-
- News
- Books
Featured Books
- smt007 Magazine
Latest Issues
Current IssueWhat's Your Sweet Spot?
Are you in a niche that’s growing or shrinking? Is it time to reassess and refocus? We spotlight companies thriving by redefining or reinforcing their niche. What are their insights?
Moving Forward With Confidence
In this issue, we focus on sales and quoting, workforce training, new IPC leadership in the U.S. and Canada, the effects of tariffs, CFX standards, and much more—all designed to provide perspective as you move through the cloud bank of today's shifting economic market.
Intelligent Test and Inspection
Are you ready to explore the cutting-edge advancements shaping the electronics manufacturing industry? The May 2025 issue of SMT007 Magazine is packed with insights, innovations, and expert perspectives that you won’t want to miss.
- Articles
- Columns
- Links
- Media kit
||| MENU - smt007 Magazine
Choosing Solder Processes: Getting It Right
October 25, 2017 | Stephen Las Marias, I-Connect007Estimated reading time: 6 minutes
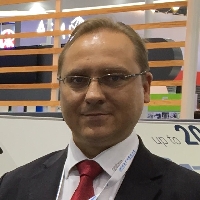
To find out more about achieving the perfect solder joint, I interviewed Ralf Wagenfuehr, plant manager at Rehm Thermal Systems, during the recent NEPCON South China exhibition in Shenzhen to get his insights on this issue from the perspective of a reflow oven supplier.
Stephen Las Marias: Ralf, why do you think solder joints are among the key factors in PCB defects?
Ralf Wagenfuehr: It all comes down to the solder joint. It’s getting (the components) connected to the board. The other factors are based on the suppliers, the components, the PCBs, etc. I think the solder joint is the main purpose of the whole SMT industry. Everything else is easy to control, but bringing them together, it is important to have the correct parameters in there.
Las Marias: How would you define or characterize a perfect solder joint?
Wagenfuehr: A perfect solder joint, we believe, can be only achieved in the nitrogen atmosphere. You don’t look only at when it’s connected, you have to look at the next 10 years, where the end-user is using the product continuously. The perfect solder joint is reliable, and I think the important thing is it has a clear surface, that it’s not impacted, and that there are no corrosions, among other things. While a good connection on the surface is very important, you also must make sure the joints are stable.
Las Marias: Why do you need a nitrogen environment?
Wagenfuehr: In a nitrogen environment, you can exclude oxygen already, so mostly, you would achieve better wetting. Sure, it depends on the paste, but I believe reliable solder joints can be achieved under a nitrogen atmosphere. That’s why we designed nitrogen ovens.
Las Marias: What are the parameters to consider for achieving the perfect solder joint?
Wagenfuehr: The main ingredient is the solder paste, and it is important for material surfaces. You have different components and different surfaces for different customer requests. That’s why choosing the right paste for the right components is one of the most important things.
Next is the customer’s temperature ranges for the components in PCBs. There’s a wide range of applications. Some cannot have nitrogen, some need nitrogen. The solder paste is very important, but connecting the components to the board is a process that influences the long-term reliability of the parts themselves.
Las Marias: It’s important that the paste supplier, the assembler, equipment supplier, and customer are all working together.
Wagenfuehr: Yes, that’s very important. If you choose the wrong surface finish, then you will have defects built in from the beginning. That will cause defects on a long-term view. Of course, most people are already considering this. But I think it’s very important to have the right paste.
Las Marias: Ralf, what are the other soldering issues from your perspective?
Wagenfuehr: Wrong profiling is one. We still see people doing wrong profiling. Wrong designs and wrong storages are the other issues. Design has a big influence. We have a lot of engineers working together, we have a lot of components, solder paste, solder pads, so the design (of the board) has a really big impact. Wrong storage (of solder paste) is also one of the biggest culprits.
Las Marias: Why is voiding a big issue right now?
Wagenfuehr: Things are getting more compact, and the power usage is getting higher. We have more applications running on a smaller surface. That means everything is consuming more power, even on the PCB. Of course, in applications such as automotive, medical, and other critical industries, it can cost lives. You don’t want a PCB to break down on the airplane when you’re in it. Your mobile phone breaks down, it’s a quality issue; you can make a decision in the future. But for other things, you only have one chance to make it right. As things become smaller, more compact, with more built-in functions into the circuits, and into the components, it is important to have less soldering voids.
Las Marias: How do you help customers address their voiding problem?
Wagenfuehr: We have the main systems, including our condensation soldering, our vacuum soldering, and vacuum reflow. But we also have a whole process chain that we can support. Our customers call us not only for voiding but mainly also for this, and how we can support them is through our process chain. Here, the design is one of the main factors for the voiding. The design often is the wrong choice. Things cannot escape, and air cannot escape. The soldier joint is the wrong size, or has the wrong pad. We have to design it with some holes so air can escape from the solder pad. Of course, the printing process is very important. How we pressurize the components on the solder pad itself is very important. We have done studies, and we figured that with an improved process, you can nearly achieve around 20% or less in higher applications, but of course, if you can control all your factors with our systems, you can go down to 2% voiding.
Las Marias: What are the key considerations to achieve this?
Wagenfuehr: Atmosphere is one of the factors that have an impact on the process. For instance, you have less oxygen when the solder melts. It’s important to have the right surrounding atmosphere. The process must be seen as a whole process chain to avoid voiding. We have trained process engineers at all locations, and we can support on the process chain as well. This is why Rehm is very strong—not only for making machines, but by being able to support the process chain as well.
Page 1 of 2
Suggested Items
Driving Innovation: Direct Imaging vs. Conventional Exposure
07/01/2025 | Simon Khesin -- Column: Driving InnovationMy first camera used Kodak film. I even experimented with developing photos in the bathroom, though I usually dropped the film off at a Kodak center and received the prints two weeks later, only to discover that some images were out of focus or poorly framed. Today, every smartphone contains a high-quality camera capable of producing stunning images instantly.
Hands-On Demos Now Available for Apollo Seiko’s EF and AF Selective Soldering Lines
06/30/2025 | Apollo SeikoApollo Seiko, a leading innovator in soldering technology, is excited to spotlight its expanded lineup of EF and AF Series Selective Soldering Systems, now available for live demonstrations in its newly dedicated demo room.
Indium Corporation Expert to Present on Automotive and Industrial Solder Bonding Solutions at Global Electronics Association Workshop
06/26/2025 | IndiumIndium Corporation Principal Engineer, Advanced Materials, Andy Mackie, Ph.D., MSc, will deliver a technical presentation on innovative solder bonding solutions for automotive and industrial applications at the Global Electronics A
Fresh PCB Concepts: Assembly Challenges with Micro Components and Standard Solder Mask Practices
06/26/2025 | Team NCAB -- Column: Fresh PCB ConceptsMicro components have redefined what is possible in PCB design. With package sizes like 01005 and 0201 becoming more common in high-density layouts, designers are now expected to pack more performance into smaller spaces than ever before. While these advancements support miniaturization and functionality, they introduce new assembly challenges, particularly with traditional solder mask and legend application processes.
Knocking Down the Bone Pile: Tin Whisker Mitigation in Aerospace Applications, Part 3
06/25/2025 | Nash Bell -- Column: Knocking Down the Bone PileTin whiskers are slender, hair-like metallic growths that can develop on the surface of tin-plated electronic components. Typically measuring a few micrometers in diameter and growing several millimeters in length, they form through an electrochemical process influenced by environmental factors such as temperature variations, mechanical or compressive stress, and the aging of solder alloys.