-
- News
- Books
Featured Books
- smt007 Magazine
Latest Issues
Current IssueWhat's Your Sweet Spot?
Are you in a niche that’s growing or shrinking? Is it time to reassess and refocus? We spotlight companies thriving by redefining or reinforcing their niche. What are their insights?
Moving Forward With Confidence
In this issue, we focus on sales and quoting, workforce training, new IPC leadership in the U.S. and Canada, the effects of tariffs, CFX standards, and much more—all designed to provide perspective as you move through the cloud bank of today's shifting economic market.
Intelligent Test and Inspection
Are you ready to explore the cutting-edge advancements shaping the electronics manufacturing industry? The May 2025 issue of SMT007 Magazine is packed with insights, innovations, and expert perspectives that you won’t want to miss.
- Articles
- Columns
- Links
- Media kit
||| MENU - smt007 Magazine
Moving Toward the Zero-Defect Line
October 24, 2017 | Stephen Las Marias, I-Connect007Estimated reading time: 7 minutes
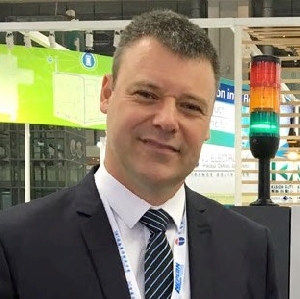
For this month’s issue of SMT Magazine, I interviewed Olivier Pirou, Chief Operating Officer of Vi TECHNOLOGY, during the NEPCON South China exhibition in Shenzhen to learn more about achieving the perfect solder joint from the point of view of an inspection systems provider, and how manufacturers can strategize to achieve a zero-defect line.
Stephen Las Marias: Olivier, from your perspective as an inspection technology provider, what should a perfect solder joint look like?
Olivier Pirou: We have an IPC standard describing what is the acceptable quality level of a soldered joint, and more generally speaking, what is a good printed circuit assembly. Beyond the quality aspects, especially in very stringent environments such as automotive or harsh industrial conditions, your solder joint will need to be the most reliable possible. It’s a combination of geometrical features, and mechanical structure of the long-term reliabilities in a joint.
Las Marias: What are the parameters for perfect and/or reliable solder joints?
Pirou: Many parameters are involved in the printing process, the pick-and-place process, the reflow process, to make the perfect assembly. All those conditions are even getting more complex, where a lot of different materials are involved, being consumables or component supplies, and operating conditions within the factories that are different from one to another. The approach that Vi TECHNOLOGY is taking to enable the zero-defect line – we should probably say the Six Sigma line – is to make sure that each individual process operates within controlled process limits. For that, we need outstanding Quality sensors, I would call them, after each process—the printing process, the pick-and-place process, and the reflow process, to make sure that all the relevant parameters are monitored, all the processes have a closed loop to make sure that any deviations in the process are caught before the defect appears, and that this is sufficiently agile for the line operator and line supervisor to use. By outstanding quality sensors, we also mean an SPI/AOI inspection that has no noise: no machine noise (often referred to as false calls) or human noise often referred to as (false accepts).
In addition to making sure that each individual process is and stays within control, we add a smart layer that is the combination of information of quality sensors to remove the noise and ultimately add onto the test and quality.
This is really what we’re aiming at quite successfully with our 3D SPI, 3D AOI and SIGMA LINK Suite —offering quality sensor excellence through very easy to use and automated equipment, capturing the entire defect spectrum of the processes, making sure that we take most of the correlation between printing, pick-and-place, and reflow process to operates within the Six Sigma boundaries.
Las Marias: Is it like the Industry 4.0 approach?
Pirou: Exactly. With Industry 4.0, you have the combination of horizontal and vertical communication. What we just described is the horizontal approach. Then you have the vertical integration, which ensures that if any of the deviation is occurring within the line, you have a strict control of what needs to happen. If something goes wrong, you have the connection with the MES to decide. The idea is, within that information hub, to link up horizontally in the line and vertically towards MES or other customer systems to have smarter operations.
Las Marias: Olivier, what soldering problems continue to persist?
Pirou: Miniaturization is in there. The printing process has its challenges with the increasing miniaturization, and more complex assembly processes, so we still see soldering issues. 3D SPI today is making even more sense in this type of environment. But the same is true for pick-and-place and reflow because the components that are placed are very different from one another. These, and various applications that are requiring, even for the end customer, increased integration. The end device is getting smaller as well, and on top of all that, the Z-dimension is getting even more important—even critical—in some environments. Critical measures for X, Y, theta, and Z in the automotive environment, for instance, are very important. The automated optical metrology has never been so justified.
Las Marias: Is having an X-ray capability important nowadays?
Pirou: Indeed, it’s getting important. It always has been important in the failure analysis, but most of the problems are consequences of up-front processes that have not been under control. To us, making sure that all individual processes are operating within the limits, that were set to have a good assembly, are essential. In that case, you can probably avoid a lot of downstream controls. Seeing the voids at X-ray doesn’t help very much. The real key is to avoid voiding.
But the X-ray can build redundancy in the quality control chain especially when it is intelligently coupled with AOI or SPI technologies. But again, we believe that it’s a process-by-process approach combined to have greater control. We don’t believe that there is one single point inspection strategy or electrical test strategy that would replace or be superior to all the others.
