-
- News
- Books
Featured Books
- smt007 Magazine
Latest Issues
Current IssueMoving Forward With Confidence
In this issue, we focus on sales and quoting, workforce training, new IPC leadership in the U.S. and Canada, the effects of tariffs, CFX standards, and much more—all designed to provide perspective as you move through the cloud bank of today's shifting economic market.
Intelligent Test and Inspection
Are you ready to explore the cutting-edge advancements shaping the electronics manufacturing industry? The May 2025 issue of SMT007 Magazine is packed with insights, innovations, and expert perspectives that you won’t want to miss.
Do You Have X-ray Vision?
Has X-ray’s time finally come in electronics manufacturing? Join us in this issue of SMT007 Magazine, where we answer this question and others to bring more efficiency to your bottom line.
- Articles
- Columns
- Links
- Media kit
||| MENU - smt007 Magazine
Field Trip: CID Class Sees How Flex is Made at Streamline Circuits
June 6, 2018 | Kelly Dack, CID+, EPTACEstimated reading time: 3 minutes
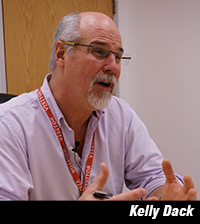
I’ve been designing PCBs and flexible circuits for decades now. I’ve heard a lot of advice over the years, but what really sticks in my mind are the wise words of a mechanical engineer I worked with back in the ’80s. He was an older guy named Clarence. One day, Clarence and I were doing a design review, and he gave me some sage advice: “Kelly, never design something that can’t be built.”
I got a chuckle out of his statement. Well, duh! Of course, it must be manufacturable. Every designer knows that, right?
But as the years went by, I engaged with more designers, design teams and manufacturing stakeholders. (In my view, the stakeholders are anyone with “skin in the game.” We don’t want to let down any of our fellow stakeholders.) I soon realized that Clarence’s words were a prophetic warning for my future career path as a PCB designer. While I was thinking “duh,” I had only begun to start reaching out to suppliers and manufacturers in the PCB industry.
As I spoke with these manufacturing stakeholders about what they need from a designer to make successful circuit boards, I heard woeful tales of PCB designs that were unmanufacturable. Some designs had lines that would etch away, or via pads that would be obliterated if over-drilled to allow for plating. Multilayer PCB stack-ups would often need to be a quarter-inch thick to achieve the specified impedance requirements. It was as if these PCB designers had never set foot inside a fabrication facility before. And that turns out to be the case more often than you might think; many designers have never visited a board shop.
After many years, I’m still designing rigid PCBs and “flexitos,” and I’m still reaching out to PCB manufacturing suppliers and making queries to find out what designers can do to help our manufacturing counterparts be successful. And you know what? I’m am hearing Clarence’s words echoing from an entire industry of fabricators: “Never design something that can’t be built.”
If you are a PCB designer, are you surprised? Maybe you are responding “Duh,” as I did 30 years ago. In the spirit of Clarence, I’m here to warn you that “duh” is an inadequate response. Unmanufacturable designs are still prevalent in the PCB industry, on a worldwide scale.
To help alleviate this issue, I’m trying to convince designers that they need to visit a board shop every now and then. I recently had the opportunity to take a group of designers on a tour of Streamline Circuits, a rigid and flex fabricator in Santa, Clara, California.
As a design instructor for EPTAC, I was teaching an IPC Certified Interconnect Designer (CID) class in Santa Clara. This four-day class drew a group of five PCB designers, all hoping to achieve their CID certification by the end of the week. During the segment of the course materials that covers the importance of reaching out to other PCB process stakeholders, I always ask the class if anyone has visited a PCB fabrication supplier to see the process up close. I am constantly amazed that a very small percentage of designers have ever done so.
During this class, I had learned that the training facility that EPTAC uses in Santa Clara is a block away from Streamline Circuits. Streamline does a lot of military and aerospace work, as well as communications and industrial electronics. The company manufactures quite a bit of multilayer flex and rigid-flex circuits, in addition to rigid boards. This would make a great field trip for my CID class!
To read this entire article, which appeared in the April 2018 issue of Flex007 Magazine, click here.
Suggested Items
Compal Announces Completion of New Automotive Electronics Facility in Poland, Signaling Strategic Growth in Europe
06/30/2025 | Compal Electronics Inc.Compal Electronics is proud to announce the completion of Phase One of its new manufacturing facility in Czeladź, Silesian Voivodeship, Poland, marking a major milestone in its strategic expansion into the European automotive electronics market.
Leadership Development Continues at Incap Slovakia
06/30/2025 | IncapIncap Slovakia has launched the first leadership development training of 2025 as part of its ongoing Team Leaders Academy programme.
Incap Estonia Recognized with Second Golden Label for Responsible Business
06/27/2025 | IncapIncap Electronics Estonia has been awarded a golden label by the Responsible Business Forum in Estonia for the second time. The responsible business label is a prestigious symbol in Estonia that identifies entrepreneurs and organisations that demonstrate excellence in environmental, social, and economic responsibility.
TRI Unveils New Multi-Camera AOI, TR7500 SIII Ultra
06/27/2025 | TRITest Research, Inc. (TRI), the leading test and inspection systems provider for the electronics manufacturing industry, proudly introduces the new TR7500 SIII Ultra.
TT Electronics Achieves ISO 13485 Medical Certification at Mexicali EMS Facility
06/27/2025 | TT ElectronicsThis milestone underscores TT Electronics’ commitment to delivering high-quality, compliant, and reliable manufacturing solutions to its global customers in healthcare and life sciences.