-
- News
- Books
Featured Books
- smt007 Magazine
Latest Issues
Current IssueWhat's Your Sweet Spot?
Are you in a niche that’s growing or shrinking? Is it time to reassess and refocus? We spotlight companies thriving by redefining or reinforcing their niche. What are their insights?
Moving Forward With Confidence
In this issue, we focus on sales and quoting, workforce training, new IPC leadership in the U.S. and Canada, the effects of tariffs, CFX standards, and much more—all designed to provide perspective as you move through the cloud bank of today's shifting economic market.
Intelligent Test and Inspection
Are you ready to explore the cutting-edge advancements shaping the electronics manufacturing industry? The May 2025 issue of SMT007 Magazine is packed with insights, innovations, and expert perspectives that you won’t want to miss.
- Articles
- Columns
- Links
- Media kit
||| MENU - smt007 Magazine
Equipment Matters in Solder Paste Printing
December 6, 2017 | Stephen Las Marias, I-Connect007Estimated reading time: 6 minutes
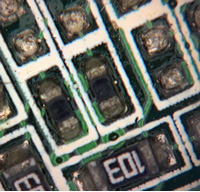
The solder paste printing process has always been considered a major contributor to yield loss. According to many studies, solder paste printing accounts for up to 70% of all PCB assembly defects.
For the December 2017 issue of SMT Magazine, we interviewed experts in the solder paste printing process to learn more about the key issues leading to this huge percentage of defects, and the technology developments that are addressing these challenges and improving yields in the process. These experts, including Tim O’Neill, technical marketing manager for AIM Solder; Edward Stone, sales manager at Manncorp; and Lenthor Engineering’s Dave Moody and Matt Kan, director of sales and marketing, and EMS manager, respectively, provided their insights from the perspective of a solder paste supplier, an equipment manufacturer, and a PCB assembler.
Lenthor Engineering’s Kan says 99% of the time they mostly deal with flex and rigid-flex assemblies, so it’s a whole different environment than rigid: “I can only speak from my personal experience. When I tried to deploy process steps that I used for rigid, I found out quickly most of the time, it didn’t work for the flex and the rigid-flex world. With flex and rigid flex, any kinks from one area to the next, you get misprints, even if your fixture your board correctly. Another option is to array with support tabs to keep the board as flat as possible. Since we design, fabricate and assemble under one roof, we have the advantages of deciding which method is the most cost effective,” explains Kan. “With the flex and the rigid-flex, you have to tweak your printing parameters because everyone knows a flat surface is crucial; and dealing with flex, you have different thicknesses, so your typical 5 mils stencil for rigid doesn’t always apply in the flex circuit world. Our standard is 3 mils; we change up or down in foil thickness as we see fit, step down, back etched, etc. Printing problems that we encounter is either not enough or too much paste. As things get smaller and smaller, we would switch from Type 3 to Type 4 for the smaller 0201 or 01005 components.”
From a solder supplier’s perspective, one of the key challenges is the ever-shrinking solder deposit, and the challenges that it introduces to the printing process. “When we got into the business 20 years ago, the smallest component that you saw in practice was an 0603; 0402 was still theoretical. Now, we’re talking about 08005s, sub-miniature and below the visual threshold. This not only causes significant challenges to the printing process, but downstream processes as well,” explains O’Neill. “With regard to print defects, the area ratio or the thickness of the stencil as it relates to the size of the hole in the stencil is a critical parameter and we are confronted with apertures that are as tall as they are wide. Getting solder paste out of that aperture consistently and repeatedly is becoming more challenging because the ratios are becoming inverted. A 0.66 area ratio was considered the finest area ratio that was practical in a production environment; now, I would estimate a 0.5 area ratio is becoming more commonplace due to advancements both in solder paste technology, as well as complementary technologies, including hardware, stencil coatings, etc. The technology involved in paste printing is moving forward and giving assemblers more tools in their toolbox to address fine feature print challenges. Matt's situation with flex circuits inherently produces more variability than somebody assembling rigid circuit boards might have, so he's got an even bigger challenge in addressing consistency in his process.”
O’Neill says consistency and overall volume are the two most important variables that they are focusing on to help assemblers improve transfer efficiency. “Not only do we want to get as much solder paste through that aperture as we can, we want to get it through as repeatedly as we possibly can,” he says.
