,” The Board Authority, Vol.2 No.1, April 2000, pp. 8–12.
2. IPC 2315.
This column originally appeared in the August 2017 issue of The PCB Magazine, click here.
More Columns from Trouble in Your Tank
Trouble in Your Tank: Can You Drill the Perfect Hole?Trouble in Your Tank: Yield Improvement and Reliability
Trouble in Your Tank: Causes of Plating Voids, Pre-electroless Copper
Trouble in Your Tank: Organic Addition Agents in Electrolytic Copper Plating
Trouble in Your Tank: Interconnect Defect—The Three Degrees of Separation
Trouble in Your Tank: Things You Can Do for Better Wet Process Control
Trouble in Your Tank: Processes to Support IC Substrates and Advanced Packaging, Part 5
Trouble in Your Tank: Materials for PWB Fabrication—Drillability and Metallization