-
- News
- Books
Featured Books
- pcb007 Magazine
Latest Issues
Current IssueIn Pursuit of Perfection: Defect Reduction
For bare PCB board fabrication, defect reduction is a critical aspect of a company's bottom line profitability. In this issue, we examine how imaging, etching, and plating processes can provide information and insight into reducing defects and increasing yields.
Voices of the Industry
We take the pulse of the PCB industry by sharing insights from leading fabricators and suppliers in this month's issue. We've gathered their thoughts on the new U.S. administration, spending, the war in Ukraine, and their most pressing needs. It’s an eye-opening and enlightening look behind the curtain.
The Essential Guide to Surface Finishes
We go back to basics this month with a recount of a little history, and look forward to addressing the many challenges that high density, high frequency, adhesion, SI, and corrosion concerns for harsh environments bring to the fore. We compare and contrast surface finishes by type and application, take a hard look at the many iterations of gold plating, and address palladium as a surface finish.
- Articles
- Columns
Search Console
- Links
- Media kit
||| MENU - pcb007 Magazine
Estimated reading time: 2 minutes
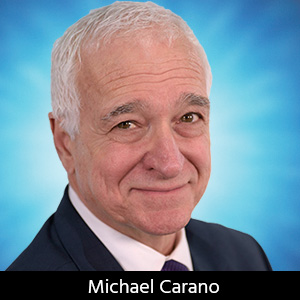
Contact Columnist Form
Trouble in Your Tank: Moving into Microvias—The Interaction of Materials and Processes, Part 2
Introduction
For the fabricator to successfully implement an HDI strategy, several new competencies must be acquired. These competencies include:
- Material selection
- Small diameter via formation
- Fine line imaging and etching
- Via filling technology
- Improved registration
- Enhanced bonding strength for the sub-laminations
- Metallization technology
These topics will be presented in more detail in this and future columns. But first, a short discussion on materials for HDI is warranted.
Materials
Most of the dielectric materials that are used to make printed circuit boards incorporate reinforcement into the resin system. Reinforcement usually takes the form of woven glass fiber. Woven fiberglass is just like any other cloth, made up of individual filaments that are woven together on a loom. By using different diameter filaments, different yarn bundle sizes and different weave patterns, different styles of glass cloth are created. Woven glass fabric adds both dimensional stability and thermal durability to the dielectric, but it does present some problems when used in HDI constructions.
Materials selection is equally as important, especially due to the higher temperatures of lead-free assembly and their subsequent effect on laminate delamination and reliability. Important new capabilities to embrace are:
- Impedance calculations and stackups for high-frequency boards using coplanar waveguides and coplanar stripline models
- Characteristics and scaling/feature compensation for the newer phenolic-epoxy and halogen-free FR-4s
- Ability to add local fiducials to align laser drilling CCD cameras
- System to store laser drilling parameters based on diameter, depth, and material types
- Characteristics of via-plugging to determine if placement of buried vias will create problems
Via Formation
When lasers are used to create vias, the difference in ablation rates between the glass fiber and the surrounding resin can cause poor hole quality. Also, the fiberglass cloth is not uniform due to having areas with no glass, areas with one strand, and the intersections of strands (also known as knuckles), making it difficult to set up drilling parameters for all these varying materials. Usually the drilling is set up for the hardest to drill region which is the knuckle area. Figure 1 shows some examples of poor hole quality due to laser ablation of glass fiber reinforced dielectrics. It seems many fabricators opt to not employ a glass etch in these types of conditions. A properly controlled glass etch will aid in removing the protruding glass fiber bundles and enhance overall plating uniformity.
When migrating HDI manufacturing over to laser-drillable prepregs, improvement in via quality is achievable. These laser-drillable prepregs are made using spread yarns in both the warp and fill directions. Thus the reinforcement is more uniform helping to minimize the areas with no glass fiber, as well as the knuckle area.
To read the full version of this article which appeared in the November 2017 issue of The PCB Magazine, click here.
Related Article:
Trouble in Your Tank: Moving into Microvias—The Interaction of Materials and Processes, Part 1
More Columns from Trouble in Your Tank
Trouble in Your Tank: Yield Improvement and ReliabilityTrouble in Your Tank: Causes of Plating Voids, Pre-electroless Copper
Trouble in Your Tank: Organic Addition Agents in Electrolytic Copper Plating
Trouble in Your Tank: Interconnect Defect—The Three Degrees of Separation
Trouble in Your Tank: Things You Can Do for Better Wet Process Control
Trouble in Your Tank: Processes to Support IC Substrates and Advanced Packaging, Part 5
Trouble in Your Tank: Materials for PWB Fabrication—Drillability and Metallization
Trouble in Your Tank: Supporting IC Substrates and Advanced Packaging, Part 5