Nanocarbon Materials Are Challenging Silicon – From Transparent Electronics to Bendable 3D Displays
September 7, 2017 | Aalto UniversityEstimated reading time: 3 minutes
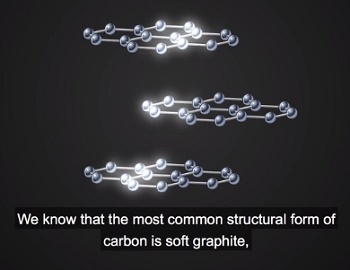
The superior characteristics of nanocarbon make it an extremely promising material for numerous current and future applications.
"Light and flexible nanocarbon materials conduct electricity better than copper and have greater mechanical strength than steel. They are also good thermal conductors and have great potential for use in reinforced composites, nanoelectronics, sensors and nanomechanical devices," says professor Esko I. Kauppinen, the director of Aalto University’s NanoMaterials research group.
Recently, significant advances have been made in the development of nanocarbon materials and their applications. The International Symposium on Nanocarbon Materials gathered the world’s cutting-edge nanocarbon material researchers to Aalto University.
Flexible and transparent electronics
One of the breakthrough applications of carbon nanotubes (CNT) is foreseen in transistor technology. Carbon nanotubes have already been shown to outperform silicon as the semiconducting material for transistors.
"The structure of CNT makes it more chemically stable than silicon. Compared to silicon CMOS technology, carbon nanotube devices are about 5-10 times faster, over 10 times more efficient in power consumption and much smaller in size," says professor Lian-Mao Peng from Peking University.
There are still several technical problems to solve before CNT based chips become commercial products; the main concerns are the material’s thermal and long-term stability. Also, the silicon industry is very mature and it will take major efforts to replace silicon as semiconducting material in electronics.
"I would say in 3-5 years we will see CNTs in some low-end applications that are not dominated by silicon, like flexible and transparent electronics. Maybe in 10-15 years CNT will get to mainstream semiconductor industry with high performance and low power consumption," Peng says.
Carbon nanotube films are also a potential material for the charge selection/conduction layer of perovskite solar cells. Perovskite solar cells challenge the traditional silicon cells with a cheaper, simpler and more energy-efficient manufacturing process.
"The best reported perovskite solar cells have the power conversion efficiency of 22 percent which is compatible to silicon solar cells. And, they can be much cheaper than silicon cells as organic solar cells. Also, flexible and transparent perovskite solar cells could be integrated in windows and other building surfaces. I expect they could become commercial in 3-5 years," says professor Shigeo Maruyama from the University of Tokyo.
Carbon nanostructure such as graphene gets exciting new applications through nanoscale technologies. Photo: Alexander Savin.
Shaping surfaces with curved and 3D formed displays
Besides carbon nanotubes, nanocarbons are found in various structures like spherical fullerens and single atomic layer graphene. In 2006, a new carbon composite nanomaterial was discovered by Aalto University NanoMaterials Group headed by professor Kauppinen. The material was named and patented as NanoBud.
"NanoBuds are formed by binding spheroidal carbon molecules, fullerenes, to the outer sidewalls of single-walled carbon nanotubes. Printed on a thin film of plastic, NanoBuds can be used in touch screens of mobile phones, cameras and wearable devices," Kauppinen says.
The discovery of NanoBud led to the establishment of Canatu Oy to develop and exploit commercial innovations. The Aalto University spin-off company manufactures 3D formable, flexible and transparent carbon NanoBud films and touch sensors for consumer electronics and automotive industry.
The NanoMaterials Group is one of the world's leading gas-phase synthesis laboratories for NanoBuds, nanotubes and nanomaterials. In Aalto University, high-level nanocarbon material research is conducted also in several other research teams in the School of Science, School of Chemical Engineering and School of Electrical Engineering.
"Besides our strong international networks, nanocarbon material research collaboration within Aalto University is most fruitful. By learning from each other we can achieve much better results compared to what we could accomplish ourselves," Kauppinen says.
The future of nanocarbon materials shines bright.
Testimonial
"We’re proud to call I-Connect007 a trusted partner. Their innovative approach and industry insight made our podcast collaboration a success by connecting us with the right audience and delivering real results."
Julia McCaffrey - NCAB GroupSuggested Items
MKS Showcases Next-generation PCB Manufacturing Solutions at the Thailand Electronics Circuit Asia 2025
08/06/2025 | MKS Instruments, Inc.MKS Inc, a global provider of enabling technologies that transform our world, today announced its participation in Thailand Electronics Circuit Asia 2025 (THECA 2025), taking place August 20–22 at BITEC in Bangkok.
Point2 Technology, Foxconn Interconnect Technology Partner to Revolutionize AI Cluster Scalability with Terabit-Speed Interconnect
08/06/2025 | BUSINESS WIREPoint2 Technology, a leading provider of ultra-low-power, low-latency mixed-signal SoC solutions for multi-terabit interconnect, and Foxconn Interconnect Technology (FIT), a global leader in precision interconnect solutions, have signed a Memorandum of Understanding (MOU) to accelerate the commercialization of next-generation Active RF Cable (ARC) and Near Pluggable e-Tube (NPE) solutions.
Advancing Electrolytic Copper Plating for AI-driven Package Substrates
08/05/2025 | Dirk Ruess and Mustafa Oezkoek, MKS’ AtotechThe rise of artificial intelligence (AI) applications has become a pivotal force driving growth in the server industry. Its challenging requirements for high-frequency and high-density computing are leading to an increasing demand for development of advanced manufacturing methods of package substrates with finer features, higher hole densities, and denser interconnects. These requirements are essential for modern multilayer board (MLB) designs, which play a critical role in AI hardware. However, these intricate designs introduce considerable manufacturing complexities.
Statement from the Global Electronics Association on the July 2025 Tariff on Copper Foil and Electronics-Grade Copper Inputs
07/31/2025 | Global Electronics AssociationWe are disappointed by today’s decision to impose a 50% tariff on imported copper foil and other essential materials critical to electronics manufacturing in the United States.
Trouble in Your Tank: Metallizing Flexible Circuit Materials—Mitigating Deposit Stress
08/04/2025 | Michael Carano -- Column: Trouble in Your TankMetallizing materials, such as polyimide used for flexible circuitry and high-reliability multilayer printed wiring boards, provide a significant challenge for process engineers. Conventional electroless copper systems often require pre-treatments with hazardous chemicals or have a small process window to achieve uniform coverage without blistering. It all boils down to enhancing the adhesion of the thin film of electroless copper to these smooth surfaces.