-
- News
- Books
Featured Books
- pcb007 Magazine
Latest Issues
Current IssueThe Hole Truth: Via Integrity in an HDI World
From the drilled hole to registration across multiple sequential lamination cycles, to the quality of your copper plating, via reliability in an HDI world is becoming an ever-greater challenge. This month we look at “The Hole Truth,” from creating the “perfect” via to how you can assure via quality and reliability, the first time, every time.
In Pursuit of Perfection: Defect Reduction
For bare PCB board fabrication, defect reduction is a critical aspect of a company's bottom line profitability. In this issue, we examine how imaging, etching, and plating processes can provide information and insight into reducing defects and increasing yields.
Voices of the Industry
We take the pulse of the PCB industry by sharing insights from leading fabricators and suppliers in this month's issue. We've gathered their thoughts on the new U.S. administration, spending, the war in Ukraine, and their most pressing needs. It’s an eye-opening and enlightening look behind the curtain.
- Articles
- Columns
- Links
- Media kit
||| MENU - pcb007 Magazine
Pluritec Wants to Remove Human Factor from Solder Mask
December 6, 2017 | PluritecEstimated reading time: 4 minutes
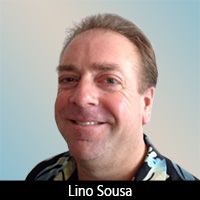
Solder mask remains a relatively hands-on task, which can result in human error. But equipment manufacturer Pluritec wants to change that. At PCB West, I spoke with Pluritec Vice President of Sales Lino Sousa about the company’s new spray technology that can turn solder mask application into what is essentially a push-button operation.
Andy Shaughnessy: I'm here at PCB West with Lino Sousa of Pluritec. Lino, why don't you just give us a brief background about Pluritec and we'll go on from there.
Lino Sousa: Pluritec has been in the printed circuit board market now for over 40 years, originally starting as a supplier of drill and routing equipment. In the last five years, we have started investing in other technologies that would augment what we're doing. And the new thing now is really solder mask application. It seems to be a department that still relies on tribal knowledge and experience. There are always hurtles to overcome, but we are seeing our solutions overcome these hurtles.
Shaughnessy: I understand you're looking at taking some of the human error out of the process?
Sousa: Well yeah, look at the way people apply solder mask today. You have screen technology, you have squeegees, you have inks and you're moving things around. It's supposed to be in a clean environment; it's very human-intensive, and there are lot of “touch and feel” type decisions that must be made with all these variables. With a lot of the equipment today, you don't want the human making those type of decisions. You just want them to upload a recipe, then just load and unload panels.
Shaughnessy: So how are you planning to change that?
Sousa: With the new spray technology, you can now put a panel into a machine that is controlled by a computer that will manage speed, pressure, and measure the ink, and now you're coating with something that is very repeatable and measurable. All of this is processed in an environmentally controlled chamber that can feed automatically to a quick dry tack oven. Now you just have to get your recipes correct and then it's very repeatable. You, me, any one of us could coat mask, because all we'd have to know is how to put panels in the machine and hit the button.
Now, let’s talk about flexibility. If you want to do a green board, that's great. But Johnny wants to do a blue board. With screen technology, now you’ve got to tear everything down, set up for blue, run the five panels, tear everything down again, and go back to old faithful green. This process can take anywhere from 45-90 minutes. This has been killing our customers, because now you have to also introduce LDI materials, which are different than LPI, so it's now becoming a material nightmare. With our new spray technology, we can put in multiple guns; we have some with up to four. Start with one board that's red, and you hit the button. The next one's blue? OK, hit the blue button. You want green? hit the green button. Again, the human element is taken away from set-ups, tear-downs, etc.
Shaughnessy: Why has this remained such a hands-on job over the years?
Sousa: Everybody says they want to improve quality and lower costs, but don’t touch my solder mask department because I've been doing it for 20 years and it works. So, now we have 40 systems out there, so we have moved from concept to reliable results. Now the hurtle is that we must change the mindset that screening is the only acceptable application of Soldermask.
Shaughnessy: Plus, it’s such a simple technology.
Sousa: If you really look at it historically, 20 years ago we used to screen the copper. Then we went to dry film and it was the Holy Grail to change that. And then we used to screen the legend. Now you’ve got inkjet for legend. Currently Inkjet really doesn't work for solder mask because it's 90% Ink deposition versus 5% for legend. Inkjet may be here some day but it isn’t here today. We're doing solder mask the way we did it 20 or 30 years ago. There’s no difference, and now it's time to change. We manufacture a system now that allows a person to put a board on one end, pick the color they want, and come out with nobody touching the panel. We have to diversify; that's what this market wants. They want tools, and they need tools. So, you’ve got to fill the need.
Shaughnessy: What do you see playing over the near future? What is Pluritec shooting for?
Sousa: Well, the markets are strong. It seems like we visit customers every day and everybody's busy. And they’re busy being busy. There’s urgency now. When equipment breaks, that's when they buy.
Shaughnessy: A lot of people are hiring as well. People are having a hard time finding qualified people, which I guess is a good sign, almost full employment.
Sousa: Yeah, haven't seen that in a while.
Shaughnessy: How's the show going for you?
Sousa: This is always a really interesting show for us because it's not really designed for a manufacturer. But they have 32 board shops here, and actually they're my customers, so they come by the booth and ask questions about what we're doing. So, we're just here poking the bear (laughs).
Shaughnessy: That’s great. Thanks for your time today, Lino.
Sousa: Thank you, Andy.
Suggested Items
SHENMAO Strengthens Semiconductor Capabilities with Acquisition of PMTC
07/10/2025 | SHENMAOSHENMAO America, Inc. has announced the acquisition of Profound Material Technology Co., Ltd. (PMTC), a premier Taiwan-based manufacturer of high-performance solder balls for semiconductor packaging.
KYZEN to Highlight Understencil and PCB Cleaners at SMTA Querétaro Expo and Tech Forum
07/09/2025 | KYZEN'KYZEN, the global leader in innovative environmentally responsible cleaning chemistries, will exhibit at the SMTA Querétaro Expo & Tech Forum, scheduled to take place Thursday, July 24, at Centro de Congresos y Teatro Metropolitano de Querétaro.
Driving Innovation: Direct Imaging vs. Conventional Exposure
07/01/2025 | Simon Khesin -- Column: Driving InnovationMy first camera used Kodak film. I even experimented with developing photos in the bathroom, though I usually dropped the film off at a Kodak center and received the prints two weeks later, only to discover that some images were out of focus or poorly framed. Today, every smartphone contains a high-quality camera capable of producing stunning images instantly.
Hands-On Demos Now Available for Apollo Seiko’s EF and AF Selective Soldering Lines
06/30/2025 | Apollo SeikoApollo Seiko, a leading innovator in soldering technology, is excited to spotlight its expanded lineup of EF and AF Series Selective Soldering Systems, now available for live demonstrations in its newly dedicated demo room.
Indium Corporation Expert to Present on Automotive and Industrial Solder Bonding Solutions at Global Electronics Association Workshop
06/26/2025 | IndiumIndium Corporation Principal Engineer, Advanced Materials, Andy Mackie, Ph.D., MSc, will deliver a technical presentation on innovative solder bonding solutions for automotive and industrial applications at the Global Electronics A