-
- News
- Books
Featured Books
- pcb007 Magazine
Latest Issues
Current IssueInventing the Future with SEL
Two years after launching its state-of-the-art PCB facility, SEL shares lessons in vision, execution, and innovation, plus insights from industry icons and technology leaders shaping the future of PCB fabrication.
Sales: From Pitch to PO
From the first cold call to finally receiving that first purchase order, the July PCB007 Magazine breaks down some critical parts of the sales stack. To up your sales game, read on!
The Hole Truth: Via Integrity in an HDI World
From the drilled hole to registration across multiple sequential lamination cycles, to the quality of your copper plating, via reliability in an HDI world is becoming an ever-greater challenge. This month we look at “The Hole Truth,” from creating the “perfect” via to how you can assure via quality and reliability, the first time, every time.
- Articles
- Columns
- Links
- Media kit
||| MENU - pcb007 Magazine
Estimated reading time: 3 minutes
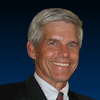
All About Flex: Using ZIF Connectors with Flexible Circuits
Zero insertion force (ZIF) connectors are probably the most popular flexible circuitry connector because they allow the circuit to be inserted and removed multiple times with very little mechanical wear on the copper traces. ZIF connectors are designed with a mechanical latching mechanism that clamps down onto exposed traces to ensure a long lasting, robust connection. The connector’s latching mechanism allows the circuit to be released and permits easy removal of the flex.
Another significant advantage of a ZIF connector system is the elimination of a mating connector. This allows a reduced connection profile while keeping cost and weight of the circuit assembly to a minimum.
There are many companies that provide ZIF connectors. Three popular suppliers are AMP, Hirose and Molex. Some considerations when designing/specifying a flexible circuit assembly using ZIF connectors are discussed below.
Overall Thickness
The connector’s latching mechanism closes onto the flexible circuit and properly seats within a narrow thickness range. Total thickness of the flex circuit in the connector area (thickness from the top of the plated copper pads to the bottom of the stiffener on the opposite side) needs to be controlled with the adhesive thickness bonding the stiffener (which essentially is acting as a shim) as a key variable. The most common thickness range for the end of the circuit inserted into the connector is 0.012” +/- 0.002”. There are also less common ZIF connectors available specifying thinner thicknesses.
Stiffener
In most cases a stiffener needs to be bonded to the circuits back side to create the proper thickness. This also helps to ensure adequate rigidity so the end of the circuit can be easily inserted without damaging the circuit. Stiffeners are most commonly made of polyimide, polyester or FR-4 (glass epoxy) and are attached with either a thermoset adhesive or a pressure sensitive adhesive (PSA). The length of the stiffener is an important consideration as it should not coincide with the end of the coverfilm or be positioned at a point where the circuit will be tasked to bend. This can create a focused stress point. It is recommended to overlap the coverlay end by at least .030” to avoid the mechanical stress that could ultimately result in a fractured trace (Figure 1).
Figure 1: Cross-section of flex circuit for ZIF connector.
Outline Profile
ZIF connector circuits will often vary slightly in their outline shape. Many of the tails have simple and straight edges, however, others require contoured edges to create retention features. This shaping also allows visual verification of proper insertion. The circuitry set-up/design engineer will define cutline dimensions once the connector manufacturer and part number are known.
Image to Cutline Registration
Another key feature of the circuitry on a flex circuit inserted into a ZIF connector is the image to cutline tolerance. The latching connector uses the edge of the circuit as a mechanical edge guide for alignment of the trace pattern to the connector contacts. Tolerance requirements from image to edge of circuit are most often +-.002”, with tighter requirements seen frequently. Cutting the circuit with a laser or an optical punch insures this feature is maintained.
Surface Finish and Thickness
Electroless nickel immersion gold (ENIG) is the most common finish for ZIF connector interface. ENIG has the advantage of excellent solderability, allowing this single finish to be applied across the entire surface of the circuit. There are other options including electro-plated Ni/Au which provides a thicker gold surface. This may be specified in high reliability applications or when an inordinate amount of mechanical force is required such as in membrane switch keypad contacts.
Tin-lead solder plating, immersion tin, or carbon printing are additional surface finishes used with ZIF connections. It is important to match surface finishes between the circuit and the connector, for example, if the connector contacts are gold, the traces on the flex circuit should also have a gold finish.
Dave Becker is vice president of sales and marketing at All Flex Flexible Circuits LLC.
More Columns from All About Flex
All About Flex: Terms and ConditionsAll About Flex: ISO 9001 Basics
All About Flex: FAQs on UL Listings for Flexible Circuits
All About Flex: Avoiding Trace Fracturing in a Flexible Circuit
Polyimide vs. Silicone for Flexible Heaters
All About Flex: Copper Thickness Requirements for Flex Circuits
All About Flex: Copper Grain Direction
All About Flex: Options for Purchasing Flexible Heaters