-
- News
- Books
Featured Books
- design007 Magazine
Latest Issues
Current IssueRules of Thumb
This month, we delve into rules of thumb—which ones work, which ones should be avoided. Rules of thumb are everywhere, but there may be hundreds of rules of thumb for PCB design. How do we separate the wheat from the chaff, so to speak?
Partial HDI
Our expert contributors provide a complete, detailed view of partial HDI this month. Most experienced PCB designers can start using this approach right away, but you need to know these tips, tricks and techniques first.
Silicon to Systems: From Soup to Nuts
This month, we asked our expert contributors to weigh in on silicon to systems—what it means to PCB designers and design engineers, EDA companies, and the rest of the PCB supply chain... from soup to nuts.
- Articles
- Columns
Search Console
- Links
- Media kit
||| MENU - design007 Magazine
Who Really Owns the PCB Layout? Part 2
February 7, 2018 | Paul Taubman, Nine Dot ConnectsEstimated reading time: 6 minutes
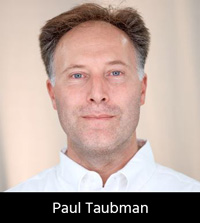
This article’s argument for mechanical engineering involvement in PCB design is specific to the layout. The schematics and circuit design such as power, analog, and digital belong to the electrical engineering domain and this area requires classroom and lab experience which one would expect from a degreed electrical program. It is not to say that a mechanical engineer cannot do circuit design. More so, we envision a future in which academia offers degrees in mechatronic design. Under the current circumstances, this industry is notorious for making gross assumptions about an engineer’s capabilities and we wish not to propagate the belief that a mechanical engineer can do the whole PCB design based on their degree alone unless they have been exposed to circuit design during their undergraduate career.
In our last article, we made the bold statement that the PCB layout is just as much a mechanical effort as it is an electrical one. We can go so far as to say that the PCB is an excellent example of mechatronics, the simultaneous blending of electrical and mechanical design practices. In this article, we will make the argument that it may be the mechanical engineers who are more prepared to take on the PCB layout.
Library Development
One of the critical aspects of the layout is the creation of the footprint. The footprint is the exposed copper on the board which will be used to attach the component during the assembly process. For the leads of the component to be fitted properly to the board, the pads of the footprint must be dimensioned to accommodate tolerances. Notice the words “dimensioned” and “tolerances” in the prior sentence. This is not the vocabulary of an electrical engineer nor is it something that an electrical engineer would be taught in an undergraduate program. Yet, any draftsman or mechanical engineer will be familiar with these terms.
The IEEE and IPC are the two primary authorities of the electronics industry. What is surprising is that when it comes to PCB specifications, handbooks and even the IPC’s Certified Interconnect Designer (CID) program, these documents are steeped in mechanical requirements. The IPC CID certification is focused on the requirements necessary to design a PCB that is manufacturable. In a 2013 version of the CID training, geometric dimensioning and tolerance (GDT) was introduced in depth. GDT is not taught to an electrical engineer unless he goes out of the way to learn it.
Beyond the footprints, there are also 3D component shapes. The ability to add these components to the footprints in the ECAD tools has greatly aided in the ability for the PCB board to be fitted based on 3D representations. The mechanical folks have been instrumental in making these components available. In a sense, mechanical engineers currently play a bigger role in the creation of footprints than they may realize.
Board Shape
We can no longer ignore the impact that marketing has on the shape of board. In many cases, the look of the product comes from the marketing department. Since the look of the product is mechanical in nature, they are inclined to interface with the mechanical team to bring their idea into a 3D representation. As a result, the board shape is being influenced by an organization that knows nothing about engineering who is driving the mechanical team which knows very little about electronics. Having a PCB-savvy mechanical team can go a long way in representing the needs of the circuit designers.
In the past, a square or rectangular board would have been adequate given the space available in the product’s mechanical enclosure. The design of the enclosure was based on the final product of the PCB layout. Advancements in the MCAD tools and manufacturing allow for products that are anything but square. Many board shapes are now being imported from the MCAD tools based on the dimensions of the enclosures. It is not unusual to find board with asymmetric curves. When it comes to complex shapes, MCAD tools are far better suited for drawing a board outline than the ECAD tools. In some EDA tools, one can create a board shape based on an imported enclosure, but this enclosure was more than likely created in an MCAD tool.
Component Placement
Component placement is another area that is becoming more driven by the mechanical design. It is now commonplace to pass the board and its components between the ECAD and MCAD tools. This is imperative to check key locations, especially components that the end user will need to press like a button or a switch, like a display monitor or LEDs, or connect through a cable. The mechanical designer (and the even the marketing team) have just as much input on the component placement as does the layout artist.
Through this collaboration, both the electrical and mechanical aspects of component placement may be sorted and determined prior to routing. This is a great example of mechatronic design in action, for it considers both the electrical and mechanical needs in real time. Without this collaboration, high-profile components are overlooked, and fitment conflicts between the board, the components, and the enclosure are prevalent.
