-
- News
- Books
Featured Books
- smt007 Magazine
Latest Issues
Current IssueSpotlight on India
We invite you on a virtual tour of India’s thriving ecosystem, guided by the Global Electronics Association’s India office staff, who share their insights into the region’s growth and opportunities.
Supply Chain Strategies
A successful brand is built on strong customer relationships—anchored by a well-orchestrated supply chain at its core. This month, we look at how managing your supply chain directly influences customer perception.
What's Your Sweet Spot?
Are you in a niche that’s growing or shrinking? Is it time to reassess and refocus? We spotlight companies thriving by redefining or reinforcing their niche. What are their insights?
- Articles
- Columns
- Links
- Media kit
||| MENU - smt007 Magazine
What SMT Component Shortages Mean for Design and Manufacturing Engineers
September 13, 2018 | Russell Poppe, JJS ManufacturingEstimated reading time: 4 minutes
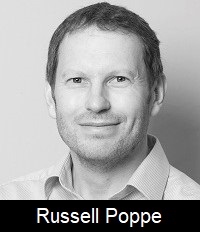
Much has been written about the increasing shortages of multilayer ceramic capacitors (MLCC), surface mount (SMT) resistors and other semiconductor devices. Right now, we are seeing price increases and greatly extended lead times. In some cases, the delivery time is so long that the component is all but unavailable, and there has been a vast increase in devices notified as "end of life" and due for obsolescence.
Where components can be found, it is quite possible that they will be offered in smaller package sizes than before. According to a recent TTi MLCC Market update, manufacturers are migrating to smaller package sizes. We might find, for example, the popular 100nF capacitor soon only being available in 0201 or 01005 packages.
It seems the situation is likely to get rapidly worse rather than better. Given that product still needs to be manufactured and sold, it going to be down to design and manufacturing engineers to come up with solutions, and fast.
So, what are our options?
1. Can we fit smaller SMT components on PCB pads designed for larger devices?
Maybe. Unfortunately, there is no straight answer as it very much depends on the overall PCB design. The component size and the PCB pad design will determine how much of the device can sit on the pad and how good the solder joint can be. Standard sizes for components and pads or ‘land patterns’ are defined by IPC 7531, but for a variety of reasons designs can be slightly different, and maybe more or less favorable to using ‘wrong size’ components. As a worst case you might find something like the following for the smaller components:
If it does appear possible, it will probably be necessary to re-design the solder stencil. Careful stencil design, very accurate component placement and reflow profiling can reduce the risk of unwanted defects such as ‘tombstoning’. Without a change to the stencil aperture, the applied solder will try to ‘wet’ over the whole pad, which being too large for the device can pull it away from the pad.
It might be possible to get the PCB manufacturer to alter the solder resist to cover more of the pad, but again this can present printing problems.
Smaller components might also make it necessary to reduce the stencil thickness from say 5 to 4 thou. A ‘stepped’ stencil could be required to ensure the right amount of solder paste is applied to the right areas of the PCB, or perhaps use solder paste jetting instead of printing.
If you are looking to comply with IPC-A-610 standards, then you might find this approach is unsuitable. There could also be implications for longer term product reliability due to the solder joints being less than ideal.
Inspection and test also need considering. In particular, automated optical inspection (AOI) will need to be adjusted. First time pass yields are likely to decrease, and a larger amount of rework may be necessary.
Of course, when specifying alternative components their performance characteristics need to be correct too; smaller components may well have different operating voltages, heat dissipation etc. making them unsuitable for your circuit. ‘Track and gap’ requirements might need to be considered.
It is also worth checking that your SMT assembly equipment is capable of placing smaller components as 0402, or even larger, could be the limit for older equipment.
2. Can we re-design the PCB for smaller components?
Yes, and this is probably the preferred option, though much of the above still applies in terms of checking production capability, component characteristics and the need to amend stencils and inspection. Of course, testing and approvals processes will also need to be considered.
It might be possible to replace a few components with smaller parts, and keep the rest the same, by using a stepped stencil as discussed above. However, if the new smaller components are widely distributed across the PCB, decoupling capacitors for example, then a more extensive re-design might be required to ensure all components are small enough to use the same stencil thickness. Alternatively, it may be necessary to consider jet printing the solder paste.
If space allows, designing pads to accommodate two component sizes could help. This could be by having parallel components (with one not fitted) or by adjusting the pad size and gap; though of course consideration needs to be given to the solder joint that can achieved.
What should we do now?
In summary, the best approach is to discuss and evaluate what is possible with your manufacturing engineers before committing to any smaller components, as they will most probably raise some challenges—and costs—if indeed the parts are useable at all.
Ensuring the electrical integrity of the circuit is maintained is also vital, and, of course, any testing and/or approvals processes must be planned in.
Most important of all, though, is to start planning now. Your electronics manufacturing services (EMS) provider may have done a great job so far shielding you from this issue and securing stocks on behalf but there’s a limit to what they will be able to achieve as the months roll by without your input.
Testimonial
"We’re proud to call I-Connect007 a trusted partner. Their innovative approach and industry insight made our podcast collaboration a success by connecting us with the right audience and delivering real results."
Julia McCaffrey - NCAB GroupSuggested Items
Absolute EMS: The Science of the Perfect Solder Joint
09/05/2025 | Absolute EMS, Inc.Absolute EMS, Inc., a six-time award-winning provider of fast turnaround, turnkey contract electronic manufacturing services (EMS), is drawing attention to the critical role of 3D Solder Paste Inspection (SPI) in ensuring the reliability of both FLEX and rigid printed circuit board assemblies (PCBAs).
Indium Corporation to Highlight High-Reliability Solder Solutions at SMTA Guadalajara Expo
09/04/2025 | Indium CorporationIndium Corporation, a leading materials refiner, smelter, manufacturer, and supplier to the global electronics, semiconductor, thin-film, and thermal management markets, will feature a range of innovative, high-reliability solder products for printed circuit board assembly (PCBA) at the SMTA Guadalajara Expo and Tech Forum, to be held September 17-18 in Guadalajara, Mexico.
Dr. Jennie Hwang to Present on ‘Solder Joint Reliability’ at SMTA International 2025
09/03/2025 | Dr. Jennie HwangDr. Jennie Hwang to address “Solder Joint Reliability” at the 2025 SMTA International Conference on Monday, October 20. Leveraging her decades of extensive real-world experiences and deep knowledge,
Indium to Highlight Energy-Efficient, High-Reliability Solder Solutions for EV and Electronics at Productronica India
09/03/2025 | Indium CorporationIndium Corporation, a leading materials refiner, smelter, manufacturer, and supplier to the global electronics, semiconductor, electric vehicle (EV), thin-film, and thermal management markets, will feature a range of sustainable, high-reliability solder products at Productronica India, to be held September 17-19 in Bengaluru, India.
Altus Supports Datalink Electronics with Advanced Selective Soldering Solution to Boost Manufacturing Efficiency
09/02/2025 | Altus GroupDatalink Electronics has partnered with Altus Group to integrate a cutting-edge automated soldering solution, enhancing its production capabilities and reinforcing its strategic focus on quality, automation, and scalability.