-
- News
- Books
Featured Books
- smt007 Magazine
Latest Issues
Current IssueMoving Forward With Confidence
In this issue, we focus on sales and quoting, workforce training, new IPC leadership in the U.S. and Canada, the effects of tariffs, CFX standards, and much more—all designed to provide perspective as you move through the cloud bank of today's shifting economic market.
Intelligent Test and Inspection
Are you ready to explore the cutting-edge advancements shaping the electronics manufacturing industry? The May 2025 issue of SMT007 Magazine is packed with insights, innovations, and expert perspectives that you won’t want to miss.
Do You Have X-ray Vision?
Has X-ray’s time finally come in electronics manufacturing? Join us in this issue of SMT007 Magazine, where we answer this question and others to bring more efficiency to your bottom line.
- Articles
- Columns
- Links
- Media kit
||| MENU - smt007 Magazine
LPKF Sees Increasing Use of UV Lasers
May 30, 2018 | Stephen Las Marias, I-Connect007Estimated reading time: 7 minutes
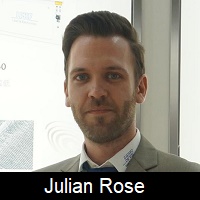
LPKF Laser & Electronics AG is a laser machine manufacturer that provides solutions for SMT and PCB processes, including stencil lasers, drilling machines, UV lasers, and depaneling systems. In an interview, Julian Rose, product manager for the UV and stencil laser machines of LPKF, discusses the challenges in laser stencils and strategies and techniques to address them, and the increasing use of UV lasers.
Stephen Las Marias: What are the greatest challenges that your customers are facing now when it comes to creating stencils?
Julian Rose: Basically, everything is getting smaller. We were always talking about apertures with the same type of circuit microns at the minimum, and right now, it’s getting even smaller, up to 20 or even 10 microns. This is a challenge at this stage because the stencil laser is made for stainless steel materials, so you need to have a melting process that is taking place and you need to somehow be able to do that with the laser. We have already shown that we can also go down to 10 microns, but there are other processes behind that, which is our limitation. In some parts of the printing process, 10 microns is really a challenge also.
Las Marias: How do you help address those issues?
Rose: We do several investigations on surface roughness because it is basically influencing how good we can get the solder paste through the stencil. We're investigating this and finding out parameters to improve the roughness and get it as smooth as possible. On the other hand, we try to optimize the laser process also so that when you have smaller apertures, the quality is the same as those of bigger apertures.
Las Marias: Has it always been laser process, or were there mechanical processes before?
Rose: Yes, there are also mechanical processes to create a stencil. Of course, this is not very efficient because the lag time of drilling tools are very low due to the stainless steel. There are other kinds of stencils like polymer stencils, for example. However, the lifetime of this is not so good so it won’t be able to handle 10,000 printing times, for example. Even if they are cheaper and might have nice printing results, the lifetime just comes down to the metal quality.
Las Marias: What makes your laser stencil technology unique in the market?
Rose: A combination of performance and security. For a long time, we don’t have any competition; but that changed in recent years, so we needed to make new developments. One of those is the RTPC, or real time process control. This enables us to detect every single laser pulse, and whether it cuts through the material. Why? Because there might be some changes in the material—maybe it’s not very flat, or not tight enough in the frame. To avoid any downtime for the customers, we control every single laser pulse. If there is an error happening, we will inform the customer, or we'll automatically regenerate the same aperture again. It’s 100% safe for the result of the stencil, and no additional AOI would be needed, for example. In addition, as step-up and step-down stencils become more necessary, we have solutions for that.
Las Marias: Why is there a need for step stencils?
Rose: If you think about a regular PCB and there’s an IC connector on top, when the pitch of the connectors is smaller, you would need to have less solder paste. You would decrease the thickness of the stencil—which is why it’s called step down—to get a small solder paste volume because the aperture is smaller. Then, when you push the solder paste through the stencil, there's less space for the paste and less material. On the other hand, step up is the other way around. For the big connectors, for example, you need more solder paste and that is why you make the step up.
Las Marias: Where do you think the development of stencil laser is headed?
Rose: That's a good question. Without telling too much about this, efficiency is not really the challenge here anymore, because I think the difference here with the machines is already very good. There are several companies that can serve the market already, and a lot of them use our stencil lasers. It’s more a matter of quality and price. Security wise, there are also no challenges because the security of the PCB itself is much worse than our stencil laser. It is more a matter of dimension and quality for cutting roughness, for example.
