-
- News
- Books
Featured Books
- smt007 Magazine
Latest Issues
Current IssueWhat's Your Sweet Spot?
Are you in a niche that’s growing or shrinking? Is it time to reassess and refocus? We spotlight companies thriving by redefining or reinforcing their niche. What are their insights?
Moving Forward With Confidence
In this issue, we focus on sales and quoting, workforce training, new IPC leadership in the U.S. and Canada, the effects of tariffs, CFX standards, and much more—all designed to provide perspective as you move through the cloud bank of today's shifting economic market.
Intelligent Test and Inspection
Are you ready to explore the cutting-edge advancements shaping the electronics manufacturing industry? The May 2025 issue of SMT007 Magazine is packed with insights, innovations, and expert perspectives that you won’t want to miss.
- Articles
- Columns
- Links
- Media kit
||| MENU - smt007 Magazine
Making the Right Equipment Selection
January 25, 2018 | Stephen Las Marias and Patty Goldman, I-Connect007Estimated reading time: 7 minutes
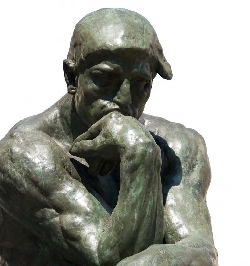
For this month’s issue of SMT007 Magazine, our focus is on equipment—not just on who’s got the latest and the greatest, but on how people decide what to buy, when to buy it, and how those decisions are made. In preparation for this issue, we invited Kathy Nargi-Toth, president of Eltek USA, and Matt Turpin, president and CEO of Zentech Manufacturing to a discussion on the decision-making process for new equipment, and the key considerations for choosing the best machine solution for a process.
Headquartered in Israel, Eltek manufactures rigid-flex, multilayer flex, and HDI PCBs. The company works primarily with the military, defense, and aerospace segment, and medical electronics. Baltimore-based Zentech Manufacturing, meanwhile, is an EMS firm mainly focused on the mil/aero and medical electronics markets.
“There are probably three main ways that a PCB fabricator would evaluate new equipment purchases,” says Nargi-Toth, who has been in the PCB industry for over 30 years. “The first would be to address a capacity issue, or a bottleneck. So, you’re looking for more of the same, perhaps. The second would be to meet a technical challenge that your current equipment can’t. The last one would be to do something that is new or revolutionary. That case would follow your roadmap and would be looking to purchase equipment that may not yet be available. In these cases, it is best to be working with your main equipment suppliers. Often, they are already looking at new techniques that can advance you along your roadmap. Most fabricators are doing some amount of each of these three types of purchases, depending on how the particular operation is focused.”
According to Nargi-Toth, in Eltek’s case one of the primary focuses is equipment that can handle thin materials. “There seems to be an overriding decision-making process when we go about buying a new piece of equipment. How does it handle flex material? How does it handle the sequential lamination, sub-composite layers or plated through-hole innerlayers? This material handing focus helps us concentrate on equipment that meets our overarching requirement, because we need to have equipment with 1-10 mil handling capabilities. As an example, we do a lot of hole filling, and we have been using one type of equipment for many years. But it wasn’t as adept at handling the thin materials. So, when we looked to add more capacity we evaluated a different machine and found that gave us better fill, especially with those small holes, and was also better for handling thin material. The process, basically, is we have a need, we put together a proposal of what type of equipment we want to look at, we gather some samples, we run samples, we evaluate them versus what we have, and then decide. We’ve done that for our etching line, and we have done that for laser drilling. Basically, benchmarking new equipment against existing and looking at two or three different types of equipment from different suppliers in the same category. We just purchased another laser drill, and in that case, we did a survey of what was out there, and we ended up buying another machine like the one we had, because it best met our needs.”
Being in the EMS business for about 35 years now, Turpin has already seen a lot of changes. According to him, in the old days—around 15 years or so back—an EMS firm could buy a set of equipment, and use the same set of equipment 10 years later. “Because technology just did not change that fast,” he says. “Back in the old days, you had a lot more mom-and-pop shops. A lot of Tier 4s and Tier 3s, because it wasn’t as capital intensive back then. It was great for an EMS business, selling from the equipment standpoint. I wouldn’t necessarily say ‘the good old days,’ but there’d be times where you bought the equipment, you could run the equipment, and things didn’t change that much. And then we entered a period where there was a rate of change, and we were like this until relatively recently, where you knew that there was new technology out there, but you could wait for a program, a customer, or an opportunity to come along before you buy. It’s like, ‘Okay, well, yeah I know that there are longer ovens out there. But if I get a 30-core layer board and it’s a big enough program, I’ll bite off and I’ll buy a new oven.”
Over the past five years, Turpin says you just don’t need to wait for a program because there was enough research to figure out what you needed. “You had to become fast with the technology to even know how you’d end up quoting, because you can’t just buy the equipment and start using it the next day. You have to develop a process around it. You’ve got to learn how to do it. You’ve got to hire people. In the EMS world, we are driven more towards having a technology roadmap, where we do need to plot out emerging technologies. Not just on the process side, but on the component side. Component suppliers are coming out with some crazy stuff that influences the equipment you need to process it. It is just creeping more into the EMS side.”