In order to do that, solder paste rheology is evolving. Typically, as the viscosity gets lower, solder pastes become creamier. “It doesn’t take a genius to see how a solder paste that is more fluid and less viscous is going to be easier to pass through the aperture.” says O’Neill. “The problem this creates is that, when the stencil is removed, the deposit must maintain its shape or it would bridge, slump and cause other bridging and solder beading problems. Lowering viscosity alone, while it may improve transfer efficiency, won’t necessarily improve consistency. Pad design, board design—there’s a host of variables that need to be considered, board support being a big one—something the Lenthor guys building rigid-flex know better than anyone. Getting solder paste through an aperture is one thing, getting it through the apertures consistently is another. The advent of solder paste inspection (SPI) equipment has given the assembler the ability to measure every single deposit on that board in real time. This is especially critical now that we’re reaching the visual threshold for solder deposits. SPI gives assemblers the ability to analyze, in real time, every deposit made on a circuit board. SPI closes the feedback loop so that the process engineers and supervisors can make sure the print process is well within the defined parameters.”
Equipment Perspective
Manncorp often deals with a lot of OEMs and companies that are just getting into their first SMT line and developing their own in-house capability. “It’s our job to suggest the appropriate equipment to be able to build the boards that the customer is looking to do,” says Stone.
Because of the nature of the customers and economics—wanting to save money where they can—they always feel that the stencil printer is not that important, and that they’d rather put the money into the pick-and-place machine.
“Yet, if you have a pick-and-place with capability to do 0201 or 01005 in ultra-fine pitch, and you buy the cheapest manual printer that you can get, you’re not going to be able to benefit from all that capability. And that’s something that you really must explain to the customer, and make sure that you’re advising the correct equipment for the job at hand,” says Stone. “In my opinion, a good manual printer for a start-up company is a good way to start. I mean, it’s a good tool to have in your toolbox, but is it going to be able to do the most challenging devices out there? No, probably not. I would say, as far challenges that have been around more recently, we’re seeing a lot of activity in very large board printing, especially for the LED industry. We’re seeing circuit boards that are between 1,200 mm and 1,500 mm long. That’s four to five feet—exceptionally large compared to what we were used to. It used to be if you had a board that was 16” x 18”, that was a really big board. Now, we’re seeing boards that are really long, and you need specialized equipment to handle it. Those types of printers have to be super accurate, especially in the adjusting of the axis when it’s aligning the stencil to the board. Because it is so long, your X-Y rotation is extremely critical. When it moves just a tiny little bit, when you’re out there on the fringes, it’s moving quite a lot. We’re also seeing a lot of people getting into the 01005 printing, which has its own set of challenges. Again, you’re going to need a good automatic printer, vision system, and all these programmable parameters that you’d expect in any high-end printer. That’s not something that you’re going to be doing on a simple tabletop device.”
To read the full version of this article which appeared in the December 2017 issue of SMT Magazine, click here.
Suggested Items
Driving Innovation: Direct Imaging vs. Conventional Exposure
07/01/2025 | Simon Khesin -- Column: Driving InnovationMy first camera used Kodak film. I even experimented with developing photos in the bathroom, though I usually dropped the film off at a Kodak center and received the prints two weeks later, only to discover that some images were out of focus or poorly framed. Today, every smartphone contains a high-quality camera capable of producing stunning images instantly.
Hands-On Demos Now Available for Apollo Seiko’s EF and AF Selective Soldering Lines
06/30/2025 | Apollo SeikoApollo Seiko, a leading innovator in soldering technology, is excited to spotlight its expanded lineup of EF and AF Series Selective Soldering Systems, now available for live demonstrations in its newly dedicated demo room.
Indium Corporation Expert to Present on Automotive and Industrial Solder Bonding Solutions at Global Electronics Association Workshop
06/26/2025 | IndiumIndium Corporation Principal Engineer, Advanced Materials, Andy Mackie, Ph.D., MSc, will deliver a technical presentation on innovative solder bonding solutions for automotive and industrial applications at the Global Electronics A
Fresh PCB Concepts: Assembly Challenges with Micro Components and Standard Solder Mask Practices
06/26/2025 | Team NCAB -- Column: Fresh PCB ConceptsMicro components have redefined what is possible in PCB design. With package sizes like 01005 and 0201 becoming more common in high-density layouts, designers are now expected to pack more performance into smaller spaces than ever before. While these advancements support miniaturization and functionality, they introduce new assembly challenges, particularly with traditional solder mask and legend application processes.
Knocking Down the Bone Pile: Tin Whisker Mitigation in Aerospace Applications, Part 3
06/25/2025 | Nash Bell -- Column: Knocking Down the Bone PileTin whiskers are slender, hair-like metallic growths that can develop on the surface of tin-plated electronic components. Typically measuring a few micrometers in diameter and growing several millimeters in length, they form through an electrochemical process influenced by environmental factors such as temperature variations, mechanical or compressive stress, and the aging of solder alloys.