The Vast Offerings in Laminate Technologies from TUC
April 10, 2018 | Patty Goldman, I-Connect007Estimated reading time: 8 minutes
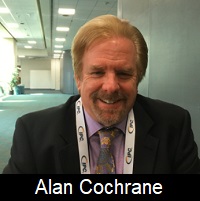
While at IPC APEX EXPO a few weeks ago, I sat down with George Hsin, chief strategy officer for TUC Worldwide, and Alan Cochrane, president of TUC North America. I was interested in learning more about the company and their laminate products and Alan was happy to fill me in.
Patty Goldman: Alan, please being by telling our readers about TUC and the types of materials you offer for PCB fabrication.
Cochrane: TUC is a laminate supplier with corporate headquarters and factory located in Jhubei, Taiwan, and factories in Changshu and Zhongshan, China. TUC has a worldwide sales organization as well as a North American distribution network with centers in Plymouth, Minnesota, as well as San Jose and Anaheim, California. TUC supplies a vast group of laminate technologies based on commercial-grade up to the high-end server and automotive radar applications. It's all for printed circuit boards that are getting a lot more diverse and complex; the material selections are proving to be very finite for the end application where we have to customize the dielectric constants of the materials to meet a specific end-product requirement, whether it be in the automotive or the high-speed digital server market. Now the focus is loss of the materials. Five years ago, it was dielectric constant. People used to be focused on thinner dielectrics to make smaller traces and maintain that characteristic impedance. Now, characteristic impedance is not the main requirement; overall signal loss is the main requirement.
Goldman: For which industries, or is it all of them??
Cochrane: Well, from cellphone applications to the high-speed digital applications. Now for power consumption, voltages are down to 0.8 volts, so having a loss that exceeds a couple hundred millivolts is no longer acceptable.
Goldman: Do you find differences between the industries? Are some of them getting more specific or do companies get more specific, like “we need this” and somebody else says “we need that”?
Cochrane: Automotive is very high frequency for the collision avoidance applications and within the automotive industry you have that which is very high-frequency millimeter wave-type applications, as well as under-the-hood applications. So high reliability, low Z-axis expansion of the materials. Even within the automotive group, there's a wide variety of material requirements that fall into that.
Goldman: You're obviously customizing products—laminates more or less. How many different types in that arena do you have?
Cochrane: For the material types we probably have, I would say, 25, maybe 30, different material types. Some are specific to an Intel processor product that has certain loss requirements and are mostly cost-driven. They also need to have a certain level of signal integrity to go along with it. Then there are the higher-end materials, where cost is not a driver, performance is the big driver. With that, we get into very expensive copper foils and processing. The components that go into the resin systems and the copper foils are very expensive, therefore the resulting materials are more expensive. But they meet a need that is critical to have. That is ever increasing. Not too long ago, we were at 14.5 gigahertz for the top-of-the-line chip applications. Now we're up to 25, 28 gigahertz. The next generation that is already being worked on is 56 gigahertz for high-speed digital applications. There's talk of 112 gigahertz. The chip is the limiting factor but the laminates have to support those high-speeds.
Goldman: You guys are working in all those areas. Now I know, recently you got some certifications. I remember seeing that in the news.
Cochrane: Yes. Through the IPC-4104, the IPC has started monitoring laminate suppliers such as ourselves, to ensure that they meet the requirements of IPC-4101, and they're doing the testing that's prescribed in that specification and they're able to do it in a reasonable, consistent fashion, which is to help the end-user realize that you're not going to get a lot of process variation when you buy products from that suppliers. TUC was the first one that was actually certified through this program and so we certified a number of different slash sheet materials within our factory.
Goldman: Nice. Your customers are all over the world, I presume?
Cochrane: Yes. They're all over the world. We have large OEMs here in North America, where most of the prototyping and the new product introductions happen. Although we do have many OEMs in China that are starting to gain some traction for the localized market there in China. Then we have a number of customers in Europe. A lot of the automotive OEM activity with collision-avoidance is there, but there are big telecom OEMs in Europe as well. It is definitely a world-wide arena and we're starting to get into military applications as well, because the military has certain high-reliability requirements. They are pushing our materials to utilize for their new chip packaging and that is being used in a lot of the airborne applications.
Goldman: Is that military mostly in North American or do you find it all over?
Cochrane: It's all over but predominantly North America and Israel.
Goldman: That's what I would have guessed. And automotive mostly in Europe and the U.S. and now some in China because there are automotive OEMs there that are starting to grow.
Cochrane: They're getting bigger, but from a technology standpoint they're lagging behind a bit more. The European companies are driving the automotive technology, but it definitely tiers down into the Asian marketplace. It used to be that, say for collision-avoidance, it was only in the high-end luxury type vehicles and now we're down into Hyundais and Kias. There's a lot of price pressure that's being put on them. They need high-performance materials for that application but they also need to get the price reduction. Where we come in is being able to supply a product that can do that at a relatively acceptable cost.
Goldman: As we all know, new products are expensive to begin with, there's always that learning curve, then prices come down some as the technology becomes more commonplace and then on the next highest technology product.
Cochrane: Even with the materials. Along that same line, as we introduce a material, of course there's a cost to pay for the research and development and all that testing. So the price point starts out higher but as it gets adopted within the industry and across multiple industry platforms, then the cost starts going down because the productivity goes up considerably. And that window is happening much faster. It used to be maybe a two-year time frame for that price/cost erosion. Now we're 12 months.