Rules Checker
The PCB editor is driven by a rule checker. This includes, but is certainly not limited to, copper clearances, component clearances, trace widths, via sizes, and copper pull-backs. Like the footprints, these rules are driven by tolerances and dimensions. Though some of these are also driven by electrical requirements, especially in power or high-speed design, most of these rules are declared to ensure that the board can be fabricated and assembled. This again goes back to the commentary above about the need to understand GDT.
Routing
One of the biggest challenges of the design is the routing of the copper. This is one of those areas that requires experience and innate skills. It is certainly not taught, and even if it were, the curriculum would be based on rules of thumb and constant exercises to hone the skills. Therefore, no single engineering discipline may lay claim to being the best at routing.
Note that ECAD tool companies recognize the time and effort required to route boards. Because of market competition, there is an ongoing push to provide more features and tools to automate the routing and/or to assist in trace placement. Regardless, autorouting requires the layout artist to have a defined strategy, and that still requires experience and skills.
Thermal
Thermal issues have always been a concern with PCBs, especially in harsh environments and circuits with power components. With high-speed design, thermal issues also have a major impact on the power distribution network (PDN) of the board. Both ECAD and MCAD have been responding to this need with simulation tools. Most simulation tools require the user to provide initial conditions, meaning the user must have a fundamental understanding of heat flow. Like other aspects of PCB design, thermal dynamics tends to be taught in mechanical engineering.
Conclusion
The point of this discussion is to show that the PCB is as much a mechanical design as it is electrical. Granted, there are PCBs that are so complex that they require the experience and knowledge of an electrical engineer; however, PCB layout is very much a mechanical creature that can be tackled by a mechanical engineer with a bit of knowledge and experience in ECAD tools and the overall design process.
More so, we are seeing that the PCB is truly a mechatronic design. It needs to be designed with both electrical and mechanical needs in mind. As one looks to the future, we can no longer turn a blind eye to 3D printing, conductive inks, and embedded components. The way we fabricate and assemble electronics will not only be very different, but the skill sets will also be different.
We see a critical need for designers to get involved with the design of PCBs, regardless of their degree or experience.
Paul Taubman is technical services director for Nine Dot Connects, a PCB design bureau, reseller, and provider of design instruction and consulting services. This article originally appeared as a blog on the Nine Dot Connects website.
Suggested Items
Unlocking Advanced Circuitry Through Liquid Metal Ink
10/31/2024 | I-Connect007 Editorial TeamPCB UHDI technologist John Johnson of American Standard Circuits discusses the evolving landscape of electronics manufacturing and the critical role of innovation, specifically liquid metal ink technology, as an alternate process to traditional metallization in PCB fabrication to achieve ever finer features and tighter tolerances. The discussion highlights the benefits of reliability, efficiency, and yields as a tradeoff to any increased cost to run the process. As this technology becomes better understood and accepted, even sought out by customers and designers, John says there is a move toward mainstream incorporation.
Fresh PCB Concepts: The Critical Nature of Copper Thickness on PCBs
10/31/2024 | Team NCAB -- Column: Fresh PCB ConceptsPCBs are the backbone of modern electronics and the copper layers within these boards serve as the primary pathways for electrical signals. When designing and manufacturing PCBs, copper thickness is one of the most critical factors and significantly affects the board’s performance and durability. The IPC-6012F specification, the industry standard for the performance and qualification of rigid PCBs, sets clear guidelines on copper thickness to ensure reliability in different environments and applications.
Book Excerpt: The Printed Circuit Designer’s Guide to... DFM Essentials, Ch. 1
10/25/2024 | I-Connect007The guidelines offered in this book are based on both ASC recommendations and IPC standards with the understanding that some may require adjustment based on the material set, fabricator processes, and other design constraints. This chapter details high-frequency materials, copper foil types, metal core PCBs, and the benefits of embedded capacitance and resistor materials in multilayer PCBs.
The Cost-Benefit Analysis of Direct Metallization
10/21/2024 | Carmichael Gugliotti, MacDermid AlphaCarmichael Gugliotti of MacDermid Alpha discusses the innovative realm of direct metallization technology, its numerous applications, and significant advantages over traditional processes. Carmichael offers an in-depth look at how direct metallization, through developments such as Blackhole and Shadow, is revolutionizing PCB manufacturing by enhancing efficiency, sustainability, and cost-effectiveness. From its origins in the 1980s to its application in cutting-edge, high-density interconnects and its pivotal role in sustainability, this discussion sheds light on how direct metallization shapes the future of PCB manufacturing across various industries, including automotive, consumer electronics, and beyond.
Connect the Dots: Designing for Reality—Pattern Plating
10/16/2024 | Matt Stevenson -- Column: Connect the DotsIn the previous episode of I-Connect007’s On the Line with… podcast, we painted the picture of the outer layer imaging process. Now we are ready for pattern plating, where fabrication can get tricky. The board is now ready to receive the copper traces, pads, and other elements specified in the original CAD design. This article will lay out the pattern plating process and discuss constraints in the chemistries that must be properly managed to meet the customer's exacting manufacturing tolerances.