Las Marias: Definitely, collaboration is important.
Pirou: Collaboration is important. You see the whole industry moving to greater connection. there’s this Industry 4.0 global initiative that now leads all equipment manufacturers to link together.
Las Marias: Olivier, can you explain some of the latest innovations from Vi TECHNOLOGY that would help customers ensure that their solder paste and solder joints are reliable or perfect?
Pirou: Sure. As you know, with our PI Series system, we’re leading the way in fully automated 3D solder paste inspection. I think PI really offers superior value in terms of ease of use with unmatched metrology capabilities. Because beyond the quality of the metrology, of the machine, what we embed in that is really the ease of use. It’s an auto-programming machine. We’re going also in that direction for 3DAOI. Because most of the players will go to a fully-automated line, nobody really cares to program an SPI machine or an AOI machine or an X-ray machine. If it’s auto-programmed, if the limits are well set, if we have a mechanism to stay within process limit boundaries, it would save a lot of time and cost to our customers and, at the end of the day, increase quality.
This is what we do with PI. Of course, the same applies to the 3D AOI that we’ve introduced last year. The main innovation that we’ve brought to NEPCON is Sigma Line, and this is the correlation between 3D SPI and 3D AOI, to make sure that we have a mechanism to auto-adjust tolerances between all inspection sensors in the line.
Las Marias: It’s like one, smart loop?
Pirou: Yes. Closed loop at the process steps, and a smarter loop linking all the quality sensors together in the line, which are 3D SPI, 3D AOI, pre-reflow, and post-reflow.
Las Marias: There are still companies who are using 2D AOI and 2D SPI. How do you encourage them, and what is the justification for them, to move to 3D technology?
Pirou: At the end of the day, it’s all about customer requirements and test coverage. There is not always a reason to exclude 2D to 3D. All the players are using mathematical algorithms that are a combination of both. 3D is a great enabler to simplify programming and to expand test coverage, but this shouldn’t be at the expense of a lower 2D capability. If you take the example of, for instance, the lighting automotive industry, they have very critical 2D measurements to make sure that the optical path of the LED is well aligned. A centroid is compared to other features on the board, being a point, being a line, or whatever, with advanced metrology capabilities, you can achieve the accuracy and the reliability required for such applications. As I said, the best technologies today are combining the best of both worlds to serve the customer requirements for what is critical to the process and critical to the end-user application.
Las Marias: Over the past few years, we’ve talked to a lot of people and companies, and everyone’s very optimistic. They’re saying that last year there was a downturn, but at the end of last year it started picking up, and this year growth is continuing. Are you also experiencing it on your side?
Pirou: Yes. We see, as far as inspection is concerned, that this is one of the best ways today to guarantee quality at individual process steps. This is creating value for customers. Everybody wants to move towards the Six Sigma line. Inspection is a great enabler, and yes, we see that we are one of the few to really contribute to that better yield enhancement with customers.
Las Marias: Is there anything else we should be talking about?
Pirou: Moving towards the Six Sigma line in an ever-smarter factory is a very exiting topic. The world is moving fast in that direction which makes our industry much more interesting.
Las Marias: Thank you very much, Olivier.
Pirou: Thank you for your time.
Suggested Items
Driving Innovation: Direct Imaging vs. Conventional Exposure
07/01/2025 | Simon Khesin -- Column: Driving InnovationMy first camera used Kodak film. I even experimented with developing photos in the bathroom, though I usually dropped the film off at a Kodak center and received the prints two weeks later, only to discover that some images were out of focus or poorly framed. Today, every smartphone contains a high-quality camera capable of producing stunning images instantly.
Hands-On Demos Now Available for Apollo Seiko’s EF and AF Selective Soldering Lines
06/30/2025 | Apollo SeikoApollo Seiko, a leading innovator in soldering technology, is excited to spotlight its expanded lineup of EF and AF Series Selective Soldering Systems, now available for live demonstrations in its newly dedicated demo room.
Indium Corporation Expert to Present on Automotive and Industrial Solder Bonding Solutions at Global Electronics Association Workshop
06/26/2025 | IndiumIndium Corporation Principal Engineer, Advanced Materials, Andy Mackie, Ph.D., MSc, will deliver a technical presentation on innovative solder bonding solutions for automotive and industrial applications at the Global Electronics A
Fresh PCB Concepts: Assembly Challenges with Micro Components and Standard Solder Mask Practices
06/26/2025 | Team NCAB -- Column: Fresh PCB ConceptsMicro components have redefined what is possible in PCB design. With package sizes like 01005 and 0201 becoming more common in high-density layouts, designers are now expected to pack more performance into smaller spaces than ever before. While these advancements support miniaturization and functionality, they introduce new assembly challenges, particularly with traditional solder mask and legend application processes.
Knocking Down the Bone Pile: Tin Whisker Mitigation in Aerospace Applications, Part 3
06/25/2025 | Nash Bell -- Column: Knocking Down the Bone PileTin whiskers are slender, hair-like metallic growths that can develop on the surface of tin-plated electronic components. Typically measuring a few micrometers in diameter and growing several millimeters in length, they form through an electrochemical process influenced by environmental factors such as temperature variations, mechanical or compressive stress, and the aging of solder alloys.