Experts Discussion with John Talbot, Tramonto Circuits
June 6, 2018 | I-Connect007 Editorial TeamEstimated reading time: 6 minutes
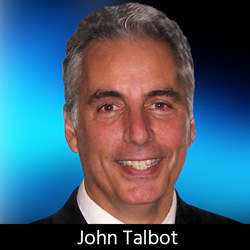
For this first issue of Flex007 Magazine, we interviewed John Talbot, president and owner of Tramonto Circuits. Headquartered in metro Minneapolis, Minnesota, Tramonto manufactures flexible and rigid PCBs for a variety of industry segments. Editors Andy Shaughnessy, Patty Goldman and Stephen Las Marias asked John to discuss the challenges and opportunities in the world of flexible circuits, and some of the trends he’s seeing in this market.
Andy Shaughnessy: John, what trends are you seeing in flex this year?
John Talbot: I think wearables will be a big topic for the next three or four years. We’re seeing a lot of interest in aerospace and automotive right now. Assembly is something near and dear to my heart; even though the flex industry has been around for a long time, it’s still a really small part of the overall industry, and we still have customers who are not comfortable with the assembly portion of flex circuits.
Shaughnessy: Do you all offer flex assembly and design?
Talbot: Yes, we build bare circuits and we do assembly and design. We still don’t see a whole lot of customers that are looking for design help. They tend to design the circuits as they would a printed board, and then get some help from us to just adjust it or revise it to make it manufacturable in the flexible circuit world.
Patty Goldman: How much of your design work is for flex?
Talbot: Maybe 10% are designed from the bottom up. Everything else is at least a design put in front of us and then we help them adjust it.
Goldman: So that 10%, do they just say, “Here, design something for us please?” Or are they just throwing up their hands and saying “We don’t even know how to design this”?
Talbot: Not quite. It’s more like they don’t have the time, or they’ve designed circuit boards for a long time, but now they’re starting to get into flexible circuits and they just need some help figuring things out, typically with the standards. For years and years, we all know what the printed circuit board industry likes about trace widths and spaces and drill hole sizes, annular rings, and solder mask clearance; all that kind of changes a little bit when it comes to the flex industry. So, 90% of what we get is people who are comfortable with circuit board standards but not so much with the flexible standards. Shaughnessy: Are flex standards keeping up with the industry, John?
Talbot: Not entirely—not for a company like ours anyway. We’re still an etch company. We are still removing copper and I think that we are seeing a pattern for several years now, of things getting smaller and tighter—smaller holes, smaller traces, and that sort of thing. Stephen Las Marias: You mentioned earlier that some of the companies are still not comfortable with the assembly of flexible circuits. Why do you think that is so?
Talbot: It’s probably two-fold, Stephen. One reason would be because they’re very comfortable with printed circuit board assembly, and two because you can’t simply put a flexible circuit through the SMT line the way you would a circuit board. There are more fixtures and more carriers; there’s more planning and more tooling required to do it.
Las Marias: Does that mean that you have to sort of customize your assembly line when you’re working on flexible circuits?
Talbot: Yes, on almost every product. Let me give you an example: If you panelize a circuit board, and you put the traditional mouse bites in that we use to hold the circuits into the panels, that panel will stay nice and rigid all the way through the screening process, the pick-and-place, and the oven. Now, if you panelize a flexible circuit, the tabs are not the same. We don’t have mouse bites necessarily. We have literally just a tab of material left open. So, handling that panel, even if you’re using fixtures and carriers, sometimes just handling the panel out of the packaging will break the tabs, and now you’ve got floppy circuits. You’re trying to screen very small patterns into a paste, and then also trying to hit it with the pick-and-place machine as well. This causes a little more of a problem than the traditional circuit board would.
Shaughnessy: What are some of the segments driving flex now? What about automotive?
Talbot: We’re seeing some automotive right now, and we’re still seeing a lot of aerospace, and medical is very high. Another topic that I would add to this is very long circuits.
Goldman: Which of the industries has the greatest influence on change or keeping you at the highest level of technology?
Talbot: That’s a hard question to answer. Medical for sure, and I wouldn’t even know after that. Medical are the customers who give us the most challenges.
