-
- News
- Books
Featured Books
- smt007 Magazine
Latest Issues
Current IssueWhat's Your Sweet Spot?
Are you in a niche that’s growing or shrinking? Is it time to reassess and refocus? We spotlight companies thriving by redefining or reinforcing their niche. What are their insights?
Moving Forward With Confidence
In this issue, we focus on sales and quoting, workforce training, new IPC leadership in the U.S. and Canada, the effects of tariffs, CFX standards, and much more—all designed to provide perspective as you move through the cloud bank of today's shifting economic market.
Intelligent Test and Inspection
Are you ready to explore the cutting-edge advancements shaping the electronics manufacturing industry? The May 2025 issue of SMT007 Magazine is packed with insights, innovations, and expert perspectives that you won’t want to miss.
- Articles
- Columns
- Links
- Media kit
||| MENU - smt007 Magazine
Is Hybrid Technology Gaining Momentum?
October 2, 2017 | Dieter G. Weiss, Weiss EngineeringEstimated reading time: 3 minutes
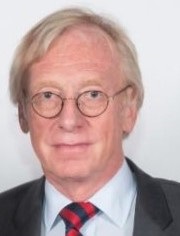
Over the past 20 years, ceramic hybrids have changed more and more to a backyard living in the European electronics industry. Price pressure, specifically from the automotive electronics industry, was the key reason. As long as the base materials for normal printed circuits were not able to comply with the high demands in regards to heat resistance and dimensional stability, the industry did not consider normal PCBs made of FR4 laminate a substitute for ceramic hybrids by the industry. The laminate industry, suffering from high price pressure as well, successfully worked on improving their products in order to expand the market for their products. They raised the glass transition temperature of the epoxy resins, improved the glass fabric in regards to dimensional stability and optimized the laminate pressing process for lower tolerances until the day, when the first Tier 1 supplier for the automotive industry exchanged the thick film hybrids in his products to ordinary FR4 PCBs.
This process took a long time, but when started, it was irreversible and led to a dramatic reduction in demand for thick film hybrids. The automotive market, still by far the biggest market for ceramic hybrids, caused the total European market to get into reverse gear. Purchasing managers in the automotive industry used this argument as well to put additional price pressure onto the hybrid manufacturers. As a result, some hybrid manufacturers closed, others changed hands and some extended their service offer to normal electronic manufacturing services using organic PCBs. Even this year, one hybrid manufacturer had to announce insolvency, while another one took the “Hybrid” out of his company name as he stopped selling hybrids. Today, there are about 56 hybrid manufacturers operating in Europe, of which 23 are located in Germany. OEMs and manufacturing service companies share the market, the bigger share (>50%) is owned by nine OEMs. The European market is about the size of the production value, as there are exports (USA and few to Asia) as well as imports (Japan and US).
To the young electronic designers, it needs to be explained that there is not only thick film technology in the hybrid industry. Thin film technology, allowing much denser structures than screen-printing with thick film metallic pastes, is an alternative as well as multilayer constructions where the circuitry is applied onto a green ceramic, which is finally sintered at high temperatures. The latter one is the king class in technology of hybrid circuitry, as it requires the green ceramic to shrink at a predefined percentage. Depending on the technology and sintering temperature, one differentiates between low temperature cofired ceramics (LTCC) and high temperature cofired ceramics (HTCC).
Temperatures of about 850°C for LTCC still allow the use of silver- or gold-pastes for the circuitry, whereas HTCC can only use molybdenum or tungsten pastes as the sintering operates at 1,600°C to 1,800°C. The last technology in hybrids is direct copper bonding (DCB). This technology uses ceramic as a base (either aluminum oxide, aluminum nitride or zirconia toughened alumina) onto which a copper layer is applied. The name for this product category originates from the direct application of copper onto the ceramic. There are different technologies to apply the copper. The copper is much thicker than in normal FR4 for organic PCBs, which use 18µm and 35µm as a standard, as high power applications use DCB. To get a circuit structure, the copper can be etched or be built with a galvanic process.
Today, thick film technology only counts for a little more than a third of the production of Hybrids, coming down from more than 50%. LTCC and HTCC take another third and thin film technology is still a niche with about 5%. The big winner in the hybrid industry is DCB. High-power applications in many industries are gaining market share, e.g. in the energy management for electrical cars. Can the hybrid industry take advantage of this development? While there are about 40 of the 56 European manufacturers working with thick film technology, only 12 have a share in DCB and those are mainly OEMs.
The suppliers for the hybrid manufacturers have seen this development very early, in specific the ceramic suppliers and the metal paste suppliers and stepped right into it. Today, they sell value-added products and are able to take advantage of this development. This only applies to the hybrid electronic manufacturing service companies. Lately, one of them told me that they see an increased demand for thick film products again, as well coming from the automotive industry. It waits to be seen whether this becomes a trend or not. Today, the European hybrid market still has a small production value with about €1.2 billion in revenues.
Suggested Items
The Evolution of Picosecond Laser Drilling
06/19/2025 | Marcy LaRont, PCB007 MagazineIs it hard to imagine a single laser pulse reduced not only from nanoseconds to picoseconds in its pulse duration, but even to femtoseconds? Well, buckle up because it seems we are there. In this interview, Dr. Stefan Rung, technical director of laser machines at Schmoll Maschinen GmbH, traces the technology trajectory of the laser drill from the CO2 laser to cutting-edge picosecond and hybrid laser drilling systems, highlighting the benefits and limitations of each method, and demonstrating how laser innovations are shaping the future of PCB fabrication.
Day 2: More Cutting-edge Insights at the EIPC Summer Conference
06/18/2025 | Pete Starkey, I-Connect007The European Institute for the PCB Community (EIPC) summer conference took place this year in Edinburgh, Scotland, June 3-4. This is the third of three articles on the conference. The other two cover Day 1’s sessions and the opening keynote speech. Below is a recap of the second day’s sessions.
Day 1: Cutting Edge Insights at the EIPC Summer Conference
06/17/2025 | Pete Starkey, I-Connect007The European Institute for the PCB Community (EIPC) Summer Conference took place this year in Edinburgh, Scotland, June 3-4. This is the second of three articles on the conference. The other two cover the keynote speeches and Day 2 of the technical conference. Below is a recap of the first day’s sessions.
Preventing Surface Prep Defects and Ensuring Reliability
06/10/2025 | Marcy LaRont, PCB007 MagazineIn printed circuit board (PCB) fabrication, surface preparation is a critical process that ensures strong adhesion, reliable plating, and long-term product performance. Without proper surface treatment, manufacturers may encounter defects such as delamination, poor solder mask adhesion, and plating failures. This article examines key surface preparation techniques, common defects resulting from improper processes, and real-world case studies that illustrate best practices.
RF PCB Design Tips and Tricks
05/08/2025 | Cherie Litson, EPTAC MIT CID/CID+There are many great books, videos, and information online about designing PCBs for RF circuits. A few of my favorite RF sources are Hans Rosenberg, Stephen Chavez, and Rick Hartley, but there are many more. These PCB design engineers have a very good perspective on what it takes to take an RF design from schematic concept to PCB layout.