So that's a good and a bad thing. It sure keeps us developing new products. Right now, we're focusing on high-Dk materials. For some of the radar applications they want a high dielectric constant, so they want more capacitance in the materials. So we're building materials that have a Dk of 6.2 then 8 and then 10, in an epoxy-based type of material.
Goldman: We've talked about prices coming down and all that, but you need raw materials and their prices probably don't come down. We keep hearing about copper shortages and glass shortages and even resin shortages. How's your supply doing?
Cochrane: The supply is doing well. Right now, based on our screening of our copper supply for example, the materials that we use—for the high-end materials—are in relatively decent shape because there are fewer people in that marketplace using them. The problem happens in the lower-end materials where there aren’t requirements like signal-integrity and very-low profile coppers are not needed. That type of copper has much higher demand so there's some struggle and the cost goes up on those. Unfortunately, those laminates have been around for a long time and the cost has significantly dropped off on them. So in some cases we need to increase the price for those more common materials and that's a concern. In the newer materials, because they are new and haven’t reached that production stage or saturation level, we're not as impacted cost-wise. But within the copper suppliers, there's still competition. Within the resin suppliers, there's some level of competition and that helps a little bit.
Goldman: We keep hearing how lithium ion batteries are sucking up a lot of the copper foil. And that hurts.
Cochrane: And we understand. If I'm in the copper foil business and my requirement is to build something that just doesn't have pinholes, the battery people like it and they pay a higher margin than do the PCB suppliers, which much tighter requirements. The PCB industry has very strict quality controls on ductility, elongation, surface profiles, and coatings. Fortunately for us, like I said, low-profile coppers are not being used in the batteries electric vehicles at this point. Not that it's not going to be in the future.
Goldman: You can never sit back and say everything's okay. There's always more to be done, right?
Cochrane: We look at the marketplace for copper where we know there are copper mines that are stagnant and that not functioning at this time. We hope that they see the price-point and they decide to start utilizing.
Goldman: Actually, I didn't feel that the problem was the copper itself but making the copper foil which is electrodeposited onto drums. The supply was limited because there is or was a limited number of drums available on which the foil is deposited—and that shortage is not disappearing.
Cochrane: Yes, the drums are a long lead time, something like two years to get a drum made. Again, there's apprehension because right now things are looking good from that standpoint where the products are picking up, the consumption is picking up. That's I think some hesitation on the copper suppliers to put that into play. But still, it is mining as well. It has to start someplace. The solution…that's the initial part of it. And then it's processing too of course. But we haven't had any issues at this point.
Goldman: It's good to hear that your supply is stable. Thanks so much for your time. Have a good show.
Cochrane: It's been pretty crowded so that's good to see.
Goldman: Yes. It looks busy and I think there's a lot of enthusiasm. Everybody is upbeat this year. That's nice to see.
Cochrane: Thank you.
Testimonial
"Advertising in PCB007 Magazine has been a great way to showcase our bare board testers to the right audience. The I-Connect007 team makes the process smooth and professional. We’re proud to be featured in such a trusted publication."
Klaus Koziol - atgSuggested Items
How Good Design Enables Sustainable PCBs
08/21/2025 | Gerry Partida, Summit InterconnectSustainability has become a key focus for PCB companies seeking to reduce waste, conserve energy, and optimize resources. While many discussions on sustainability center around materials or energy-efficient processes, PCB design is an often overlooked factor that lies at the heart of manufacturing. Good design practices, especially those based on established IPC standards, play a central role in enabling sustainable PCB production. By ensuring designs are manufacturable and reliable, engineers can significantly reduce the environmental impact of their products.
50% Copper Tariffs, 100% Chip Uncertainty, and a Truce
08/19/2025 | Andy Shaughnessy, I-Connect007If you’re like me, tariffs were not on your radar screen until a few months ago, but now political rhetoric has turned to presidential action. Tariffs are front-page news with major developments coming directly from the Oval Office. These are not typical times. President Donald Trump campaigned on tariff reform, and he’s now busy revamping America’s tariff policy.
Global PCB Connections: Understanding the General Fabrication Process—A Designer’s Hidden Advantage
08/14/2025 | Markus Voeltz -- Column: Global PCB ConnectionsDesigners don’t need to become fabricators, but understanding the basics of PCB fabrication can save you time, money, and frustration. The more you understand what’s happening on the shop floor, the better you’ll be able to prevent downstream issues. As you move into more advanced designs like HDI, flex circuits, stacked vias, and embedded components, this foundational knowledge becomes even more critical. Remember: the fabricator is your partner.
MKS’ Atotech to Participate in IPCA Electronics Expo 2025
08/11/2025 | AtotechMKS Inc., a global provider of enabling technologies that transform our world, announced that its strategic brands ESI® (laser systems) and Atotech® (process chemicals, equipment, software, and services) will showcase their latest range of leading manufacturing solutions for printed circuit board (PCB) and package substrate manufacturing at the upcoming 17th IPCA Show to be held at Pragati Maidan, New Delhi from August 21-23, 2025.
MKS Showcases Next-generation PCB Manufacturing Solutions at the Thailand Electronics Circuit Asia 2025
08/06/2025 | MKS Instruments, Inc.MKS Inc, a global provider of enabling technologies that transform our world, today announced its participation in Thailand Electronics Circuit Asia 2025 (THECA 2025), taking place August 20–22 at BITEC in Bangkok.