-
- News
- Books
Featured Books
- smt007 Magazine
Latest Issues
Current IssueMoving Forward With Confidence
In this issue, we focus on sales and quoting, workforce training, new IPC leadership in the U.S. and Canada, the effects of tariffs, CFX standards, and much more—all designed to provide perspective as you move through the cloud bank of today's shifting economic market.
Intelligent Test and Inspection
Are you ready to explore the cutting-edge advancements shaping the electronics manufacturing industry? The May 2025 issue of SMT007 Magazine is packed with insights, innovations, and expert perspectives that you won’t want to miss.
Do You Have X-ray Vision?
Has X-ray’s time finally come in electronics manufacturing? Join us in this issue of SMT007 Magazine, where we answer this question and others to bring more efficiency to your bottom line.
- Articles
- Columns
- Links
- Media kit
||| MENU - smt007 Magazine
Tackling Reliability Challenges in Low-Temperature Soldering
July 18, 2018 | Barry Matties and Stephen Las Marias, I-Connect007Estimated reading time: 5 minutes
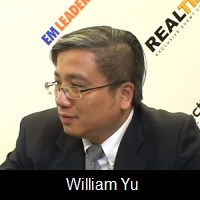
William Yu, senior technical services manager for Alpha Assembly Solutions, recently shared with I-Connect007 the challenges when it comes to the reliability of low-temperature solder pastes and soldering strategies to overcome these issues.
Barry Matties: First, tell us a little bit about Alpha and what you do.
William Yu: I’m the technical services manager for Alpha, and we are a material supplier. I support all the customers with issues in the field. We provide training to customers and introduce our new products to customers.
Matties: As a technical services manager, you are helping your customers in their process?
Yu: Yes. Mostly, we face line process engineers, but sometimes we also need to face other departments like quality or production, to help improve performance, the process yields or sometimes increasing throughputs to help them to get better yields.
Matties: What are some of the common mistakes or needed areas of improvement that you see in the industry?
Yu: Mostly, we consider printing to be the issue. Another is related to the drawings. Sometimes, the customer wants to get new business, and we'll ask for some questions in their reliability. It’s quite a wide range of questions from customers.
Matties: One product that you have is your low-temperature solder paste. What was the drive behind bringing this product to market?
Yu: This product is for the soldering performance and soldering reliability. As we know, our consumer products like smartphones and laptops are becoming thinner. So, the related BGA components are becoming thinner. The issue is not just the BGA warpage and the PCB warpage; sometimes, there are also the mismatch between these two components—the CTE difference—which will result in having more head-in-pillow, or non-wet open defects. We consider it the middle problem in the production lines. We want to help customers reduce this kind of issue in the field. This is one key reason we provide these components to customers.
Initially, we didn’t get a very good start because while we almost have 10 years’ experience in low-temperature soldering, we haven’t been in BGA soldering area before. This is where the issue is coming from—BGA soldering—because of the warpage caused by the mismatch between the CTE of the BGA and the PCB.
Matties: When you say a mismatch, is that from a design point of view? Could the board be designed differently to help alleviate or solve that problem?
Yu: Yes. You can say that a customer could solve this issue from the design stage; but sometimes, it’s difficult. If you want to implement the function of your boards, sometimes the only choice is some special components. So, the function was fixed, the components were fixed, but there’s a mismatch.
Matties: They knew it?
Yu: Yes.
Matties: And they’re relying on the assembler to do a magic job.
Yu: Yes.
Matties: When someone has an ongoing problem like this, what advice would you give them to start looking to prevent this issue?
Yu: Before it goes in the process, we would have the satisfactory file, the alloy products. We will advise customers to modify their stencil, design, and reflow process, like using nitrogen to improve it. But, sometimes, prompt action cannot cover the problem. So, we introduced our low-temperature material.
Matties: How is this product being received? Is the marketplace performance what you expected?
Yu: Currently, some data we know is if the soldering temperature decreased by 50 degrees from related components, it can reduce warpage by 10%. So, less warpage means better soldering.
Stephen Las Marias: Some of the engineers I’ve talked to are saying that when it comes to low-temperature solder, there are still some issues when it comes to the electromechanical reliability. What can you say about that?
