-
- News
- Books
Featured Books
- smt007 Magazine
Latest Issues
Current IssueMoving Forward With Confidence
In this issue, we focus on sales and quoting, workforce training, new IPC leadership in the U.S. and Canada, the effects of tariffs, CFX standards, and much more—all designed to provide perspective as you move through the cloud bank of today's shifting economic market.
Intelligent Test and Inspection
Are you ready to explore the cutting-edge advancements shaping the electronics manufacturing industry? The May 2025 issue of SMT007 Magazine is packed with insights, innovations, and expert perspectives that you won’t want to miss.
Do You Have X-ray Vision?
Has X-ray’s time finally come in electronics manufacturing? Join us in this issue of SMT007 Magazine, where we answer this question and others to bring more efficiency to your bottom line.
- Articles
- Columns
- Links
- Media kit
||| MENU - smt007 Magazine
Jigar Patel on ZESTRON’s Reliability Solutions for Class 3 Assemblies
June 14, 2018 | Patty Goldman, I-Connect007Estimated reading time: 8 minutes
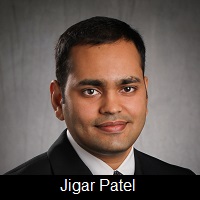
At the SMTA West Penn Expo, I had a chance to discuss a paper presented by Jigar Patel, senior application engineer at ZESTRON. Jigar explained some of the cleaning challenges with newer components and how ZESTRON helps optimize cleaning processes for their customers.
Patty Goldman: Jigar, you’re presenting a paper here at SMTA West Penn Expo, and I'm hoping you'll tell me a little bit about that paper. But first, tell me about yourself.
Jigar Patel: I work as a senior application engineer at ZESTRON, and I’ve been with ZESTRON for the last 12 years. We make cleaning agents for printed circuit board defluxing, stencil cleaning, and maintenance cleaning applications. The bulk of my job is to support customers who are implementing a cleaning process. Our existing customers who are building new board designs are starting to use new component types, so if they're facing any challenges we assist them with resolving those issues. We have a technical center where we have most types of cleaning equipment that is available in the market, like spray in-line cleaners, batch cleaners, stencil cleaners. We can replicate the cleaning process that customers have at their site. We clean the boards, document the results and prepare technical report.
Besides that, we also have an analytical center where we can do ionic contamination and ionic chromatography analysis. For post cleaning, we do visual inspection and quantitative analysis. We then submit all these results to customers.
Goldman: Tell me about the paper you’re presenting today.
Patel: Sure. I'll be discussing reliability challenges for the Class 3 assemblies and how we can resolve them. The main focus of this paper is to assist customers who are building these Class 3 assemblies and how we can help them if they're cleaning their boards.
Most of the Class 3 assemblies are used in aerospace, medical, and similar areas where they need long term reliability. The product should perform for certain time under all the conditions. Take, for example, a pacemaker. Once they put the pacemaker inside your heart, it should work for a minimum 10 years without replacing the battery. If you have any residual contamination inside the circuit board that is going inside the pacemaker, it will create leakage current. You need to ensure there is no contamination present and the battery does not drain out. This is just one example.
Goldman: What are the challenges that you're seeing these days?
Patel: Now, more and more customers are using complex package types, like 2D and 3D packages, where you have a chip on top of another chip, like PoPs. Traditional components have pretty good clearance underneath—the cleaning and rinsing solution can penetrate those areas very easily. But with this new complex package design, you have very low stand-off clearance, less than four mils or two mils. And in some cases, even less than one mil stand-off height.
Goldman: That's pretty hard to get rinsed underneath.
Patel: That's right. The surface tension of DI water is 70 dynes/cm. and under normal circumstances, water will have a very difficult time reaching those areas and cleaning during a short duration time, whether it's 10 to 15 minutes in a batch cleaner, or four or five minutes in a spray in air in-line cleaner.
A cleaning agent lowers the surface tension below 30 dynes/cm. It helps in accessing the low standoff area and it also helps in solubilizing the flux much faster. So that's the main challenge. If customers are using these complex packages and they want high reliability, they need to clean well. But cleaning with the traditional method is not going to be an option. They need to optimize the process based on the components they're using, based on the paste and flux they're using, and based on the machine they have.
Goldman: So, in your lab, you can help them optimize that, I presume?
Patel: Yes. We have all the cleaning equipment which are available in the market—spray in air in-line cleaners, batch cleaners and stencil cleaners. Typically, customers send us a board if they're working on some new design for cleaning trials. Depending on the machine they have, we'll select that machine in our lab for the trials. We'll run the cleaning trials. And after cleaning trials, we will do post-cleaning inspection. The first step is to always visually inspect the board surface, to see if there is any contamination or residue present. After that, we validate the cleaning results using either ionic contamination or ion chromatography analysis.
Goldman: Ion chromatography, I understand, is the next level of testing beyond the ROSE testing, correct?
Patel: ROSE testing just tells you the amount of contamination that is present on the board surface. It will not tell you from where it is originating. And also there's a limitation with the ROSE testing: it can extract the residue from the surface, but if it's trapped underneath the component, it will have a very hard time extracting that residue.
Goldman: When you're testing to find the optimum, can the ion chromatography tell if there's something underneath the component? How do you ensure that?
Patel: The simplest and best way to ensure there is no residue present underneath component is to remove the component and visually inspect it.
Goldman: If you're running tests, that's what you can do.
