-
- News
- Books
Featured Books
- smt007 Magazine
Latest Issues
Current IssueMoving Forward With Confidence
In this issue, we focus on sales and quoting, workforce training, new IPC leadership in the U.S. and Canada, the effects of tariffs, CFX standards, and much more—all designed to provide perspective as you move through the cloud bank of today's shifting economic market.
Intelligent Test and Inspection
Are you ready to explore the cutting-edge advancements shaping the electronics manufacturing industry? The May 2025 issue of SMT007 Magazine is packed with insights, innovations, and expert perspectives that you won’t want to miss.
Do You Have X-ray Vision?
Has X-ray’s time finally come in electronics manufacturing? Join us in this issue of SMT007 Magazine, where we answer this question and others to bring more efficiency to your bottom line.
- Articles
- Columns
- Links
- Media kit
||| MENU - smt007 Magazine
Conversation with… Vexos: Doing It Right the First Time
July 23, 2018 | Stephen Las Marias, I-Connect007Estimated reading time: 5 minutes
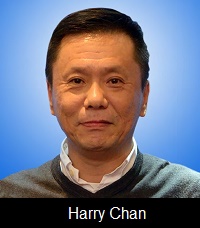
Vexos Corp. is a high-mix, low to mid-volume EMS provider with facilities in the United States, Canada and China. Vexos primarily focuses within the automotive, industrial, networking, communication, medical and security market segments.
Harry Chan, Deputy GM and VP Manufacturing for Vexos Shenzhen, is responsible for all aspects of manufacturing through continuous process improvement, production management, and development of manufacturing talent and teams. In an email interview with SMT007 Magazine, he shared the challenges when dealing with flexible circuit assemblies, and strategies and techniques to address them.
Stephen Las Marias: What’s driving the increasing demand for flex and flex assemblies?
Harry Chan: The major factor for flex circuits is new technology and the need to work with PCBAs that can be manipulated to conform to the finished product. Also, moving to smaller devices means limited space allocation for key components. As OEMs and device manufacturers work with smaller components for their products, flex circuits provide a viable solution.
Las Marias: What are the top three challenges when it comes to flexible circuit assembly?
Chan: We have developed key processes through our manufacturing systems to better manage the way we build products that use flex circuits. The most common areas we encounter are:
1. Flatness and temperature profile control in the SMT process: Understanding the nature of the board and controlling environment at the SMT level is very important to the success of the product.
2. Difficult or impossible to repair/rework: Sometimes, we come across RMA request from our customers that can be a challenge from a repair or rework standpoint.
3. Handling/storage issues: We adhere to proper storage conditions. Vexos has key handling and manufacturing processes in place to ensure we meet these challenges when handling or storing flex printed circuits boards.
Las Marias: What strategies do you employ to address these challenges?
Chan: Our strategy is, do it right the first time (DIRTFT). Early manufacturing engineering is very important; we start from design level to minimize the unnecessary cost and manufacturing impact. We review the design with the customer in the early stages and provide flex circuit layout design guidelines. We replace or minimize the design to rigid-flex circuits, if there is no special size, weight, impedance, electrical noise, or other limitations.
Las Marias: How different is the assembly of flex circuits from rigid circuits, and what are the critical factors to consider?
Chan: There are several key factors that must coincide when working with customers that require a solution using flex circuit boards—these are technology through to manufacturability and the landed cost.
1. Cost efficiency: Manufacturing and assembly costs are significantly more expensive compared with rigid-flex circuits.
2. SMT process: Special assembly carriers are required to control the flex circuit flatness during the screen printing/SMT and other processes.
3. Repair/rework: Difficult or impossible to repair/rework.
Las Marias: How do you ensure flex circuit assembly success?
Chan: Controlling the manufacturing processes can minimize the manufacturing issues.
1. Storage: Requires proper storage conditions.
2. Baking: Requires proper baking before flex SMT.
3. Assembly carrier: Special design assembly carrier required to keep the flex circuitry flat during the screen printing/SMT processes, etc.
4. Solder paste: Selecting low-temperature solder pastes (i.e., ALPHA OM-550) can minimize any delamination or heat damage after reflow.
5. Soldering wire: Selecting the low-temperature soldering wire can minimize any delamination or heat damage during the hand soldering/repair or rework process.
Las Marias: What are the best practices to consider when dealing with flex circuit assembly?
