-
-
News
News Highlights
- Books
Featured Books
- smt007 Magazine
Latest Issues
Current IssueWhat's Your Sweet Spot?
Are you in a niche that’s growing or shrinking? Is it time to reassess and refocus? We spotlight companies thriving by redefining or reinforcing their niche. What are their insights?
Moving Forward With Confidence
In this issue, we focus on sales and quoting, workforce training, new IPC leadership in the U.S. and Canada, the effects of tariffs, CFX standards, and much more—all designed to provide perspective as you move through the cloud bank of today's shifting economic market.
Intelligent Test and Inspection
Are you ready to explore the cutting-edge advancements shaping the electronics manufacturing industry? The May 2025 issue of SMT007 Magazine is packed with insights, innovations, and expert perspectives that you won’t want to miss.
- Articles
- Columns
- Links
- Media kit
||| MENU - smt007 Magazine
Best Practices in Manufacturing: Wave Soldering
August 24, 2018 | Brian Morrison, Vexos Corp.Estimated reading time: 4 minutes
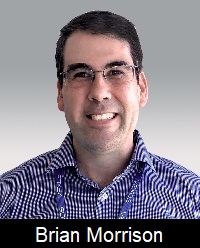
Over the years, best practices have evolved and will continue to evolve with the changing environments, company needs and challenges and what may work for one company may not necessarily be best for another. A common area sometimes overlooked versus surface mount is wave solder, which can commonly introduce significant touch up and rework if not appropriately managed.
The following recommendations are based on experiences and best practices and is not intended to be considered hard and fast rules, but rather guidelines—your situation will dictate which practices work best for your company.
This article will be focusing on common wave defects and best practices to both address, predict and proactively prevent these issues from reoccurring. Contributing elements such as component selection/ considerations, design, tooling and process will be discussed. By far the most common wave defect is bridging, which is the unwanted formation of solder between conductors. Defect contributors include component, design, tooling and process.
Solder Bridging
Component Considerations
Lead length: Specification of component lead length in the design versus the PCB thickness provides the respective protrusion of the lead into the solder during this process. Ensuring the lead length is neither too short (i.e., solder cannot reach the pin to achieve capacitary action) or too long (i.e., provides a pathway for webbing from one pin to the adjacent) can prorogate bridging for the assembly.
Best practice when specifying the component lead length is to ensure the lead length is long enough to provide the necessary heat transfer for proper wicking to provide sufficient barrel fill while neither exceeding the maximum protrusion specified as per IPC-A-610. A good rule of thumb is the length should not be longer than the distance between the two adjacent annular rings. By ensuring this is met, the probability of webbing is significantly reduced as surface tension will draw the solder to the nearest copper area. In cases where the lead length is too long, component prep and lead trimming are recommended to provide the desired length.
Other considerations related to the components themselves can be PCB contamination, component contamination, oxidation or solder mask issues.
Design Considerations
Component orientation: Particularly relevant to larger pin count connectors with at least two or more rows where orientation of the connector parallel to the wave can result in significant bridging occurrences.
Best practice is to ensure larger pin count connectors are orientated perpendicular to the wave to minimize the number of exposed trailing end pins of the connector where bridging is likely to occur. This is especially true for fine pitch. In situations where orientation cannot be accommodated, other methods such as solder thieves (effectively non-functional pads or copper features which are placed on the trailing edge to pull the solder away from the last lead to prevent bridging) can be designed either into the board or onto the selective wave pallet to minimize bridging.
Tooling Considerations
Some best practices in selective solder pallet design include proper PCB orientation in the selective wave pallet. It is recommended to angle the board between 15–30° to help mitigate the bridging to a few pins by ensuring only a handful of pins end up as trailing pins. This is especially helpful where larger pin connectors are designed parallel to the wave direction.
Sufficiently large wave openings and solder flow channels on the bottom of the wave pallet provides sufficient solder flow and flux application, preventing pooling or areas where solder is trapped resulting in bridging. Generally, constraints such as minimum clearance from the outside edge of the annular ring to a surface mount pad drive the opening size. Recommendation is 0.100” for this distance for proper design.
Bottom side surface mount component heights can drive thicker pallet requirements and further impact the ability of the solder to flow in and out of the pocket. The aspect ratio relates to the solder opening length/ width versus the vertical travel required for the solder to reach the bottom of the PCB. The minimum ratio is 1:1 for leaded solder but increases to 1:3 for lead-free solder. That is, if the length/width is 0.150”, then the maximum vertical dimension is 0.150” for leaded solder. Violating this aspect ratio will obstruct proper flow and increase the chance of wave related defects.
Additionally, orientating the board on selective wave pallet at 15° degrees can help mitigate the bridging to a few pins. Typically, a hybrid solution of the above techniques provides the optimal solution.
Process Considerations
Selecting the right flux for the application as well as the appropriate thermal profile can have a significant impact on the formation of solder bridging, and selecting an appropriate flux for the thermal mass and heating profile required can have a significant impact on overall yield.
Generally, a higher solid content is more robust at higher temperatures and water-based fluxes do not perform as well at higher temperatures and better suited for lower thermal boards. Ensuring the pre-heat temperature and dwell time for your board is appropriate for your flux can mean the difference between a good and bad result. Burning off the flux prior to wave can result in bridging.
To read the full version of this article, which appeared in the July 2018 issue of SMT007 Magazine, click here.
Suggested Items
Happy’s Tech Talk #39: PCBs Replace Motor Windings
06/12/2025 | Happy Holden -- Column: Happy’s Tech TalkThe age of electric vehicles has arrived. If we can improve energy storage, lower the price tag of batteries, andmake them work at lower temperatures, EVs may become our favorite mode of transportation. Certainly, the motors are going through a massive change. Figure 1 shows a typical EV motor.
KYZEN Focuses on Aqueous Cleaning and Stencil Cleaning at SMTA Ontario
06/09/2025 | KYZEN'KYZEN, the global leader in innovative environmentally responsible cleaning chemistries, will exhibit at the SMTA Ontario Expo and Tech Forum, scheduled to take place Tuesday, June 17 at the Venu Event Space in Vaughan, Ontario, Canada. KYZEN will be on-site to provide information about aqueous cleaning chemistry AQUANOX A4618 and the full line of AQUANOX products.
KYZEN’s AQUANOX A4618 and AQUANOX A4727 Highlighted at SMTA Huntsville and Atlanta Expo & Tech Forums
04/08/2025 | KYZEN'KYZEN, the global leader in innovative environmentally responsible cleaning chemistries, will exhibit at the SMTA Huntsville Expo & Tech Forum, scheduled to take place Tuesday, April 22 at the Jackson Center in Huntsville, AL, and the SMTA Atlanta Expo & Tech Forum.
Indium Corporation, Industry Partners to Showcase Products 'Live@APEX'
03/10/2025 | Indium CorporationIndium Corporation®, in cooperation with its industry partners, will feature its proven solder solutions live on the show floor throughout IPC APEX Expo from March 18-20 in Anaheim, California.
Airbus-built Biomass Forest Measuring Satellite Shipped to Kourou
02/21/2025 | AirbusBiomass, the European Space Agency’s (ESA) Airbus-built satellite, has left Toulouse for its journey by ship to Kourou, French Guiana, ready for launch.