-
- News
- Books
Featured Books
- smt007 Magazine
Latest Issues
Current IssueMoving Forward With Confidence
In this issue, we focus on sales and quoting, workforce training, new IPC leadership in the U.S. and Canada, the effects of tariffs, CFX standards, and much more—all designed to provide perspective as you move through the cloud bank of today's shifting economic market.
Intelligent Test and Inspection
Are you ready to explore the cutting-edge advancements shaping the electronics manufacturing industry? The May 2025 issue of SMT007 Magazine is packed with insights, innovations, and expert perspectives that you won’t want to miss.
Do You Have X-ray Vision?
Has X-ray’s time finally come in electronics manufacturing? Join us in this issue of SMT007 Magazine, where we answer this question and others to bring more efficiency to your bottom line.
- Articles
- Columns
- Links
- Media kit
||| MENU - smt007 Magazine
Design and Manufacturing Perspectives from DISH Technology’s Les Beller
May 30, 2018 | Barry Matties, I-Connect007Estimated reading time: 23 minutes
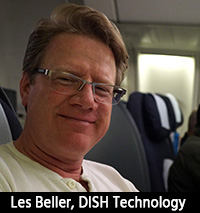
I recently interviewed Les Beller, a long-time PCB designer who is now a manufacturing engineer for DISH Technology. We discussed his company’s business shift towards 5G and streaming, and the stresses that puts on a design team. He also explains the greatest challenges that he’s facing with HDI and higher frequencies, and the added importance for designers to understand the manufacturing process and DFM tools.
Barry Matties: For our readers, give us a little bit of your background.
Beller: I'm a manufacturing engineer for DISH Technology. We used to be known as EchoStar Technology, until we were absorbed back in with DISH as DISH Technologies. Prior, I was a quality engineer, and before that I was a PCB designer for about 30 years, back to tape and Mylar. So I've done the nose of the dog, the tail of the dog, and now I'm in manufacturing engineering, which is sometimes on both ends of the dog!
Matties: And all the parts in between. Let's talk about design for a minute. I would think that's a foundation for everything that you're doing. When you look at designs today, what's your impression?
Beller: The first thing I look at with designs today is how they're utilizing the board space, taking into consideration whether it's a consumer product or a high-mix/low-volume product. I look at some of these traits from a designer's view as well as an assembly view, and how they’re interconnecting/packaging the PCBs. Are they designed for a resilient life? Are they going to be long-life products out in the field? Did the designers create a board that is going to be easily fabricated and inexpensive to build? I perform tear-downs occasionally and am amazed how well, and how poor, a product can be designed with respect to serviceability.
Matties: You mentioned the HDI; is that a new area for DISH?
Beller: Absolutely. We've traditionally been involved with designing set-top satellite TV products with as few PCB layers as possible, down to the cost per square-inch pricing. We have only had two or three HDI designs in the past. We now are performing a refocus based on the drop-in pay-TV services—people are doing more streaming. We've had to shift our service from purely satellite-based product to an OTT type streaming product, and have also had to learn to contract out to other OEMs that need this type of product. One of our newer niche products is in the multi-camera streaming and production market, SlingStudio, which is not at all related to pay-TV. What’s new in our future is going to be 5G IoT type products. Based on DISH's award of the frequency bands we obtained from the FCC, we're going to be setting up our 5G type network and designing everything under the sun that will be narrow-band IoT for the customers. Some of this IoT is already determined and in process, but the layers are just being peeled back in this new market. Everyone is rushing into it.
Matties: Is the push for HDI just purely a space functionality issue?
Beller: Primarily, yes. We'll still have different technologies of boards. HDI will be necessary depending on the chip architectures and device packaging. If we get down to very low-pitch devices, we're going to have to use HDI. This is based on assumptions that a good portion of the products are going to be more of a compact type of product. We will still steer our products to the technology they require to save cost, whenever possible. It’s our mantra!
Matties: There's a lot of conversation about HDI lowering your costs. Or does it actually cost more?
Beller: I would say the engineers tend to think that immediately it's going to lower the costs because it can be much smaller, but that is rarely the case. This is where a PCB designer needs to be intelligent, to push back and validate if the industrial design (ID) requires the end product to be that small. Let’s use a bit more space for the vias; let's not force the fabricator to put more labor into the board or force them into a low-yield process just to make my board easier to design. How about a look at panel usage, alternate materials or stack-ups? These habits will always save you cost and open up negotiation windows with the suppliers. I believe what primarily drives HDI for us is going to be product size (like a mobile phone or portable device) and then functionality (processing speed) that will drive the HDI requirement and cost. Then of course, there's the middle market, in which I think size doesn’t matter quite so much for a product. Some companies will tend to overdesign to get to market fast, then wont take the re-design path for cost-savings like we would all hope. This is a critical decision for the management: time to market or cost? There are many designers, ourselves included, who are learning more about HDI as we move forward.