Chan: Due to the flexible circuit technology, certain design and assembly considerations must be accounted for. Fortunately, the design rules for flex circuits are very similar to the design rules for traditional PCBs. That is, the designer must pay attention to certain design aspects: minimum hole sizes, minimum trace widths, minimum space between traces and pads, minimum distances to design edges, flex circuit/board outline tolerances, distance of copper geometries from flex circuit/board edges, and copper and overall design thicknesses.
Traditional PCBs and flex circuits share some, but not all, of the manufacturing process steps. For instance, the flex material—usually copper clad polyimide—is selected, drilled, plated, photo-imaged, developed and etched just like the traditional PCB process. The next step, also similar for both PCBs and flex circuits, involves the panels being baked to remove any moisture from the wet processes. It is after this step where the traditional PCB and flex circuit processes begin to differ. Instead of going to the solder mask station, as would happen with traditional PCBs, flex circuits go to the coverlay station.
1. PCB layout design support: Review and provide flex layout design guidelines to the designer.
2. Manufacturing tooling design: Review and design the proper assembly carries.
3. Manufacturing process: Review and create the proper assembly processes for SMT/hand solder and repair or other processes.
Las Marias: What can you say to our readers about choosing EMS partners for their flex circuit assemblies?
Chan: Choose the right manufacturing partners with a proven track record. From small consumer handheld products to sophisticated medical or avionics systems, flex circuits are integral to almost every product that we use today. The demand for more compact, high-performance products and a competitive market has brought flex circuit technology into sharp focus. Product quality, viability, performance and cost all depend on your flex circuit design.
While fulfilling our customer needs is critical, success and profitability also depend on how the manufacturing partner can support the product design and development process. With applications and materials continually being designed and developed, the latest technology promises to revolutionize many aspects of electronic circuit design.
It’s important to consider the following key areas when choosing an EMS provider:
• Make sure your EMS provider has experience in flex circuit assembly
• Ensure your EMS provider is involved in your flex layout design and support
• Know whether your EMS provider can give flex design layout guidelines
Las Marias: How do you see the flex circuit assembly market in the next 12 to 18 months?
Chan: I see the flex circuit market continuing to grow. The growth is largely fueled by the Internet of Things movement. With everything becoming interconnected in cars, homes, and mobile devices, the requirement for flex circuits will grow.
Las Marias: Do you have any final comments?
Chan: Although it seems that an assembly is an assembly is an assembly, that is not always the case. Working with flex circuits brings unique challenges and unless you have been working with them repeatedly, an assembler will not know what pitfalls to avoid. When you couple the component knowledge, flex and rigid-flex circuits with the manufacturing acumen, you have a winning combination.
Las Marias: Thank you very much, Harry.
Chan: Thank you.
Suggested Items
Hands-On Demos Now Available for Apollo Seiko’s EF and AF Selective Soldering Lines
06/30/2025 | Apollo SeikoApollo Seiko, a leading innovator in soldering technology, is excited to spotlight its expanded lineup of EF and AF Series Selective Soldering Systems, now available for live demonstrations in its newly dedicated demo room.
SolderKing’s Successful Approach to Modern Soldering Needs
06/18/2025 | Nolan Johnson, I-Connect007Chris Ward, co-founder of the family-owned SolderKing, discusses his company's rapid growth and recent recognition with the King’s Award for Enterprise. Chris shares how SolderKing has achieved these award-winning levels of service in such a short timeframe. Their secret? Being flexible in a changing market, technical prowess, and strong customer support.
E-tronix Announces Upcoming Webinar with ELMOTEC: Optimizing Soldering Quality and Efficiency with Robotic Automation
05/30/2025 | E-tronixE-tronix, a Stromberg Company, is excited to host an informative webinar presented by Raphael Luchs, CEO of ELMOTEC, titled "Optimize Soldering Quality and Efficiency with Robotic Automation," taking place on Wednesday, June 4, 2025 at 12:00 PM CDT.
SMTA Releases Final Batch of Training Resources Donated by Bob Willis
05/29/2025 | SMTAThe Surface Mount Technology Association (SMTA) announces the release of several more webinars, poster sets, and photo libraries to conclude a generous donation from renowned industry expert Bob Willis.
Altus Supports Phoenix Systems in Advancing THT Assembly with Robotic Soldering
05/27/2025 | Altus GroupAltus Group, a leading distributor of capital equipment in the UK and Ireland, has successfully supported Phoenix Systems UK Ltd in its investment in robotic soldering technology to further enhance its through-hole technology (THT) assembly processes.