Patel: Right. If it's a test board or a dummy board you can do that. But on a production board it will be very challenging to remove components. There are ways you can ensure the cleanliness underneath some specific component, and that is by doing a localized extraction and the ionic chromatography test. With ROSE testing you submerge the entire board in an isopropanol-water mixture to do the extraction process. Then when you're checking the contamination, you divide that total amount of contamination by the surface area and it gives you microgram per square inch relative to that board.
If a customer is building a complex board, and they have specific components they're concerned about, like QFNs, MLF, BGAs, and LGAs, we can pinpoint these components by using localized extraction. The extracted solution can be injected into the ion chromatograph to get the detailed analysis, like cations, anions and weak organic acids.
Goldman: And you can tell exactly what the contaminant is?
Patel: Sure. This is a non-destructive way of doing the testing. But if you want to be 100% sure, and if you can remove the component, then always remove the component and do the visual inspection. That will give you the complete analysis.
Goldman: In the end, you can optimize their process for these components, but they're not necessarily going to go through that extensive testing, because you've already done it, right?
Patel: Exactly. We have an extensive database where we record all the test results based on what flux customers are using. We have a pretty good starting point. If a customer sends us a board, we ask them what paste and flux they're using. We know the starting parameters to select and which chemistry to go with. We are almost 80–90% where we need to be. Based on their board type, components they're using, and if the board has gone through multiple reflow cycles, we then need to do a little bit of optimization in our lab. Once we define the process parameters, we document all that in a technical report and send it to the customer for their review and approval.
Goldman: It sounds like you guys are very useful to your customers.
Patel: A core focus of ZESTRON management is to assist customers and provide all the tools to engineers that are working at ZESTRON supporting these customers. For example, customers have cleaning equipment and we have all these machines in our technical center, so we can easily replicate their process. We not only know about the chemistry, but we also know about the machines. If we go to a customer's site, to assist them with chemistry implementation in their machine, we not only adjust the chemistry, but we also program the machine, the temperature, pressure settings, and so forth.
Goldman: That's very interesting. Are there any specific conclusions to your paper that you want to talk about?
Patel: I'll be discussing a few case studies in my technical paper—the challenges and issues we have faced. The main conclusion is: When you are designing a board that you need to clean, you have to keep a few things in mind that will assist you in the cleaning process. For example, for the bottom termination components, like QFL and MLF, if you remove the solder mask underneath the component, it creates outgassing channels and also increases the stand-off height. And that helps tremendously in cleaning.
Goldman: That's an interesting point.
Patel: Yes. So those are a few things you can do from the design side. And if you already know you have to clean your assembly, you can consider all these things during the design stage. If you have the flexibility to select the solder paste and flux, you can talk to the chemical company and ask them which paste and flux is compatible for their assemblies, and easy to clean.
Goldman: That would make your job easier.
Patel: Sure. If they don't have that flexibility to make any changes—because sometimes their end customer will dictate the materials to use—we can assist them. That could make cleaning much more challenging, and we have to use more aggressive process parameters.
Goldman: The interesting thing is your customers are really the assembly people that are assembling and cleaning, right? But you need to reach the designers.
Patel: We do work with several OEMs. And based on our previous experience, some of the OEMs have considered our suggestions and they've started incorporating them during design stage. They've started using vias underneath the bottom termination components, removing the solder mask underneath low stand-off components. All those things help from the cleaning perspective.
There is a certain class of materials that can only be exposed to water, like some plastics due to temperature and chemical limitations. We've provided the list of materials that are compatible with cleaning agents to our customers so they select those materials for their boards.
Goldman: That's very interesting. Thank you so much for your time.
Patel: Thank you.
Suggested Items
Hands-On Demos Now Available for Apollo Seiko’s EF and AF Selective Soldering Lines
06/30/2025 | Apollo SeikoApollo Seiko, a leading innovator in soldering technology, is excited to spotlight its expanded lineup of EF and AF Series Selective Soldering Systems, now available for live demonstrations in its newly dedicated demo room.
Indium Corporation Expert to Present on Automotive and Industrial Solder Bonding Solutions at Global Electronics Association Workshop
06/26/2025 | IndiumIndium Corporation Principal Engineer, Advanced Materials, Andy Mackie, Ph.D., MSc, will deliver a technical presentation on innovative solder bonding solutions for automotive and industrial applications at the Global Electronics A
Fresh PCB Concepts: Assembly Challenges with Micro Components and Standard Solder Mask Practices
06/26/2025 | Team NCAB -- Column: Fresh PCB ConceptsMicro components have redefined what is possible in PCB design. With package sizes like 01005 and 0201 becoming more common in high-density layouts, designers are now expected to pack more performance into smaller spaces than ever before. While these advancements support miniaturization and functionality, they introduce new assembly challenges, particularly with traditional solder mask and legend application processes.
Knocking Down the Bone Pile: Tin Whisker Mitigation in Aerospace Applications, Part 3
06/25/2025 | Nash Bell -- Column: Knocking Down the Bone PileTin whiskers are slender, hair-like metallic growths that can develop on the surface of tin-plated electronic components. Typically measuring a few micrometers in diameter and growing several millimeters in length, they form through an electrochemical process influenced by environmental factors such as temperature variations, mechanical or compressive stress, and the aging of solder alloys.
SolderKing’s Successful Approach to Modern Soldering Needs
06/18/2025 | Nolan Johnson, I-Connect007Chris Ward, co-founder of the family-owned SolderKing, discusses his company's rapid growth and recent recognition with the King’s Award for Enterprise. Chris shares how SolderKing has achieved these award-winning levels of service in such a short timeframe. Their secret? Being flexible in a changing market, technical prowess, and strong customer support.