-
- News
- Books
Featured Books
- pcb007 Magazine
Latest Issues
Current IssueIn Pursuit of Perfection: Defect Reduction
For bare PCB board fabrication, defect reduction is a critical aspect of a company's bottom line profitability. In this issue, we examine how imaging, etching, and plating processes can provide information and insight into reducing defects and increasing yields.
Voices of the Industry
We take the pulse of the PCB industry by sharing insights from leading fabricators and suppliers in this month's issue. We've gathered their thoughts on the new U.S. administration, spending, the war in Ukraine, and their most pressing needs. It’s an eye-opening and enlightening look behind the curtain.
The Essential Guide to Surface Finishes
We go back to basics this month with a recount of a little history, and look forward to addressing the many challenges that high density, high frequency, adhesion, SI, and corrosion concerns for harsh environments bring to the fore. We compare and contrast surface finishes by type and application, take a hard look at the many iterations of gold plating, and address palladium as a surface finish.
- Articles
- Columns
Search Console
- Links
- Media kit
||| MENU - pcb007 Magazine
Estimated reading time: 2 minutes
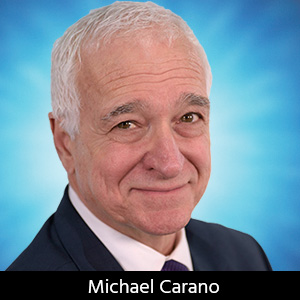
Contact Columnist Form
Trouble in Your Tank: Looking at PTH Voids
Introduction
Several columns have been published in this space describing the origins of voids in the plated through-hole. However, not all voiding is caused by or has its genesis in the electroless copper (PTH metalization) process. For this edition of “Trouble in Your Tank,” I present another look at voids and additional root causes that may be less understood.
Pre-electroplating Causes of Voids
One of the areas often overlooked as a cause of plating voids is a discontinuity in the electroless copper deposit. However, what if the panels were void-free after electroless copper only to void later in the manufacturing process? Several possibilities must be considered when such voiding is discovered. These include:
- Scrubbing prior to resist lamination
- Excessive copper removal caused by the microetch prior to electrolytic copper plating
- Photoresist residue in the via
In general, the type of void one would see is shown Figure 1. The defect depicted is often referred to as a corner void. In this case, copper plating is missing on all four corners of the hole.
Again, keep in the mind that there was no voiding related to electroless copper. So what could be the root cause of the void shown in Figure 1? It is easy see to the bare dielectric at the corners. Yes, there is sufficient copper plating in the via, however, the slope of the copper adjacent to the void has the appearance of an etched copper trace. There is the over-hang of the plated etch resist (tin or tin-lead).
The genesis of this etch void is due to the thin knee. That is, the tin or tin-lead on the corner or knee of the hole is less than optimum thickness. The thin deposit will not withstand the attack from the etching process, allowing the copper to be etched away.
Thin etch-resist plating at the knee of the via can be attributed to improper solution agitation in the tin plating process. In addition, when the organic addition agents are out of balance, thin tin deposits are often the result.
Figure 1: Example of a corner void. (Source: IPC-9121)
Excessive turbulence in the plating solution leads to excessive suppression of the deposition of metal at the knee.
At the same time, additive imbalance in the electrolytic copper plating solution leads to thin copper plating at the corner (Figure 2). It has been theorized that levelling components, carrying a positive charge, migrate preferentially to high-current density areas, just like metal ions, and inhibit metal deposition. If too much leveller is present, either because the bulk concentration is too high or the replenishment rate of leveler to the through-hole corner is higher than its consumption rate, then metal deposition at the corner will be suppressed leading to the thin knee condition. (I will present more detail on plating processes and the functioning of addition agents in a future column.)
To read the full version of this article which appeared in the April 2018 issue of PCB007 Magazine, click here.
More Columns from Trouble in Your Tank
Trouble in Your Tank: Yield Improvement and ReliabilityTrouble in Your Tank: Causes of Plating Voids, Pre-electroless Copper
Trouble in Your Tank: Organic Addition Agents in Electrolytic Copper Plating
Trouble in Your Tank: Interconnect Defect—The Three Degrees of Separation
Trouble in Your Tank: Things You Can Do for Better Wet Process Control
Trouble in Your Tank: Processes to Support IC Substrates and Advanced Packaging, Part 5
Trouble in Your Tank: Materials for PWB Fabrication—Drillability and Metallization
Trouble in Your Tank: Supporting IC Substrates and Advanced Packaging, Part 5