-
- News
- Books
Featured Books
- smt007 Magazine
Latest Issues
Current IssueSpotlight on India
We invite you on a virtual tour of India’s thriving ecosystem, guided by the Global Electronics Association’s India office staff, who share their insights into the region’s growth and opportunities.
Supply Chain Strategies
A successful brand is built on strong customer relationships—anchored by a well-orchestrated supply chain at its core. This month, we look at how managing your supply chain directly influences customer perception.
What's Your Sweet Spot?
Are you in a niche that’s growing or shrinking? Is it time to reassess and refocus? We spotlight companies thriving by redefining or reinforcing their niche. What are their insights?
- Articles
- Columns
- Links
- Media kit
||| MENU - smt007 Magazine
How Investment in Staff Well-Being Impacts Manufacturing Productivity
August 9, 2018 | Sue Poole, JJS ManufacturingEstimated reading time: 3 minutes
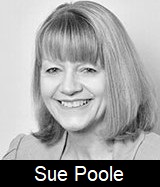
Improved productivity is one of the primary measures of success within manufacturing. And as manufacturers seek to address the challenges of increasing efficiency, there's a greater emphasis on the value of high-performance working practices such as Lean manufacturing.
At the heart of the Lean methodology is the commitment to maximizing customer value while at the same time minimizing waste.
The Lean manufacturing approach relies on employees being able to manage multiple metrics or processes. It can also demand higher levels of accountability and the capacity to focus on more complex and interdependent tasks.
When done correctly, it can lead to huge improvements in manufacturing productivity, product quality, cost-effectiveness and competitiveness.
But, as a recent report commissioned by the EEF has highlighted, the emphasis on continual quality improvement processes can also have an indirect effect on employee health and well-being.
The Unlocking Employee Productivity report was published in May 2018 to coincide with the UK's mental health awareness week and draws on the responses of more than 100 manufacturing businesses in the UK and Europe.
The study provides evidence of the relationship between performance and productivity and it shares some compelling sector-focused insights—featuring case study interviews with four firms that are actively engaged in initiatives to improve employee well-being in the workplace.
The Business Case for Investing in Well-being
According to the report, while many employees can be motivated and stimulated by the increased pressures and pace of work that Lean manufacturing requires, for others these same pressures can trigger psychological or physical stress - often leading to lower engagement, reduced satisfaction and poorer performance.
The concept of individual health and well-being can encompass a combination of physical, mental and emotional elements. And, while these are often influenced by non-work factors, the effects can have a direct impact on their work environment and levels of productivity.
The report cites for example the fact that more than 70 million working days are lost each year in the UK due to mental illness. Crucially too, it references recent US research that has found that improving mental well-being at work can boost employee productivity by 10%.
When it comes to issue of physical health and safety in the UK manufacturing sector, more than 60% of the manufacturers surveyed said they were committed to assessing the risk of physical injury and to promoting physical safety in the workplace.
For just under a third (31.9%) of respondents, a key motivation was the desire to improve employee engagement. While 28.6% of respondents said their most significant driver was reducing absence due to sickness.
In sharp contrast though, only 2.2% percentage of employers said they were actively engaged in measures to support the mental health of their staff.
Workplace Well-being Initiatives
The report suggests that a significant area of opportunity lies in providing mental health and psychosocial support for employees and it recommends some practical strategies including the provision of resources, training and feedback. The aim, it says, should be to encourage greater autonomy and give employees more control over their workload and the pace and sequence of the tasks that they're responsible for.
It also offers insights into some of the health and well-being workplace initiatives currently being implemented by manufacturing firms in the UK and Europe—from companies that provide their staff with access to online mental health support, to those that are offering on-site flu jabs, nutrition advice, healthier on-site meal options, outsourced occupational health services and workplace exercise programs.
There's no doubt that Lean manufacturing, and similar process efficiency measures, are key to competitiveness, efficiency and productivity within manufacturing. But how happy and well your employees are at work can also be a vital contributor to success.
As the report emphasizes, employees who are happier and more fulfilled, who enjoy autonomy and control in their jobs and who experience less strain and anxiety as a result of their work will often be higher performing and more productive than their competitors.
This article originally appeared on the JJS Manufacturing blog, which can be found here.
Testimonial
"Our marketing partnership with I-Connect007 is already delivering. Just a day after our press release went live, we received a direct inquiry about our updated products!"
Rachael Temple - AlltematedSuggested Items
Electronic Components Market Update
10/04/2018 | Daniella Baldock, JJS ManufacturingUnfortunately, there is still no end in sight to the electronic component shortage, and some lead-times are being quoted with 2019 and even 2020 delivery dates! So if you are working with an EMS provider, it remains vital that you communicate and share forecast information with them. You may also want to start looking at the option of fitting, or designing in, smaller components to your PCB assemblies.
What SMT Component Shortages Mean for Design and Manufacturing Engineers
09/13/2018 | Russell Poppe, JJS ManufacturingMuch has been written about the increasing shortages of electronic components such as MLCCs, chip resistors and other semiconductor devices. And the manufacturing industry is now seeing price increases and greatly extended lead times. It seems the situation is likely to get rapidly worse rather than better. What can we do? Read on.
5 Supply Chain Questions to Ask Your Assembly Partner
08/16/2018 | Neil Sharp, JJS ManufacturingA key question for any OEM who may be considering outsourcing production is whether to maintain its existing supply chain or to hand those crucial purchasing decisions over to its assembly partner. This article highlights five questions to ask a potential assembly partner before handing over the responsibility for your supply chain management.
Overcoming Growth Challenges
07/19/2018 | Neil Sharp, JJS ManufacturingGrowth is usually seen by manufacturers as a good thing—a sign of success and a result of hard work. But if this growth isn’t planned for, or the manufacturer can’t react in time, growth can cause the same devastating results as if the business was in decline. This article looks at seven common areas that can cause manufacturers a headache when their business is growing, along with solutions to help ease the pain.
How to Apply for a Graduate Scheme in Manufacturing
06/21/2018 | Neil Sharp, JJS ManufacturingThere are a whole host of benefits which make graduate schemes within the UK manufacturing industry a popular career choice. You get paid while you train, you gain invaluable on-the-job experience within your chosen sector, you develop a breadth of new technical and business skills and there’s an opportunity to continue your academic studies while you work.