As an example, Turpin said you cannot just get an oven only when you get a 34-layer board program. “You can’t just have one oven, you need to have three ovens that can do heavy layer boards and highly integrated BGA technology on those boards. You need more than one rework machine to be able to rework BGAs that are on that. You have to get out in front of that,” Turpin says.
One of the technologies that Zentech started looking at a year ago was cleaning technology. “We spent six months just looking at all the different versions. It used to be you’d see a couple of LGAs, a QFN, on a board. We’ve got some with hundreds of LGAs on a board now, and it forces you to a completely different cleaning paradigm where you can sort of clean it with the old stuff, but not really. So, you really need to look at new technologies all the time. It’s the same thing with 3D AXI. You can’t use a manual X-ray system when you have a Class 3 board with 400 bottom-terminating components. There’s no way any human being is going to accurately look at all those without glazing over. You need automated technology to do the heavy inspection on that type of work. You still have a human to do a sample to make sure you have compliant joints, but there’s no way you can screen all those bottom-terminated joints manually,” says Turpin.
Challenging Equipment Suppliers
Do they ever make demands on their equipment or department to come up with something better for their processes?
Nargi-Toth says some of their equipment is ‘machine #1,’ which is when they have challenged their suppliers to give the industry something better. “I think many of the #1 machines that Orbotech has introduced have spent some time in Eltek,” she says. “We had one of the first laser direct imaging machines they made, and the first direct imaging solder mask machine they made. It is very important for our industry that these types of relationships exist between fabricators and the supply base. We are constantly challenging our suppliers to give us something better than the machine that we just bought from them.”
But sometimes, current technologies have notable limitations. “We’ve tried to get better handling, say, in a DES line, and there are some limitations in available equipment. It may handle a 1-mil dielectric layer, but it doesn’t necessarily handle that 1-mil film when we remove 75% of the copper from it. So, I would say, from our perspective as a panel flex supplier, there are some limits in what’s currently available to meet our requirements,” says Nargi-Toth.
Automation Vision
How is automation, or the drive towards it, affecting the decision process in acquiring new equipment?
“In the EMS world and certainly in the military/aero and the medical side, your raw material expense is going to be around 60–70% of your revenue,” says Turpin. “The number one expense, in our world, is raw materials. From an automation standpoint, you certainly want to be automated in terms of how you buy, plan and process your raw materials.”
While direct labor is always important, Turpin says it’s even more important to have a robust process that can make sure you have virtually no scrap. “You’ve got these $25–$40,000-dollarapiece PCBAs running through your facility at relatively low profit, low contribution margin. You really can’t afford to have any scrap. Your shift is focused less on labor to more on quality, reliability, and taking scrap down to zero. And, pretty much, rework down to zero, too, because you can’t afford to hold onto these components for very long. You’re more looking for velocity than you are efficiency on the labor side. Having said that, you’re always concerned about efficiency, but it’s not like it was in the old days because labor, as each year goes by, is increasingly a smaller percentage of your spend. At least, in my world.”
To read the full version of this article, which appeared in the January 2018 issue of SMT007 Magazine, click here.
Suggested Items
SHENMAO Strengthens Semiconductor Capabilities with Acquisition of PMTC
07/10/2025 | SHENMAOSHENMAO America, Inc. has announced the acquisition of Profound Material Technology Co., Ltd. (PMTC), a premier Taiwan-based manufacturer of high-performance solder balls for semiconductor packaging.
KYZEN to Highlight Understencil and PCB Cleaners at SMTA Querétaro Expo and Tech Forum
07/09/2025 | KYZEN'KYZEN, the global leader in innovative environmentally responsible cleaning chemistries, will exhibit at the SMTA Querétaro Expo & Tech Forum, scheduled to take place Thursday, July 24, at Centro de Congresos y Teatro Metropolitano de Querétaro.
Driving Innovation: Direct Imaging vs. Conventional Exposure
07/01/2025 | Simon Khesin -- Column: Driving InnovationMy first camera used Kodak film. I even experimented with developing photos in the bathroom, though I usually dropped the film off at a Kodak center and received the prints two weeks later, only to discover that some images were out of focus or poorly framed. Today, every smartphone contains a high-quality camera capable of producing stunning images instantly.
Hands-On Demos Now Available for Apollo Seiko’s EF and AF Selective Soldering Lines
06/30/2025 | Apollo SeikoApollo Seiko, a leading innovator in soldering technology, is excited to spotlight its expanded lineup of EF and AF Series Selective Soldering Systems, now available for live demonstrations in its newly dedicated demo room.
Indium Corporation Expert to Present on Automotive and Industrial Solder Bonding Solutions at Global Electronics Association Workshop
06/26/2025 | IndiumIndium Corporation Principal Engineer, Advanced Materials, Andy Mackie, Ph.D., MSc, will deliver a technical presentation on innovative solder bonding solutions for automotive and industrial applications at the Global Electronics A