-
- News
- Books
Featured Books
- pcb007 Magazine
Latest Issues
Current IssueInventing the Future with SEL
Two years after launching its state-of-the-art PCB facility, SEL shares lessons in vision, execution, and innovation, plus insights from industry icons and technology leaders shaping the future of PCB fabrication.
Sales: From Pitch to PO
From the first cold call to finally receiving that first purchase order, the July PCB007 Magazine breaks down some critical parts of the sales stack. To up your sales game, read on!
The Hole Truth: Via Integrity in an HDI World
From the drilled hole to registration across multiple sequential lamination cycles, to the quality of your copper plating, via reliability in an HDI world is becoming an ever-greater challenge. This month we look at “The Hole Truth,” from creating the “perfect” via to how you can assure via quality and reliability, the first time, every time.
- Articles
- Columns
- Links
- Media kit
||| MENU - pcb007 Magazine
Estimated reading time: 3 minutes
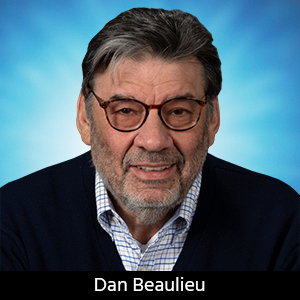
It’s Only Common Sense: Contract Manufacturing—Winning Those Big Accounts
Contract manufacturing is a service, not a product. As CEMs, we are building someone else’s product—someone else’s baby. Our customers are putting the fate of their companies in our hands. If we build the product incorrectly, our customers will be the ones to pay. They have their name on the product. They are responsible for designing, engineering, and marketing the products; we are responsible for the manufacturing of that product. Think about that for a moment. Consider how much trust comes into play when our customers decide to turn over the manufacturing of their products to our contract manufacturing services.
The decision to trust a CEM is a huge one for our customers. They must make sure that we are able to handle all their needs and have all the processes in place to deliver a product that is as good, if not better, than the one they themselves could produce, and at a better, more competitive price. So, these companies have two very difficult decisions to make: The first being if they should use a contract manufacturer in the first place; and the second, which contract manufacturer to select? As professional salespeople, this is where we come into the picture. It is our responsibility to convince our customers that they will be in good hands if they decided to trust our company with the fabrication of their product.
When you consider all the factors that go into a decision like this, it becomes evident that ours is not a simple sales process. It’s not merely holding up a product and giving a sales pitch for why the customer should buy it. This sales process is very personal—even emotional. In a way, it is almost like turning over your child to be raised by others.
When selling contract manufacturing services, as great salespeople, we should focus on making our customers feel completely comfortable, safe, and secure enough in our company to choose us to build their products. To do this, we must focus on the following key factors:
- Reliability: They need to understand that we are completely reliable. The best way to do this is through references and testimonials. They should be able to see a track record fully based on happy and satisfied customers—customers who are happy enough with our performance that they are willing to talk about it to other customers. If our target accounts see that we have customers who are willing to stand up and vouch for our reliability they will feel safe and secure in making their decision to engage with us.
- Consistency: When potential customers come to our company we must prove to them that our process is under control and that our production lines are putting out the same consistently high-quality products from the first assembly to the last. We must demonstrate that we have all the right systems, like ISO, in place, assuring them that we have a fool-proof quality assurance system.
- Credibility: It is key for customers to know that we are completely truthful in all our business transactions. This is the time for open-kimono discussions. We should concentrate on showing them that we are a real, viable, and financially sound company that will not only be there for them today, but in the future as well.
- Flexibility: This is so very important. As a CEM, you are literally their business partner in a relationship that is much more intense than the typical vendor/customer relationship. As a great CEM partner, you must always have the customer’s welfare at heart, realizing that you are playing an integral part in their success as well as yours. You have to always be prepared to walk that extra mile to assure that your customers are selling the best products money can buy, products that your company is producing for them.
As a salesperson, it is your responsibility to convey all these points to your customers, to assure them that your company will indeed treat them as true partners. But you cannot do it alone. The most important thing to remember about selling contract manufacturing services is that the entire team must be involved in the sale. From the company owner, president, program managers, quality managers, and department leads, down to the all-important purchasing manager, everyone should take part in convincing your customers that your company is unquestionably the most qualified, reliable, consistent, credible, flexible, and capable company in the industry to build their products.
It’s only common sense.
More Columns from It's Only Common Sense
It’s Only Common Sense: 20 Lessons in 20 Years—A Career in Common SenseIt’s Only Common Sense: Why Failure Is an Opportunity for Growth
It’s Only Common Sense: Stop Chasing New Customers and Start Keeping the Ones You Have
It’s Only Common Sense: Sales as a Team Sport
It’s Only Common Sense: How to Win Back Lost Customers
It’s Only Common Sense: Knowing When to Walk Away
It’s Only Common Sense: Customer Service Is Sales in Disguise
It’s Only Common Sense: Your Guide to Better Time Management