Las Marias: And laser is the technology to do it?
Rose: Yes, there’s no other way around. It’s the most versatile way to do it; it’s very cost efficient and there’s no need for anything else involving any chemical waste.
Las Marias: Let's move to drilling. As devices become smaller, the shrinking board real estate is driving manufacturers to do microvias so that they can maximize the dimensions or the functionality of the board. From your perspective, what are the challenges when it comes drilling these vias?
Rose: Drilling is also like the stencil laser. When it comes to drilling machines, we focus on UV laser drilling. CO2 lasers have a slight limitation in size, so you can get a small focus laser. However, after a certain point, it’s very difficult to get even smaller, it takes a lot of effort. UV lasers have the advantage in that you can have a very small focus laser—50 µm. That’s small, and that is one advantage. The other advantage is you have no limitation of materials you want to cut. Your UV laser can process almost every material.
The CO2 laser is currently very much in use and will still be for HDI, for example. It will be there for a very long time because with these thick materials, there is no need to get very small holes. For flex materials, you can see the current state of the art with 75-100 µm in diameter. Sometimes, even smaller, like 55 µm. The trend is going down to 35 or even 20 µm.
The 20 µm was the target for most machines, but it must have reasonable quality and speed.
Las Marias: What’s next for UV laser drilling?
Rose: I think it’s all a matter of price-performance ratio—faster and lower price. That's clear, because the demand is growing. Also, the production capacity needs to be adapted to that and the number of machines increasing, and the customer doesn't want a very high investment at the end of the day. So, we always try to have the best quality at a reasonable price. We need to improve this in the next couple of years.
Las Marias: Has there been an increase in the adoption of UV drilling?
Rose: Yes, at least with UV laser in general, since it’s such a versatile tool. You can use it for so many different processes. We can think about surface plating, we can think about drilling, cutting, all these things doing cavities. There are a lot of possibilities, but now, it's more a matter of, “Is it necessary to switch to a UV laser or can I still use my mechanical processes?” By using mechanical drills, the problem is you'll always have dust, for example, and stretch the material. We always tell customers that just buying laser makes no sense. You need to have at least a reason for that. You need to have smaller circuitries, you have problems with dust, and you have sensitive packages, for example, where you cannot use mechanical drills anymore.
Page 1 of 2
Suggested Items
BEST Inc. Introduces StikNPeel Rework Stencil for Fast, Simple and Reliable Solder Paste Printing
06/02/2025 | BEST Inc.BEST Inc., a leader in electronic component rework services, training, and products is pleased to introduce StikNPeel™ rework stencils. This innovative product is designed for printing solder paste for placement of gull wing devices such as quad flat packs (QFPs) or bottom terminated components.
KYZEN to Focus on Aqueous Cleaning and Stencil Cleaning at SMTA Juarez
05/20/2025 | KYZEN'KYZEN, the global leader in innovative environmentally responsible cleaning chemistries, will exhibit at the SMTA Juarez Expo and Tech Forum, scheduled to take place Thursday, June 5 at the Injectronics Convention Center in Ciudad Jarez, Chihuahua.
KYZEN to Spotlight Stencil Cleaning Solutions at SMTA Oregon
05/02/2025 | KYZEN'KYZEN, the global leader in innovative environmentally friendly cleaning chemistries, will exhibit at the SMTA Oregon Expo & Tech Forum, scheduled to take place on Tuesday, May 20 at the Wingspan Event and Conference Center in Hillsboro, OR. KYZEN’s cleaning expert Jeff Deering will be on-site at the expo providing information about stencil cleaning chemistries, including KYZEN E5631J.
KYZEN to Feature Stencil Cleaning and Aqueous Cleaners at SMTA Capital Expo and Tech Form
04/28/2025 | KYZEN'KYZEN, the global leader in innovative environmentally responsible cleaning chemistries, will exhibit at the SMTA Capital Expo and Tech Forum, scheduled to take place Thursday, May 8 at George Mason University – Mason Square in Arlington, VA.
KYZEN Focuses on Aqueous Cleaning and Stencil Cleaning at SMTA Wisconsin
04/24/2025 | KYZEN'KYZEN, the global leader in innovative environmentally responsible cleaning chemistries, will exhibit at the SMTA Wisconsin Expo and Tech Forum, scheduled to take place Tuesday, May 6 at the Crowne Plaza Milwaukee Airport. KYZEN will be on-site to provide attendees with information about aqueous cleaning chemistry AQUANOX A4618 and stencil cleaner KYZEN E5631J.