-
-
News
News Highlights
- Books
Featured Books
- smt007 Magazine
Latest Issues
Current IssueWhat's Your Sweet Spot?
Are you in a niche that’s growing or shrinking? Is it time to reassess and refocus? We spotlight companies thriving by redefining or reinforcing their niche. What are their insights?
Moving Forward With Confidence
In this issue, we focus on sales and quoting, workforce training, new IPC leadership in the U.S. and Canada, the effects of tariffs, CFX standards, and much more—all designed to provide perspective as you move through the cloud bank of today's shifting economic market.
Intelligent Test and Inspection
Are you ready to explore the cutting-edge advancements shaping the electronics manufacturing industry? The May 2025 issue of SMT007 Magazine is packed with insights, innovations, and expert perspectives that you won’t want to miss.
- Articles
- Columns
- Links
- Media kit
||| MENU - smt007 Magazine
Manufacturability: Pad Relief and Mask Relationship to Solder Joint Volume
March 9, 2018 | Ken Horky, Peterson ManufacturingEstimated reading time: 2 minutes
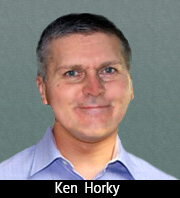
Electronic assembly thermal management has always been an issue but has become more significant as we pack more power and function into a smaller form factor. In recent years, the growing use of LEDs for illumination on a large scale has presented additional thermal demands. EMI control also benefits from generous copper use.
The first inclination for a designer is to add copper in the form of planes and flooding. How this copper is added with respect to the component footprint’s pads can alter the termination quality.
Calculating the area for each pad:
Cu-D = 63.0(L1), 11.8(W1)
Oval Pad = ((63-11.8) *11.8)+(PI()*(11.8/2)^2) = 714
+ Partial Rectangular Trace = 5.0*3.0 = 14.5, 14.5+714 = 729
Msk-D = 73.0(L2), 16.5(W2)
Unmasked Rectangular Copper Area = 73.0*16.5 = 1205
Where:
Cu-D = Non-solder mask defined or copper defined pads
• Pad features are created by the copper etching process in fabrication.
Msk-D = Solder mask defined pads
• Pad features are created by the respective solder mask pattern applied over copper, post etching in fabrication.
The Msk-D pad is 65% larger than the Cu-D pad.
Figure 1: Graphical representation of the pad definitions with example dimensions.
For simplicity, we’ll assume the solder paste deposition aperture is equal to the original pad size (often it is less). For the Cu-D pad, the trace to the pad adds relatively little additional copper area, creating only an additional 2% copper area to the pad. For the Msk-D pad, the surrounding copper plane adds significantly more copper area, 1.7X. Solder paste will occupy an area of 714 out of 1205 total pad area. This leaves 41% of the Msk-D pad area unaccounted for in solder joint volume. The post reflow results will be less interconnect volume at the termination. Without sufficient solder volume, the minimum fillet height may not meet your acceptance standards. The spoke width of thermally relieved pads can have the same effect on termination quality as an Msk-D pad. Pad size relative to mask expansion directly affects the magnitude of the issue.
In the example above, the Msk-D pad is 1.7 times larger than the original pad design using 5 mil mask expansion. If the pad was 10 times larger, using the same mask expansion, the Msk-D pad would only be 1.1 times larger. The smaller the pad, the greater the impact of mask defined pads.
Some variables to consider:
1) In design:
- Solder mask expansion or oversize value
- Thermal relief dimensions relative to pad size
2) Manufacturing:
- Stencil aperture size
- Stencil thickness
Additional Considerations
• Try to be consistent within a design layout using Cu-D or Msk-D pads, avoid mixing both.
• Many suppliers are now supplying recommended footprint dimensions for Cu-D and Msk-D designs. You may have to maintain both in the system library and use them accordingly.
• Telling your stencil fabricator to globally reduce aperture size by a percentage may produce undesired results. Take control, review the fabrication data yourself and edit to improve first run success.
• Lead-free solder doesn’t wet and flow as well as tin/lead solder did. This normally undesirable attribute may be a benefit for Msk-D pads since the solder doesn’t flow away from where it is printed as much during reflow, keeping the volume at the termination.
Ken Horky is a process engineer at Peterson Manufacturing.
Suggested Items
Driving Innovation: Direct Imaging vs. Conventional Exposure
07/01/2025 | Simon Khesin -- Column: Driving InnovationMy first camera used Kodak film. I even experimented with developing photos in the bathroom, though I usually dropped the film off at a Kodak center and received the prints two weeks later, only to discover that some images were out of focus or poorly framed. Today, every smartphone contains a high-quality camera capable of producing stunning images instantly.
Hands-On Demos Now Available for Apollo Seiko’s EF and AF Selective Soldering Lines
06/30/2025 | Apollo SeikoApollo Seiko, a leading innovator in soldering technology, is excited to spotlight its expanded lineup of EF and AF Series Selective Soldering Systems, now available for live demonstrations in its newly dedicated demo room.
Indium Corporation Expert to Present on Automotive and Industrial Solder Bonding Solutions at Global Electronics Association Workshop
06/26/2025 | IndiumIndium Corporation Principal Engineer, Advanced Materials, Andy Mackie, Ph.D., MSc, will deliver a technical presentation on innovative solder bonding solutions for automotive and industrial applications at the Global Electronics A
Fresh PCB Concepts: Assembly Challenges with Micro Components and Standard Solder Mask Practices
06/26/2025 | Team NCAB -- Column: Fresh PCB ConceptsMicro components have redefined what is possible in PCB design. With package sizes like 01005 and 0201 becoming more common in high-density layouts, designers are now expected to pack more performance into smaller spaces than ever before. While these advancements support miniaturization and functionality, they introduce new assembly challenges, particularly with traditional solder mask and legend application processes.
Knocking Down the Bone Pile: Tin Whisker Mitigation in Aerospace Applications, Part 3
06/25/2025 | Nash Bell -- Column: Knocking Down the Bone PileTin whiskers are slender, hair-like metallic growths that can develop on the surface of tin-plated electronic components. Typically measuring a few micrometers in diameter and growing several millimeters in length, they form through an electrochemical process influenced by environmental factors such as temperature variations, mechanical or compressive stress, and the aging of solder alloys.