-
- News
- Books
Featured Books
- smt007 Magazine
Latest Issues
Current IssueWhat's Your Sweet Spot?
Are you in a niche that’s growing or shrinking? Is it time to reassess and refocus? We spotlight companies thriving by redefining or reinforcing their niche. What are their insights?
Moving Forward With Confidence
In this issue, we focus on sales and quoting, workforce training, new IPC leadership in the U.S. and Canada, the effects of tariffs, CFX standards, and much more—all designed to provide perspective as you move through the cloud bank of today's shifting economic market.
Intelligent Test and Inspection
Are you ready to explore the cutting-edge advancements shaping the electronics manufacturing industry? The May 2025 issue of SMT007 Magazine is packed with insights, innovations, and expert perspectives that you won’t want to miss.
- Articles
- Columns
- Links
- Media kit
||| MENU - smt007 Magazine
Why You Want Your EMS Partner to Be Annoying and Boring
January 4, 2018 | Neil Sharp, JJS ManufacturingEstimated reading time: 4 minutes
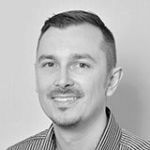
Outsourcing part or all of your manufacturing to an electronics manufacturing service (EMS) provider can be daunting. Handing over some of the control of your business can be a scary prospect. Perhaps you feel they won’t understand your products well enough, or be able to resolve issues promptly or to a satisfactory level.
When choosing an outsourcing partner you’ll want to know if they have the relevant technical capability, if they have a strong track record, are financially stable and whether they share the same beliefs about quality, processes, and attention to detail.
What you really want though, is for your EMS partner to be annoying, and ultimately boring. In this blog, we outline why.
A bit of a pain
At the start of your outsourcing journey your EMS provider will need a considerable amount of information from you. They will probably ask you lots of questions and request lots of data, they will scrutinize your product and processes, and they will want to check in with you on a regular basis.
But hang on. Didn’t you sign up to outsource your product so you didn’t have to think about manufacturing? You’re now ready to focus on designing and selling. Can’t they just get on with it?
Although you may have been manufacturing your product for years, your EMS partner hasn’t. They will be taking your product design and building it from scratch. They’ll want a Bill of Materials (BOM)detailing the parts required, a Gerber file with details for the Printed Circuit Board (PCB), and Computer Aided Design (CAD) data. Then there’s the ROHs status, and details of any additional build or quality standards. They might want detailed images of the product or even a ‘golden’ sample.
That’s a lot of information and you might not have everything immediately to hand to send over. So putting this data together probably sounds like a lot of effort on your part, right? Well, maybe. Much depends on your current systems and housekeeping, but this information is key to ensuring the accuracy and quality of your product. A good EMS partner will demand this detail and while this might feel like they are being a bit of a pain, it’s probably more worrying if you don’t hear anything at all from them.
Throughout the NPI process, your EMS partner’s engineers will be on the lookout for any potential problems or ways to improve your product or build process to improve quality, or reduce the cost and/or lead time of future builds. They might make recommendations for changes to materials supplied, the manufacturing process, documentation, or even the product design.
Is This Really Necessary?
Again, we understand this can be frustrating at times – you are letting go of the manufacturing side because you want to do just that – let it go. But if the NPI process is not followed correctly, or robust enough, you could end up with extended lead times, additional manufacturing costs, or poor-quality products further down the line.
A good EMS provider will also want to organize a formal business review soon after they’ve shipped the first couple of orders. These meetings are a useful way for both parties to agree which objectives have been met and which require further work/planning. The EMS provider will also want to show you progress against key performance indicators (KPIs) such as delivery performance and quality statistics. Sounds needy, but it’s important any issues are ironed out early on.
Fact is, in the early stages, your EMS partner will be in touch with you quite regularly. While this may annoyingly divert your attention from what you really want to be doing, it’s crucial for getting your provider to be what you really want, which is for them to be boring.
Yawn…
You want them to be boring in the sense that they just consistently deliver your products, with no effort required from you. One of the reasons you made the decision to outsource in the first place was because you wanted to free up more of your time and resources to focus on strengthening your core competencies - designing new products, and selling more goods to your customers. If your EMS partner manages your supply chain, assembly, test and logistics without any fuss or drama you can do just that.
You need to be able to rely on your EMS partner to manage the manufacturing side for you. Otherwise, what’s the point in outsourcing? You want to be free to focus on designing, selling, and adding value for your customers. The manufacturing side of your operation just needs to tick over in the background. Of course, when things do just happen, as expected, on-time, without pain or heartache they start to become dull. Predictable. Boring.
So, when it comes to finding the right EMS provider you have a choice. You could partner with a dull and boring one that may come across as slightly annoying and pedantic in the early stages. Or you could choose to work with someone much more dramatic, exciting, one that constantly keeps you guessing and on your toes.
Suggested Items
It’s Only Common Sense: Selling to Today's Generation of Buyers
06/30/2025 | Dan Beaulieu -- Column: It's Only Common SenseMillennials and Gen Z hold significant purchasing power and influence in industries worldwide. Selling to them requires adapting to their unique preferences, behaviors, and values, and exploring their buying habits, embracing their emphasis on social values, and mastering digital communication. Unlike previous generations, they prioritize experiences, sustainability, and value.
Adeon Technologies Signs Agreement as Distribution and Service Partner for PMT Global
06/13/2025 | Adeon Technologies BVAdeon Technologies has signed an agreement as Distribution and Service partner with PMT Global from Germany for its high precision measurement range of products.
Plexus Issues Fiscal 2024 Sustainability Report
06/06/2025 | PlexusPlexus Corp. released its fiscal 2024 Sustainability Report. The report, which is now available on the company’s Sustainability web page, highlights how Plexus’ commitment to sustainability and innovating responsibly is rooted in its values.
Technica Expands into Emerging Printed Electronics and Advanced Coatings Markets
06/04/2025 | Technica USATechnica is expanding its product portfolio with Agfa’s advanced line of Orgacon conductive coatings. The Orgacon products are a natural complement to Technica’s existing solutions and will allow the company to deliver greater value to customers in these markets.
Tariffs: Hope for the Best, Plan for the Worst
06/04/2025 | I-Connect007 Editorial TeamPaul Krugman received the Nobel Prize for Economics in 2008 for his work in economic geography and identifying international trade patterns. In April, he told the Goldman Sachs Exchanges podcast1, “The secret sauce of the Trump tariffs is that they are extremely uncertain. Nobody knows what they will be. Nobody knows what comes next. Now, if you’re a business trying to make plans, would you want to invest under those conditions?”