Goldman: I just wondered if it was automotive, but I wouldn’t see that as quite the same kind of challenge, right?
Talbot: No, automotive for the most part doesn’t. They’re not making things as small and tight as the medical industry does.
Goldman: That’s true. The medical industry makes everything tinier and tinier.
Shaughnessy: And medical you’ve got to go deal with FDA regulations; it’s a whole different set of hoops to jump through.
Talbot: It is, and really the trick with medical is to get the design right and consistent. Once it gets approved it has to be that way for the life of the part. The main automotive challenges, I would say, involve record keeping. And for medical, whatever the process is, you have to stick with it for the life of the product.
Shaughnessy: In automotive they’re also a little more concerned with cost, right?
Talbot: Medical is, of course. So is automotive. To be honest with you, Andy, right now we’re only 24 days into the new year and nearly half of our customers are shopping all their products. This economy that we’ve had for about a year now seems to be booming and making everybody happy, and now we have a tax cut, and everybody is getting money in their pocket. That’s increasing pricing because, for instance, in 2017, payroll increased 40% at Tramonto.
Shaughnessy: A lot of companies gave out raises and ended up having lower numbers for the 4th quarter because of the raises.
Talbot: And they’re hoping that it’s going to catch up, but the big push I’m seeing right now is that by the end of 2018, you’re going to hear a lot of manufacturers say that we’re getting back to a situation where everybody is trying to save a nickel or a penny.
Shaughnessy: Have you had any orders that are using 5G?
Talbot: We don’t have anything in-house that’s a concern for high-speed right now. Even the LCP materials is legacy stuff, so we’re not seeing any new stuff like that. And to be honest, we don’t have a whole lot of communications customers. With the communications customers we do have, typically we’re building them circuits for their racks, servers and that sort of thing.
Shaughnessy: Do your customers tend to work with you from the get-go starting at the design level?
Talbot: Not all of them, Andy. Usually it’s just if they have a problem, or if they think they might have a problem. We have lots of customers who have experienced designers, and we help when they have questions.
Shaughnessy: What kind of materials do you typically use for flex?
Talbot: Standard polyimide typically, some DuPont and some Rogers and some others.
To read the full version of this article which appeared in the April 2018 issue of Flex007 Magazine, click here.
Suggested Items
BEST Inc. Introduces StikNPeel Rework Stencil for Fast, Simple and Reliable Solder Paste Printing
06/02/2025 | BEST Inc.BEST Inc., a leader in electronic component rework services, training, and products is pleased to introduce StikNPeel™ rework stencils. This innovative product is designed for printing solder paste for placement of gull wing devices such as quad flat packs (QFPs) or bottom terminated components.
See TopLine’s Next Gen Braided Solder Column Technology at SPACE TECH EXPO 2025
05/28/2025 | TopLineAerospace and Defense applications in demanding environments have a solution now in TopLine’s Braided Solder Columns, which can withstand the rigors of deep space cold and cryogenic environments.
INEMI Interim Report: Interconnection Modeling and Simulation Results for Low-Temp Materials in First-Level Interconnect
05/30/2025 | iNEMIOne of the greatest challenges of integrating different types of silicon, memory, and other extended processing units (XPUs) in a single package is in attaching these various types of chips in a reliable way.
E-tronix Announces Upcoming Webinar with ELMOTEC: Optimizing Soldering Quality and Efficiency with Robotic Automation
05/30/2025 | E-tronixE-tronix, a Stromberg Company, is excited to host an informative webinar presented by Raphael Luchs, CEO of ELMOTEC, titled "Optimize Soldering Quality and Efficiency with Robotic Automation," taking place on Wednesday, June 4, 2025 at 12:00 PM CDT.
CE3S Launches EcoClaim Solutions to Simplify Recycling and Promote Sustainable Manufacturing
05/29/2025 | CE3SCumberland Electronics Strategic Supply Solutions (CE3S), your strategic sourcing, professional solutions and distribution partner, is proud to announce the official launch of EcoClaim™ Solutions, a comprehensive recycling program designed to make responsible disposal of materials easier, more efficient, and more accessible for manufacturers.