-
- News
- Books
Featured Books
- pcb007 Magazine
Latest Issues
Current IssueThe Hole Truth: Via Integrity in an HDI World
From the drilled hole to registration across multiple sequential lamination cycles, to the quality of your copper plating, via reliability in an HDI world is becoming an ever-greater challenge. This month we look at “The Hole Truth,” from creating the “perfect” via to how you can assure via quality and reliability, the first time, every time.
In Pursuit of Perfection: Defect Reduction
For bare PCB board fabrication, defect reduction is a critical aspect of a company's bottom line profitability. In this issue, we examine how imaging, etching, and plating processes can provide information and insight into reducing defects and increasing yields.
Voices of the Industry
We take the pulse of the PCB industry by sharing insights from leading fabricators and suppliers in this month's issue. We've gathered their thoughts on the new U.S. administration, spending, the war in Ukraine, and their most pressing needs. It’s an eye-opening and enlightening look behind the curtain.
- Articles
- Columns
- Links
- Media kit
||| MENU - pcb007 Magazine
Lamination to Drilling in Minutes: It's New and it's Not
January 3, 2018 | Barry Matties, I-Connect007Estimated reading time: 5 minutes
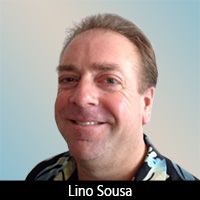
Barry Matties met with Lino Sousa at productronica to check out Pluritec’s new Pluricut HPL machine, which offers an all-in-one solution for flash routing, beveling, measuring, and corner routing.
Barry Matties: Lino, please tell our readers about this new machine.
Lino Sousa: Well, the neat thing, it's new and it's not. This is our latest Inspecta version , which, from version one, has been around for the last 15–20 years as an X-ray drill/router and optimizer. In North America, Inspecta is the defacto standard when it comes to X-ray optimization. Everybody loves this tool to do what it's supposed to do, which is optimize. But now we're going to take hours off the process time by coming from lamination, and automating all the prep steps of flash routing, beveling, measuring, corner routing, panel marking. All those steps take a lot of different pieces of equipment, and a lot of human labor. We're going to package that all into this new module.
We call it the Pluricut. We can add it as an attachment to existing systems in the field, or all new. Where you're going to come out of the press at 12:00, you're going to place your first panel on the table. Door is going to close. We're going to go out and measure the coupons on all layers, and if it's a good panel, we're going to drill new optimized tooling. Then we can measure panel thickness, and inscribe a QRC code, and man-readable header. We're going to then grab the panel, and send it back into the Pluricut. We're going to flash rout and bevel edge all four sides. In addition, you can have three corners rounded with an identifying corner. All of this data is recorded for your database in less than two minutes. Every two minutes, you're having a panel popping out the back end. So if you start your process at noon, you can be drilling at 12:05.
Matties: Without this process, you would typically spend two or three hours to do all those steps?
Sousa: It all depends, because you would be using a router. You’ve got to have time on the router. You’ve got a different tool for beveling. You’ve got to have an intelligent person knowing what he's doing, paying attention to all those steps, manually recording all that information, and making sure that you don't miss a beat. But now, all you're doing is taking an average employee, just unloading the press, and bringing the panels over. No human interface, no human errors.
Matties: It has a rather large footprint.
Sousa: Yes, but if you think of all the things it can replace. You can throw away that old router you don't need anymore. You can throw away the measuring unit you don't need anymore. You can throw away the beveller that you don't need anymore. All those things take maintenance. Now, you're doing all on one piece, and the $30-40,000 operator every shift goes away. Because you already have your operator at your inspector. You can get rid of one whole operator per shift. That's $120,000 a year.
Matties: The ROI on this must be pretty quick.
Sousa: Yeah, just the Pluricut alone, in the back end, pays for itself with labor saving in less than two years, let alone the convenience of getting it all done.
Matties: It's not just the convenience of getting it all done. It's the advantage that you're bringing to your end customer, being able to get that board out in 12 to 24 hours.
Sousa: It's all about time. Your press opens at 12:00, you're drilling at 12:05. You're literally drilling within five minutes of the press opening.
Matties: As opposed to 2:30 or 3:00 in the afternoon. What has the response been?
Sousa: Very good. We've installed our first production system on the East Coast, and we think we got all the kinks worked out. We're ready to hit the road running to customers.
Matties: Pluritec is an old brand name in the industry.
Sousa: Correct. We've been around since 1968 with Andrea Doria as the founder. He was one of the forefathers of drilling.
