Estimated reading time: 3 minutes
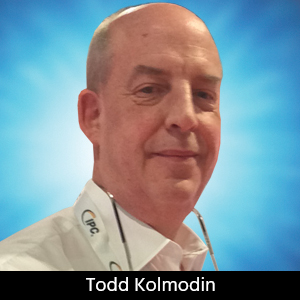
Testing Todd: AVI—Your Tireless Friend in Final Inspection
After a brief hiatus, I’m back with a sharp pencil. With IPC APEX EXPO 2018 still fresh in our memory I’m sure you had time to see automated visual inspection (AVI) equipment at the show. Those who came by our booth saw one in action. This technology is gaining traction in our industry due to several factors.
The “automation vs. human” debate continues. There are experts with many years of experience -performing final inspection with precise detail. This is not debated. However, in the course of human events, circumstances change with unpredictable results. This presents challenges to manufacturers striving to deliver product on-time and within specification guidelines.
Let’s face it: The specifications and requirements are more challenging day by day. Ever-changing IPC, ISO, AS9100, military, ITAR and required cybersecurity are all playing substantial roles in our daily life. Further complicating matters are the constraints of time-to-market demands vs. cost. The gap is shrinking between the market’s willingness to pay vs. cost of manufacture, and with this comes the need to conjure whatever magic possible to stay afloat. Tough decisions to be sure whenever automation vs. human element is concerned.
The question comes up quickly: What can AVI do for me? It’s another capital expenditure and what is the return? What is this thing going to provide?
Automated visual inspection is a straightforward term for exactly what this equipment does. Much akin to AOI, the PCB is scanned in its final form for defects previously done by an inspection technician. AVI algorithms allow for unwanted defects to be automatically identified and displayed clearly for review.
These defects are preserved in a database for further review and can be used for statistical analysis of process capability.
The difficulty with manual inspection is the operator’s field of view, lighting, ambient distractions and memory retention of the tomes of information they need to review of any given PCB on demand. Not surprisingly, that demand can change mid-order, requiring the operator to immediately change focus to a whole new PCB, many times with absolutely different requirements! It can be overwhelming, to be sure.
The AVI uses sophisticated CCD multicolor cameras with detection resolution down to 5 microns. Coupled with LED multi-channel lighting, the capture effectiveness is impressive.
Now with this technology we also achieve predictability and repeatability. AVI is driven by your CAD/CAM data so observance variance is removed. Of course, when the machine is set up for the specific PCB, fine-tuning can be accomplished to allow for manufacturing tolerances.
In Figures 1 and 2 we can see the display screen on an AVI machine. The CAM representation is shown vs. the actual board topography. From here on out, it is predictable and repeatable.
One can calculate with favorable accuracy how many panels or square feet (depending on how you calculate throughput) will be produced. It is not uncommon to see throughput ~400 sf/hr.
Remember, the AVI is looking for multiple imperfection possibilities simultaneously. Exposed copper, land violations, annular ring, solder mask imperfections/violations, missing features, and even surface discoloration are all simultaneously screened. As noted previously, defects found are visually displayed to the inspection technician. Non-conforming product is segregated from conforming so that review can be performed on the non-conforming product. Remember, we are not making the decision as to whether the product is initially conforming or not. CAD/CAM is driving the inspection along with allowed manufacturing tolerance. Here is our predictability and repeatability coming back into play.
Suppose, due to manufacturing constraints, the job has to change immediately. If a repeat job, we just load the saved program and we are inspecting within minutes. Different restrictions on the new job? No problem. AVI already knows the requirements and moves right on with inspection. If a new job, it must be set up only once, saved and production moves on.
Now back to the automation vs. human argument. We are not replacing the human fac tor but shifting the focal point. AVI is not selfaware (yet), so we still need to tell the machines how to perform the task and review the outputs generated just like any automated process. It still must be monitored for accuracy, repeatability and stability. However, for the tedious task of squinting at a PCB for hours on end attempting to identify all possible surface defects, we can leave that to the AVI as it doesn’t tire and its eyes don’t strain!
Todd Kolmodin is the vice president of quality for Gardien Services USA, and an expert in electrical test and reliability issues. To read past columns, or to contact Kolmodin, click here.
This article originally appeared in the March 2018 issue of PCB007 Magazine, click here.
More Columns from Testing Todd
Testing Todd: Why 4-wire Kelvin?Testing Todd: Why TDR?
Testing Todd: Positivity Boosts Employee Morale
Testing Todd: Preparing Employees for the Long Haul
Testing Todd: Where Can We Improve?
Testing Todd: Turning Into the Wind
Testing Todd: Coming Back to Life—Design Recovery
Testing Todd: Decision Time—Invest or Delegate?