-
-
News
News Highlights
- Books
Featured Books
- smt007 Magazine
Latest Issues
Current IssueSpotlight on India
We invite you on a virtual tour of India’s thriving ecosystem, guided by the Global Electronics Association’s India office staff, who share their insights into the region’s growth and opportunities.
Supply Chain Strategies
A successful brand is built on strong customer relationships—anchored by a well-orchestrated supply chain at its core. This month, we look at how managing your supply chain directly influences customer perception.
What's Your Sweet Spot?
Are you in a niche that’s growing or shrinking? Is it time to reassess and refocus? We spotlight companies thriving by redefining or reinforcing their niche. What are their insights?
- Articles
- Columns
- Links
- Media kit
||| MENU - smt007 Magazine
Use of Lean Manufacturing Principles Enhances Quality and Productivity
August 22, 2018 | Mike Baldwin, Spectrum Assembly Inc.Estimated reading time: 2 minutes
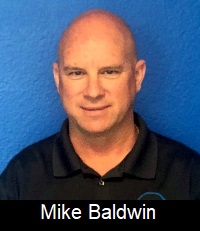
Regional EMS providers typically provide greater flexibility and responsiveness to their box build customers via use of work-cell-based batch assembly processes. Production volumes are fairly low, so the creation of dedicated continuous flow paced assembly lines is rare. However, we often see larger footprints and more complex projects with higher volumes.
Our cable, harness and PCBA manufacturing capabilities attract companies with products requiring complex subassemblies. As a result, it utilizes both work-cell-based and continuous-flow-line assembly in its box build assembly area.
One recent project example illustrates why this flexibility is important. The customer develops sports therapy devices used by trainers and professional sports teams. They had a next-generation product that increased functionality and, as a result, became mechanically much more complex. They needed a contract manufacturer capable of assisting them with development of mechanical manufacturing process instructions in addition to manufacturing the product. SAI helped develop the manufacturing process instructions as part of its new product introduction (NPI) services. The customer’s documentation for wire and cable assemblies, electronic assemblies, mechanical assemblies and cosmetics requirements is transmitted to the Aegis system and used to create visual work instructions that are utilized by the production team.
This project included cables, harnesses, PCBAs, electro-mechanical, fluidic, air and water subassemblies as well as chassis, sheet metal, plastics and hardware components. Routing the tubing in a limited chassis space was a challenge. Our team used the same process templates used in developing efficient wire and harness routing to route the fluidic, air and water lines. Trial builds were performed to ensure correct air pressure and water flow, and once nailed down, a tubing cut list was developed to make sure that all tubing was cut to appropriate lengths for the preferred routing. The customer validated the process. While computer modeling of this type of routing seems efficient, a routing that looks great on the computer screen can turn out to be an inefficient order of operations on the production line based on the obstacles that operators encounter during the assembly process. Having a combination of computer modelling and hands-on trial builds meant nothing was missed and that the order of operations was fully optimized.
Initially, the project was planned as a batch build process in several dedicated work cells, however, the volumes quickly outgrew that model. Our team utilized Lean manufacturing principles to redesign production flow from a cellular manufacturing process to a single conveyorized production line that integrated subassemblies with final assembly. Lean manufacturing principles were a core part of this redesign effort.
In the original process, cables, harnesses, PCBAs and subassemblies were assembled separately and pulled from stock. Final units were assembled sequentially by a pair of production operators.
The redesigned line has seven "feeder" work cells where production operators build electronic subassemblies consisting of multiple PCBAs, an onboard computer and associated harnesses; the fluidics; heating elements, cooling elements and additional subassemblies. In total, there are over 800 line items, seven custom PCBAs and 37 custom cables. At each station, operators add their subassembly to the base unit as it moves down the conveyor line. Programming, serialization, functional test, burn-in and crating are located at the end of the line. As part of this process, a 17-page device history record (DHR) is created and electronically filed for future use.
To read the full version of the article, which appeared in the July 2018 issue of SMT007 Magazine, click here.
Testimonial
"Our marketing partnership with I-Connect007 is already delivering. Just a day after our press release went live, we received a direct inquiry about our updated products!"
Rachael Temple - AlltematedSuggested Items
Summit Interconnect Names Milan Shah as Vice Chairman of the Board
08/26/2025 | Summit Interconnect, Inc.Summit Interconnect, a leading provider of advanced PCB manufacturing, today announced that Milan Shah has been named Vice Chairman of the Board.
Haylo Labs Acquires Plessey Semiconductors
08/20/2025 | Haylo LabsHaylo Labs has acquired Plessey Semiconductors, the UK’s leading innovator in microLED display technology.
50% Copper Tariffs, 100% Chip Uncertainty, and a Truce
08/19/2025 | Andy Shaughnessy, I-Connect007If you’re like me, tariffs were not on your radar screen until a few months ago, but now political rhetoric has turned to presidential action. Tariffs are front-page news with major developments coming directly from the Oval Office. These are not typical times. President Donald Trump campaigned on tariff reform, and he’s now busy revamping America’s tariff policy.
U.S. Uses Secret Trackers to Trace AI Chips Diverted to China, Sources Say
08/18/2025 | I-Connect007 Editorial TeamTwo sources told Reuters that U.S. authorities have secretly placed location trackers in some advanced chip shipments they see as at high risk of illegal diversion to China. They said the trackers are intended to locate AI chips that are sent to locations restricted by U.S. export laws, but authorities only examine some shipments.
SMT Perspectives and Prospects: Warren Buffett’s Perpetual Wisdom, Part 1
07/29/2025 | Dr. Jennie Hwang -- Column: SMT Perspectives and ProspectsOver the years, I have cherished the lessons by Warren Buffett and Charlie Munger at the Berkshire Hathaway annual shareholders meeting in Omaha, Nebraska. This year, I was among the more than 40,000 who attended the May 3 meeting. Millions more from around the world, including from the UK, Germany, Japan, China, Panama, and Guatemala, tuned in remotely and via CNBC’s livestream.