-
- News
- Books
Featured Books
- smt007 Magazine
Latest Issues
Current IssueWhat's Your Sweet Spot?
Are you in a niche that’s growing or shrinking? Is it time to reassess and refocus? We spotlight companies thriving by redefining or reinforcing their niche. What are their insights?
Moving Forward With Confidence
In this issue, we focus on sales and quoting, workforce training, new IPC leadership in the U.S. and Canada, the effects of tariffs, CFX standards, and much more—all designed to provide perspective as you move through the cloud bank of today's shifting economic market.
Intelligent Test and Inspection
Are you ready to explore the cutting-edge advancements shaping the electronics manufacturing industry? The May 2025 issue of SMT007 Magazine is packed with insights, innovations, and expert perspectives that you won’t want to miss.
- Articles
- Columns
- Links
- Media kit
||| MENU - smt007 Magazine
We Have the Best Practice for That
August 13, 2018 | Stephen Las Marias, I-Connect007Estimated reading time: 2 minutes
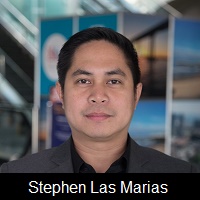
Every industry has its own set of best practices. When I was working as a clerk in a fast food restaurant during my college days, the prep station—which is where the different foods to be cooked are prepared—had a big signboard reminding everyone to use the recipe cards when preparing the many different items in the menu.
Of course, those who may have been working there for several months already had likely memorized the different ingredients needed for all of the meals on the menu. But people are not perfect. Often, not following the instructions as per the recipe card resulted in a sub-standard portioning, or bad taste or texture of the food, if not worse. This is why the best practice in that particular situation is to make sure that the recipe card is right in front of you when doing the job.
The same goes in the manual assembly lines of all contract electronics manufacturers. One of the EMS facilities I visited has a separate room where the wave soldering process is being done. In that line, a group of operators are inserting through-hole devices and components into boards before they send them to the wave soldering queue. These operators have in front of them a variety of instructions regarding the components for that particular board, the picture of the component, its dimensions, and how it should be placed or inserted on the board, and more.
Even though the operators at the end of the line are just inserting a connector or two into the boards, they still need to make sure they have the instruction cards—as a best practice—to ensure the correctness of the job they are doing.
These are just a few examples of why everyone should have some best practices of sort when it comes to the many different aspects of their operations, especially in the electronics manufacturing industry. Imagine if you’re supplying for mission-critical applications where product failure is not an option.
I believe most best practices have been developed over time, based on the many different experiences that people encounter in the manufacturing line. Some may have been set in stone from day one, but others likely were borne out of the many realizations and conclusions, perhaps after a post-mortem or evaluation of the results of the process. Some may have been passed on from generation to generation of workers as some sort of tribal knowledge.
Be that as it may, it is important to institute these best practices to make sure that your processes will result in outstanding job at the end of the day.
There many different best practices to consider for the many different aspects of electronics assembly. Of course, they may not be the correct solution for your every manufacturing issue, but at least it will be worth considering these techniques, concepts, and how they may be applied in any situation.
To read the full version of the article, which appeared in the July 2018 issue of SMT007 Magazine, click here.
Suggested Items
Hands-On Demos Now Available for Apollo Seiko’s EF and AF Selective Soldering Lines
06/30/2025 | Apollo SeikoApollo Seiko, a leading innovator in soldering technology, is excited to spotlight its expanded lineup of EF and AF Series Selective Soldering Systems, now available for live demonstrations in its newly dedicated demo room.
SolderKing’s Successful Approach to Modern Soldering Needs
06/18/2025 | Nolan Johnson, I-Connect007Chris Ward, co-founder of the family-owned SolderKing, discusses his company's rapid growth and recent recognition with the King’s Award for Enterprise. Chris shares how SolderKing has achieved these award-winning levels of service in such a short timeframe. Their secret? Being flexible in a changing market, technical prowess, and strong customer support.
E-tronix Announces Upcoming Webinar with ELMOTEC: Optimizing Soldering Quality and Efficiency with Robotic Automation
05/30/2025 | E-tronixE-tronix, a Stromberg Company, is excited to host an informative webinar presented by Raphael Luchs, CEO of ELMOTEC, titled "Optimize Soldering Quality and Efficiency with Robotic Automation," taking place on Wednesday, June 4, 2025 at 12:00 PM CDT.
SMTA Releases Final Batch of Training Resources Donated by Bob Willis
05/29/2025 | SMTAThe Surface Mount Technology Association (SMTA) announces the release of several more webinars, poster sets, and photo libraries to conclude a generous donation from renowned industry expert Bob Willis.
Altus Supports Phoenix Systems in Advancing THT Assembly with Robotic Soldering
05/27/2025 | Altus GroupAltus Group, a leading distributor of capital equipment in the UK and Ireland, has successfully supported Phoenix Systems UK Ltd in its investment in robotic soldering technology to further enhance its through-hole technology (THT) assembly processes.