Matties: Designers who I'm talking to are saying, “Well, we would never use landless vias because it's not spec’ed in.”
Beller: Customers are concerned with the reliability. The fabs like it, as it solves a little bit of a registration issue for them as the tech drives smaller. Somebody told us about using landless vias in our future products with them; as long as there is good information on the service life, it might help in some cases.
Matties: Because if you can get rid of the rings, you bring in a lot more real estate, right?
Beller: Absolutely.
Matties: I don't know that there's an appetite to pursue it. For me, I don't understand why.
Beller: You should look at the big picture when you're talking about a newer technology. It's new to some people who never would have considered it before. My first concern with a landless via on a portable is going to be resiliency. Then during the manufacturing, do I have the right laminate that's not going to create a lot of Z-axis expansion and put the interconnect with the barrel at risk? There’s no pad to have pad-rotation on! There still needs to be consideration for when it's appropriate and when it's not appropriate.
Matties: It seems like if we're really looking at functionality, you must pursue this path. If you're looking to add more functionality in the space that you already have.
Beller: Like a power application. Today's switchers and our processors are running so hot that the thermal cycle in a product is going to just wreak havoc on any of the board in that area. That's why the data is going to be real critical to that kind of technology.
Matties: In your role, what are the greatest challenges that you face dealing with your suppliers?
Beller: Boy, that's a good question. There are indeed several. I would say that my biggest challenge has been the suppliers using and maintaining statistical process control (SPC) to control our more critical signals on the boards. The suppliers we continue to use have adapted, and through a) data analysis, b) process/quality improvement and c) development of their processes through our initial development and proto cycles. They have come to realize that using SPC is a requirement in some areas. Many profess that they utilize the prior steps and love to point out charts on the wall during tours, but only some actually benefit from long-term data collection that can show them where to drill down, and where to save labor. Don’t get me wrong; many suppliers use SPC to track a process window, but they do not understand completely how it can improve yields and allow them to accept higher spec products.
A good example would be USB lines or HDMI lines. If your impedances are off on some of those lines, it's not that noticeable to a user. As an example, many devices are designed with those variances considered (considering the cable loss as well). If a supplier is “drifting” out of process control on those types of signals, it may not be as big of an issue as, for example, WiFi or Bluetooth (RF). Now you affect how far Bluetooth or WiFi can reach or the power level over time (battery drain). As a supplier, you cannot just use one global rule for high speed, and this will be the challenge going into 5G. I have spent a good part of my technical meetings explaining why this is so important to the Fab customer. My acknowledgement is that the processes are still in effect upon a return trip. By far my greatest challenges when utilizing a Consumer Product supplier base.
Page 1 of 4
Suggested Items
The Evolution of Picosecond Laser Drilling
06/19/2025 | Marcy LaRont, PCB007 MagazineIs it hard to imagine a single laser pulse reduced not only from nanoseconds to picoseconds in its pulse duration, but even to femtoseconds? Well, buckle up because it seems we are there. In this interview, Dr. Stefan Rung, technical director of laser machines at Schmoll Maschinen GmbH, traces the technology trajectory of the laser drill from the CO2 laser to cutting-edge picosecond and hybrid laser drilling systems, highlighting the benefits and limitations of each method, and demonstrating how laser innovations are shaping the future of PCB fabrication.
Day 2: More Cutting-edge Insights at the EIPC Summer Conference
06/18/2025 | Pete Starkey, I-Connect007The European Institute for the PCB Community (EIPC) summer conference took place this year in Edinburgh, Scotland, June 3-4. This is the third of three articles on the conference. The other two cover Day 1’s sessions and the opening keynote speech. Below is a recap of the second day’s sessions.
Day 1: Cutting Edge Insights at the EIPC Summer Conference
06/17/2025 | Pete Starkey, I-Connect007The European Institute for the PCB Community (EIPC) Summer Conference took place this year in Edinburgh, Scotland, June 3-4. This is the second of three articles on the conference. The other two cover the keynote speeches and Day 2 of the technical conference. Below is a recap of the first day’s sessions.
Preventing Surface Prep Defects and Ensuring Reliability
06/10/2025 | Marcy LaRont, PCB007 MagazineIn printed circuit board (PCB) fabrication, surface preparation is a critical process that ensures strong adhesion, reliable plating, and long-term product performance. Without proper surface treatment, manufacturers may encounter defects such as delamination, poor solder mask adhesion, and plating failures. This article examines key surface preparation techniques, common defects resulting from improper processes, and real-world case studies that illustrate best practices.
RF PCB Design Tips and Tricks
05/08/2025 | Cherie Litson, EPTAC MIT CID/CID+There are many great books, videos, and information online about designing PCBs for RF circuits. A few of my favorite RF sources are Hans Rosenberg, Stephen Chavez, and Rick Hartley, but there are many more. These PCB design engineers have a very good perspective on what it takes to take an RF design from schematic concept to PCB layout.