-
- News
- Books
Featured Books
- smt007 Magazine
Latest Issues
Current IssueWhat's Your Sweet Spot?
Are you in a niche that’s growing or shrinking? Is it time to reassess and refocus? We spotlight companies thriving by redefining or reinforcing their niche. What are their insights?
Moving Forward With Confidence
In this issue, we focus on sales and quoting, workforce training, new IPC leadership in the U.S. and Canada, the effects of tariffs, CFX standards, and much more—all designed to provide perspective as you move through the cloud bank of today's shifting economic market.
Intelligent Test and Inspection
Are you ready to explore the cutting-edge advancements shaping the electronics manufacturing industry? The May 2025 issue of SMT007 Magazine is packed with insights, innovations, and expert perspectives that you won’t want to miss.
- Articles
- Columns
- Links
- Media kit
||| MENU - smt007 Magazine
DFx on High-Density Assemblies
December 1, 2017 | Jonas Sjoberg, Chris Nash, David Sbiroli, and Wisdom Qu, Indium CorporationEstimated reading time: 4 minutes
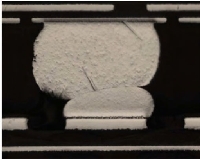
There are many ways to increase packaging density. Examples of technologies include fine-pitch connectors, package-on-package (PoP), fine pitch CSPs, 01005, 0201, and reduced component- to-component spacing.
Use of new technologies poses a number of challenges for solder paste selection, PCB design, assembly process, and reliability. The type of end product will have different challenges, concerns, and requirements in all aspects. The assembly line for many of these end products will look very similar, but specification limits would be different. Typical reliability tests are drop test, vibration, thermal cycling test (TCT), and SIR; even if the names of the tests are the same, the pass/fail criteria vary between different end products.
When it comes to material selection—and solder paste in particular—the type of end product plays a big role. An automotive, computing server, or router product would, in many cases, require an in-circuit test (ICT); thereby, the solder paste residues must be easy to penetrate with a test probe. A consumer product, on the other hand, typically doesn’t focus on ICT. The concern is more on throughput, thereby requiring a solder paste that is capable of fast screen printing.
There are many more examples, but with the increased need for high-density assembly, most, if not all, solder pastes must be able to print well on stencil apertures with area ratios (AR) way below the typical industry standard of 0.66. The AR for some products could be as low as 0.5-.55.
With the above challenges, finer solder powder is increasingly being used, and the type of solder powder is moving from type 3 towards type 4-4.5, and even type 5 for a number of applications. This poses some new challenges. In addition, low-silver and low-temperature alloys are gaining traction, making the selection of solder pastes and alloys more complex.
Once the correct solder paste material is selected, a feasible and robust assembly process must be developed and sustained. The assembly process ranges from screen-printing, placement, and reflow soldering in air or nitrogen to electrical and functional testing. Many factors influence the quality of the assembly process. With the reduced pitch and component spacing, the capabilities for solder paste, assembly, and PCB fabrication will be tested to its limits and beyond, with the need for using statistical tools is becoming a requirement to develop and maintain good yields.
Even with the right solder paste selection, good assembly process, and high-quality PCB and components, failures still will occur, leading to yield losses and extra cost. Once these failures occur, it is very easy to jump to conclusions and start making changes without knowing the root cause of the failure. As engineers, we quite often tend look for the most difficult solution, but in many cases, the simple solution is the right solution to solve the issue.
PCB and PCBA Design
When moving to high-density assembly, it is very important to understand PCB design and its limitations. With increasing density, the PCB fabrication becomes much more challenging. Some of the key PCB design requirements include:
• 50 μm copper/copper spacing (inner and outer layers)
• 50 μm solder mask slivers
• 25-40 μm solder mask registration tolerance
• 60 μm microvias
• 200 μm microvia capture pads in outer and inner layers
Understanding DFx and design is in many cases critical to be able to identify the root cause of the issues that occur on the production line. When it comes to PCB and PCBA design, there are many important aspects. In this paper, we have selected a few that have a critical impact on SPI and overall yields.