Matties: There was a lull, but the brand is coming back really strong. You're bringing some new energy into this.
Sousa: Well, the brand has always been strong in Europe. In North America, it suffered a lull, like a lot of companies; resources were used as best they could to keep the brand alive and develop/upgrade technology at the same time. They're one of the survivors. They've had all this technology in Europe, but they just didn't have someone to really raise the flag in North America. That's what I'm doing, saying, "Hey guys, look what's going on. We're missing the boat."
Matties: The lineup of equipment that you bring—inspection, drill, rout, the whole lineup—is impressive.
Sousa: The neat thing is, because of the QRC code, you can go right to our drill and you don't even have to set up the tool things. The drill will automatically read that and know which data file to do, which scale to use, which drill bits to use, and start drilling automatically.
Matties: Is the panel being held down by vacuum?
Sousa: Yes, that's held down by vacuum, because there are no tooling holes. It’s held down by vacuum so we can score it, and then we can drill the optimization holes. Fully optimized, ready to go, one-man operation.
Matties: When someone is looking to optimizing their drill rooms, what sort of things should they be looking at?
Sousa: The drill room is still being thought of in batches. You batch all the panels together. You stack all the panels together. You put all the tools together. You bring everything to a drill, then you load the drill one at a time as a batch. This means that for 15–20 minutes your drill is not drilling. We have to start thinking in singularity. You want to start drilling a panel as soon as it hits the drill department. Having five spindle drills, with only half the spindles being used, and you're waiting for slow cycle time to complete—this is inefficient. This single spindle drills you see here in our booth is a lights-out system with 1,700 tools ready to go, vision, auto loading/unloading and QRC code reading. You basically take the panel from the Pluricut, feed it into the system and walk away.
Matties: The single spindle makes a lot of sense.
Sousa: I'll be explaining that more in our eBook on how to optimize your drill room.
Matties: Is there anything that we haven't talked about, that we should cover on this?
Sousa: No, I think we're pretty much good. We’re excited about our eBook. That's really going to give us the platform to show you what it could be, where the future needs to be to meet the demands of accuracy, time, quality, deliverables to customers.
Matties: Lino, thanks for the quick tour. Greatly appreciate it.
Sousa: Thank you.
RELATED CONTENT:
Suggested Items
New Podcast Series Launches: Optimize the Interconnect
07/14/2025 | I-Connect007I-Connect007 is excited to announce the debut of Optimize the Interconnect—a new podcast series featuring guest Chris Ryder, senior director of business development at MKS’ ESI. This insightful series explores how MKS’ ESI is rethinking microvia formation for today’s most advanced HDI PCB and substrate designs.
Trouble in Your Tank: Can You Drill the Perfect Hole?
07/07/2025 | Michael Carano -- Column: Trouble in Your TankIn the movie “Friday Night Lights,” the head football coach (played by Billy Bob Thornton) addresses his high school football team on a hot day in August in West Texas. He asks his players one question: “Can you be perfect?” That is an interesting question, in football and the printed circuit board fabrication world, where being perfect is somewhat elusive. When it comes to mechanical drilling and via formation, can you drill the perfect hole time after time?
Excellon Installs COBRA Hybrid Laser at Innovative Circuits
06/23/2025 | ExcellonExcellon is pleased to announce the successful installation of a second COBRA Hybrid Laser System at Innovative Circuits, located in Alpharetta, Georgia. The Excellon COBRA Hybrid Laser System uniquely combines both UV and CO₂ (IR) laser sources on a single platform—making it ideal for high-density prototype and production printed circuit boards (PCBs).
Gorilla Circuits Elevates PCB Precision with Schmoll’s Optiflex II Alignment System
06/23/2025 | Schmoll MaschinenGorilla Circuits, a leading PCB manufacturer based in Silicon Valley, has enhanced its production capabilities with the addition of Schmoll Maschinen’s Optiflex II Post-Etch Punch system—bringing a new level of precision to multilayer board fabrication.
The Evolution of Picosecond Laser Drilling
06/19/2025 | Marcy LaRont, PCB007 MagazineIs it hard to imagine a single laser pulse reduced not only from nanoseconds to picoseconds in its pulse duration, but even to femtoseconds? Well, buckle up because it seems we are there. In this interview, Dr. Stefan Rung, technical director of laser machines at Schmoll Maschinen GmbH, traces the technology trajectory of the laser drill from the CO2 laser to cutting-edge picosecond and hybrid laser drilling systems, highlighting the benefits and limitations of each method, and demonstrating how laser innovations are shaping the future of PCB fabrication.