Yu: Because our alloy is different with SAC-305, the mechanical reliability data is not the same as SAC-305. But the data from our internal testing is almost 90% similar with SAC-305 on mechanical. Further, it has similar cycle reliability. Even the internal testing with the component level is better than SAC-305.
Las Marias: You mentioned earlier something about nitrogen increasingly being used now because of head-in-pillow and non-wet open. Tell us more about this, as nitrogen has been in use for a while, yet they are now using it more now.
Yu: For us, when we designed the new alloy and the new products, we also considered the customer costs, so when we designed it, we used this solder paste into air reflow to save the electrical cost to customers. But from the component level, they will still accommodate the soldering and the nitrogen, but we can work with air flow in the process to help customers save on cost.
Matties: So, it may cost more upfront, but in the long run, your total cost goes down.
Yu: Yes. The total cost will go down, and it will also impact the customer even after the first pass view.
Matties: Is there anything that we haven’t asked that you feel like we should be sharing with the industry?
Yu: This is difficult to say. Just from my experience in the field, there are two directions. One is smaller components. Another is the increasing combination of semiconductors and SMT components. So, you will need to provide a total solution to customers—not only solder paste or solder wire or something like that—you will have to provide all the things from the beginning to customers.
Matties: The complete process.
Yu: Yes.
Matties: By doing that you have more stability.
Yu: Yes, and soldering even includes the pairing, something like that, from the design or DFM. So, when we do some new product study, we always like to discuss with our customer DFM team to help understand their new technology and what they want to do. One is to help us to improve the products, but at the same time, we will also understand our customer’s final products so that we can improve our own products.
Matties: How often do you meet with these people for the DFM kind of conversations?
Yu: Most often when we discuss with them, we also will want to know what issues they may meet. Customers will always meet some soldering problem or printing problem in the process with new products and even sometimes when they design the rework process they also meet some issues. So, when we discuss this with the customers, we consider how to solve their issue or how to provide the solution from the beginning to avoid this kind of process problem in their field. Because, you know, sometimes the customer just has one solution for the process, or they just want to follow the older process to make the new products. Sometimes you need to try to change them, their ideas or their concepts, to let them improve their process.
Matties: Well, this has been very interesting. Thank you so much. We appreciate your time very much.
Las Marias: Thank you.
Yu: You’re welcome.
Suggested Items
Hands-On Demos Now Available for Apollo Seiko’s EF and AF Selective Soldering Lines
06/30/2025 | Apollo SeikoApollo Seiko, a leading innovator in soldering technology, is excited to spotlight its expanded lineup of EF and AF Series Selective Soldering Systems, now available for live demonstrations in its newly dedicated demo room.
Indium Corporation Expert to Present on Automotive and Industrial Solder Bonding Solutions at Global Electronics Association Workshop
06/26/2025 | IndiumIndium Corporation Principal Engineer, Advanced Materials, Andy Mackie, Ph.D., MSc, will deliver a technical presentation on innovative solder bonding solutions for automotive and industrial applications at the Global Electronics A
Fresh PCB Concepts: Assembly Challenges with Micro Components and Standard Solder Mask Practices
06/26/2025 | Team NCAB -- Column: Fresh PCB ConceptsMicro components have redefined what is possible in PCB design. With package sizes like 01005 and 0201 becoming more common in high-density layouts, designers are now expected to pack more performance into smaller spaces than ever before. While these advancements support miniaturization and functionality, they introduce new assembly challenges, particularly with traditional solder mask and legend application processes.
Knocking Down the Bone Pile: Tin Whisker Mitigation in Aerospace Applications, Part 3
06/25/2025 | Nash Bell -- Column: Knocking Down the Bone PileTin whiskers are slender, hair-like metallic growths that can develop on the surface of tin-plated electronic components. Typically measuring a few micrometers in diameter and growing several millimeters in length, they form through an electrochemical process influenced by environmental factors such as temperature variations, mechanical or compressive stress, and the aging of solder alloys.
SolderKing’s Successful Approach to Modern Soldering Needs
06/18/2025 | Nolan Johnson, I-Connect007Chris Ward, co-founder of the family-owned SolderKing, discusses his company's rapid growth and recent recognition with the King’s Award for Enterprise. Chris shares how SolderKing has achieved these award-winning levels of service in such a short timeframe. Their secret? Being flexible in a changing market, technical prowess, and strong customer support.