• PCB stretch and shrink
• Filled vs. unfilled microvias
• Silkscreen
PCB Stretch and Shrink
The maximum PCB stretch is 0.05 mm over the entire panel, and this must be clearly specified on the PCB fabrication drawing. This is very important for fine-pitch parts and high-density spacing products. The pads and apertures for 01005 passives and 0.3 mm pitch CSPs is 0.2 mm; a stretch or shrink of more than 0.05 mm leads to solder paste that will be 25% of the pad.
Microvia Issue
Excessive voids in some cases lead to solder bridging. This could be caused by oversized or "leaking" microvias in pad in combination with normal process variations. An issue on a smartphone can be seen below; failure rate for bridging was 6% in this case (Figure 2).
One primary issue today is that there are no clear specifications as to how big the microvias are allowed to be or where to measure the actual size of the microvia (Figure 4). Since there is no clear specification, the microvias can look different in size and shape between different suppliers and between batches of PCBs.
By filling the microvias with copper in the PCB fabrication process, the voids and bridging issues can be eliminated.
Silkscreen Issue
Depending on the quality of the silkscreen, the height on top of the solder mask could range from 15-40 μm. This can create a gap between the stencil and PCB of 15-40 μm, depending on the PCB design. The gap can create printing issues leading to both too little or too much solder paste height and volume. Depending on the design of a product, the solder mask can add 10-25 μm in addition to the silkscreen, creating a gap of 15-65 μm from the bottom of the stencil to the pad.
In this case, the top of the solder mask is 422 μm on top of the copper pad.
When the stencil is placed on top of the PCB, the effect of the silkscreen becomes very visible graphically. By looking at the SPI data, it becomes very clear that it can have a big impact on SPI yields, and potentially overall yields.
To read the full version of this article, which appeared in the November 2017 issue of SMT Magazine, click here.
Suggested Items
Driving Innovation: Direct Imaging vs. Conventional Exposure
07/01/2025 | Simon Khesin -- Column: Driving InnovationMy first camera used Kodak film. I even experimented with developing photos in the bathroom, though I usually dropped the film off at a Kodak center and received the prints two weeks later, only to discover that some images were out of focus or poorly framed. Today, every smartphone contains a high-quality camera capable of producing stunning images instantly.
Hands-On Demos Now Available for Apollo Seiko’s EF and AF Selective Soldering Lines
06/30/2025 | Apollo SeikoApollo Seiko, a leading innovator in soldering technology, is excited to spotlight its expanded lineup of EF and AF Series Selective Soldering Systems, now available for live demonstrations in its newly dedicated demo room.
Indium Corporation Expert to Present on Automotive and Industrial Solder Bonding Solutions at Global Electronics Association Workshop
06/26/2025 | IndiumIndium Corporation Principal Engineer, Advanced Materials, Andy Mackie, Ph.D., MSc, will deliver a technical presentation on innovative solder bonding solutions for automotive and industrial applications at the Global Electronics A
Fresh PCB Concepts: Assembly Challenges with Micro Components and Standard Solder Mask Practices
06/26/2025 | Team NCAB -- Column: Fresh PCB ConceptsMicro components have redefined what is possible in PCB design. With package sizes like 01005 and 0201 becoming more common in high-density layouts, designers are now expected to pack more performance into smaller spaces than ever before. While these advancements support miniaturization and functionality, they introduce new assembly challenges, particularly with traditional solder mask and legend application processes.
Knocking Down the Bone Pile: Tin Whisker Mitigation in Aerospace Applications, Part 3
06/25/2025 | Nash Bell -- Column: Knocking Down the Bone PileTin whiskers are slender, hair-like metallic growths that can develop on the surface of tin-plated electronic components. Typically measuring a few micrometers in diameter and growing several millimeters in length, they form through an electrochemical process influenced by environmental factors such as temperature variations, mechanical or compressive stress, and the aging of solder alloys.