-
- News
- Books
Featured Books
- pcb007 Magazine
Latest Issues
Current IssueInventing the Future with SEL
Two years after launching its state-of-the-art PCB facility, SEL shares lessons in vision, execution, and innovation, plus insights from industry icons and technology leaders shaping the future of PCB fabrication.
Sales: From Pitch to PO
From the first cold call to finally receiving that first purchase order, the July PCB007 Magazine breaks down some critical parts of the sales stack. To up your sales game, read on!
The Hole Truth: Via Integrity in an HDI World
From the drilled hole to registration across multiple sequential lamination cycles, to the quality of your copper plating, via reliability in an HDI world is becoming an ever-greater challenge. This month we look at “The Hole Truth,” from creating the “perfect” via to how you can assure via quality and reliability, the first time, every time.
- Articles
- Columns
- Links
- Media kit
||| MENU - pcb007 Magazine
Estimated reading time: 3 minutes
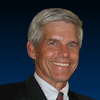
All About Flex: Flexible Circuits for Reusable Medical Products
Flexible circuits have been used in medical devices and medical instrumentation for several decades. Flex circuits and flexible heaters can be ideal solutions in applications requiring lightweight, continuous movement, and highly reliable interconnections that are biocompatible. Recent material advancements have expanded the realm of flexible circuits to include applications in reusable (via sterilization) medical products. This advancement requires performance at higher temperature exposure with more robust material constructions to withstand autoclave sterilization vs. the more traditional polyimide constructions used in the industry.
Reusable medical products are devices or instruments that are reused to treat or diagnose patients and are considered part of three categories[1]:
- Critical devices, such as surgical forceps, which contact blood or normally sterile tissue.
- Semi-critical devices, such as endoscopes, which contact mucus membranes.
- Non-critical devices, such as stethoscopes, which contact unbroken skin.
Medical instrumentation must be adequately cleaned, sanitized and or sterilized before reuse. From an FDA standpoint clean, sanitize and sterilize have different meanings. Cleaning is defined as the visual removal of particulate matter. Sanitization refers to the reduction of micro-organisms to a specified acceptable level. Sterilization indicates a further level of cleanliness as the requirement is to remove all micro-organisms.
Health facilities employing cleaning processes for reusable devices must have FDA approval. The FDA requires the health care facility to validate its cleaning process. This validation must conform to FDA requirements listed here.
Among the requirements for reusable medical devices are written procedures detailing the cleaning processes, validation procedures, acceptance criteria and revalidation frequency. Additionally, sampling procedures and analytical methods need to be documented with details describing measurement sensitivity. A final validation report is generally required for the cleaning processing with data supporting the cleanliness conclusion[3]
In general, the validation of a cleaning process must demonstrate two outcomes:
- That the cleaning process will clean the instrument or device to an acceptable level.
- That the cleaning process will not degrade the performance of the device or instrument.
The FDA does not specify the parameters of a cleaning process, only that it is validated. However, standards have been developed by the Association for the Advancement of Medical Instrumentation (AAMI) and are recognized by the FDA. Many of these standards specify procedures, facilities, training of personnel and the equipment to be used for cleaning reusable medical products.
The most effective method to kill microorganisms is heat. Saturated steam pressure is one of the most common methods specified and has been in use for a long time in the medical industry. The autoclave is the most commonly used piece of equipment used for sterilization. An autoclave is essentially a sophisticated high-pressure cooker.
The autoclave cleaning sequence may include several pressurized steam cycles, followed by high heat and chemical vapor. The high heat cycle can reach 375°F for over 10 minutes[4]. This is where many typical flexible circuits would begin to degrade.
The flex circuit industry has developed material constructions that can survive temperatures in excess of 480°F and can withstand multiple sequences of autoclave cleaning processing. This material advancement allows flexible circuits to be increasingly adopted in reusable medical devices.
The flex circuit industry has provided products for many high reliability applications in the medical industry for over 20 years. Companies focused on business systems and creation of an operating culture are currently able to support development of new parts requiring sanitization and sterilization. Design guidelines and layout are similar to most polyimide circuit constructions, but part number nuance and material specific considerations are best coordinated by consultation with an applications engineer.
References
- “Reusable Medical Device Disinfection and Cleaning Validation Requirements,” by Steven Richter, PhD, 2011, Infection Control Today.
- USDA
- U.S. Food & Drug Administration Inspection Guides, Validation of Cleaning Processes (7/93).
- Autoclave Temperature and Time Pressure Chart, Alfa Medical Equipment.
- AAMI ST79 Comprehensive guide to steam sterilization and sterility assurance in health care facilities, Association for the Advancement of Medical Instrumentation (AAMI).
- “Autoclave Sterilization Process Guide,” Nov. 2015, Sterilization and Infection Control Blog.
- “Reprocessing of Reusable Medical Devices,” U.S. Food & Drug Administration.
- “Endoscope disinfection” by George Meyer, MD, UPToDate.com.
- “Cleaning and disinfection of equipment for gastrointestinal endoscopy,” BMJ Open Gastroenterology.
- “How to Sterilize Medical Instruments,” WikiHow.
Dave Becker is vice president of sales and marketing at All Flex Flexible Circuits LLC.
More Columns from All About Flex
All About Flex: Terms and ConditionsAll About Flex: ISO 9001 Basics
All About Flex: FAQs on UL Listings for Flexible Circuits
All About Flex: Avoiding Trace Fracturing in a Flexible Circuit
Polyimide vs. Silicone for Flexible Heaters
All About Flex: Copper Thickness Requirements for Flex Circuits
All About Flex: Copper Grain Direction
All About Flex: Options for Purchasing Flexible Heaters