-
- News
- Books
Featured Books
- pcb007 Magazine
Latest Issues
Current IssueSales: From Pitch to PO
From the first cold call to finally receiving that first purchase order, the July PCB007 Magazine breaks down some critical parts of the sales stack. To up your sales game, read on!
The Hole Truth: Via Integrity in an HDI World
From the drilled hole to registration across multiple sequential lamination cycles, to the quality of your copper plating, via reliability in an HDI world is becoming an ever-greater challenge. This month we look at “The Hole Truth,” from creating the “perfect” via to how you can assure via quality and reliability, the first time, every time.
In Pursuit of Perfection: Defect Reduction
For bare PCB board fabrication, defect reduction is a critical aspect of a company's bottom line profitability. In this issue, we examine how imaging, etching, and plating processes can provide information and insight into reducing defects and increasing yields.
- Articles
- Columns
- Links
- Media kit
||| MENU - pcb007 Magazine
Estimated reading time: 3 minutes
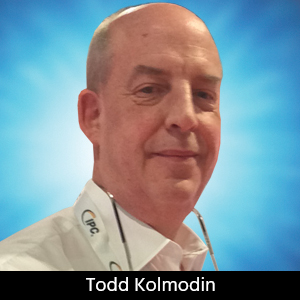
Testing Todd: What’s in your ET?
With all the buzz around automation, paperless operation, and integrated processes, it’s time to think about how the connected systems work within an electrical test department. We are all familiar with computer-aided design (CAD) and computer-aided manufacturing (CAM), but with electrical test we can also add computer-aided test (CAT) and computer-aided repair (CAR).
Back in the ‘80s, Bob Whitehead, of Electronic Packaging Company in Dallas, Texas, coined the phrase “The 4 Cs” with his vision of an integrated electrical test platform. Although Bob is no longer with us, I’m sure he would smile to see that his vision has grown even further than perhaps he imagined. As many of us can remember back in the day, ET was nothing more than a couple drilled plexiglass plates, some one-inch pins and a universal single-sided test machine capable of “self-learning,” a “known good board,” and then testing of the subsequent product. There was even the learn-comparison avenue for which you had no known good board and learned one from the lot, and then compared the rest to the learned board. It worked well for the time being unless the entire lot was bad. Bad board learned, all bad boards the same, the machine said “pass.” This would be a dangerous concept today to be sure.
So, what’s in ET today? Self-learning is a thing of the past in most cases, thank goodness. The fixture testers have evolved from the original single side, single-density versions to double density, quad density and even octal density! They can test by pre-programmed data sets, provide data logging, serialization, print bar codes, and even process the product automatically.
This is where computer-aided test (CAT) really shines. In ET today, orders can be processed simultaneously on multiple machines with floor ERP systems tracking results from any given machine. Serial number, operator, parameters, and yield can all be captured seamlessly. Between fixture testers and flying probes, the flying probes can work with the fixture testers to verify non-conforming product. This keeps the fixture testers running and not waiting to troubleshoot each board. The probers can validate if the defects are real from the fixture testers and pass the product with errors that are deemed false. This is done by the test floor integration process where data fault logs are captured, the board receives a serialized bar code, and the flying probe reads that barcode. It then reads the fault data and performs a retest based on the same CAM data used at the fixture tester. Conforming boards can automatically be marked as well.
Continuing the process, passed boards receive a passed tag while non-conforming product will receive a fault tag, complete with barcode. This fault data is also captured. We move now to CAR. The product moves to the repair/ troubleshooting area where the bar codes can be read, and the fault locations presented on a screen for easy translation to the board itself. It can be quickly determined whether the board can be reworked, or the fault requires unfavorable disposition (scrap). From here, reconciliation of the order from all facets of the ET operation can be completed. Pass/fail reconciliation, serialization, and final inspection can all be achieved.
So, we can see that the computer and automation age has hit ET as well. Many processes in ET are no longer the manual, tedious processes of the past. Still, the entire manufacturing theatre relies on the OEM to begin the process via CAD. Then the full integrated process of CAM through CAR exists under one umbrella. Even now, the once manual HiPot (dielectric breakdown) test has evolved to automated options. Flying probes are now able to automatically perform the tests that once were the tasks of a single operator.
Although an operator is still required for the machine, the tedious movements of probes to different pairs and waiting for the test is now automated. So we see in Figure 1 that, although CAD (OEM) is still the first attribute, manufacturing including the functions of ET are all in the connection equation.
Todd Kolmodin is the vice president of quality for Gardien Services USA, and an expert in electrical test and reliability issues. To read past columns, or to contact Kolmodin, click here.
This article originally appeared in the May 2018 issue of PCB007 Magazine, click here.
More Columns from Testing Todd
Testing Todd: Why 4-wire Kelvin?Testing Todd: Why TDR?
Testing Todd: Positivity Boosts Employee Morale
Testing Todd: Preparing Employees for the Long Haul
Testing Todd: Where Can We Improve?
Testing Todd: Turning Into the Wind
Testing Todd: Coming Back to Life—Design Recovery
Testing Todd: Decision Time—Invest or Delegate?