-
- News
- Books
Featured Books
- smt007 Magazine
Latest Issues
Current IssueWhat's Your Sweet Spot?
Are you in a niche that’s growing or shrinking? Is it time to reassess and refocus? We spotlight companies thriving by redefining or reinforcing their niche. What are their insights?
Moving Forward With Confidence
In this issue, we focus on sales and quoting, workforce training, new IPC leadership in the U.S. and Canada, the effects of tariffs, CFX standards, and much more—all designed to provide perspective as you move through the cloud bank of today's shifting economic market.
Intelligent Test and Inspection
Are you ready to explore the cutting-edge advancements shaping the electronics manufacturing industry? The May 2025 issue of SMT007 Magazine is packed with insights, innovations, and expert perspectives that you won’t want to miss.
- Articles
- Columns
- Links
- Media kit
||| MENU - smt007 Magazine
Getting More with Cleaning
September 10, 2018 | I-Connect007 Editorial TeamEstimated reading time: 7 minutes
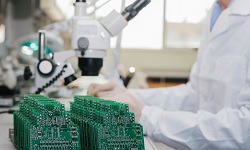
The continuing growth of the electronics industry, driven by the rapid expansion of electronics into areas such as automotive and medical, is creating a new mindset with regard to cleaning, mainly due to quality and reliability issues. Historically considered a non-value-add, cleaning is now being increasingly relied upon by manufacturers to mitigate potential board defects.
For this month’s issue of SMT007 Magazine, we invited failure analysis experts Eric Camden and Paco Solis, both lead investigators at Foresite Inc., and industry veteran Greg Smith, manager of stencil technology at BlueRing Stencils, to share their experiences with cleaning challenges in PCBAs and possible solutions.
Stephen Las Marias: What are the most critical challenges when it comes to cleaning?
Eric Camden: The critical points for cleaning these days are the bottom-terminated components in general, but with a focus on QFNs because of their low standoff height—which are very difficult to process either with water-soluble or no-clean flux. If you are trying to clean a no-clean flux from underneath a QFN, you are going to struggle, there’s no doubt about it. And I am talking about the best cleaning equipment that you can find. You still need to have a fine eye and be able to tune your cleaning process to address the QFNs. And if you can do that in general, you can say that other components will be very clean because you can effectively clean the hardest part on the board. So, from a failure analysis point, from a process reliability standpoint, from what we do in the analytical world, we see lots of issues in QFN during a wash process.
It’s very difficult to outgas the flux activators when you are starting at half a mil or 1 mil standoff height. So, really the QFNs are probably the most critical part that we see when it comes to optimizing a wash process.
Paco Solis: When it comes down to the cleaning part of it, the hydrodynamics—the flow dynamics—of the cleaning process itself, it’s one thing to have a QFN on its own without a lot of high aspect ratio architectures around it. But now, every PCBA is going to be a different, unique architecture and it may have specific requirements that impede flow dynamics. So, you just can’t put every board through in the same way. Sometimes, you have to change your orientation, your flow nozzles, or direction, to increase the flow dynamics and contact time. It’s a challenging part on its own. But the collateral architecture around it or adjacent to it can also make your issue a bit more difficult just to get chemistry or water at it.
Las Marias: Is there still a misconception when it comes to no-clean?
Solis: It depends on circuit sensitivity and architecture. And then in defense of the flux suppliers, they don’t know how and what design layout engineers and electrical engineers are going to throw at, at their products, so it’s really a little difficult sometimes to predict what’s necessary for sensitive architectures.
Las Marias: One of the issues we always hear when speaking to industry experts is the need for communication between the designers and assemblers. Is the cleaning process another issue that they should be talking about when it comes to discussions on their design and assembly?
Camden: There’s a term—design for cleanability—that’s been out there for a few years now because of some of these same issues. Some thoughts fit in to the final step of cleaning during the design process, but I think it is seen as low-value input when it comes to design, because those who design don’t always clean. Design for cleanability is something that’s out there, and it should be considered absolutely when you plan on cleaning it, because what you’re doing upfront have a negative impact on the cleaning process.
Andy Shaughnessy: What are some things that designers should do to make the cleaning process go more smoothly?
Solis: There are some architecture layers that you stuck down your trace even. We see some mistakes where layout persons are putting their legends down underneath the QFN. They are doing more and more interconnects; now you have architectures that will start impeding or there are architectures where packages are touching directly. I have some cross-section areas that show these QFNs staying at 6 microns away from the solder mask area. Basically, the core of the part is cordoned off by these architectures, so the layout engineers need to understand what the challenges are for the cleanliness and for sensitive electronics.
That is something that typically they are not involved with. Just those architectures and having to lay out those signals and the I/Os can make it more difficult just to clean.
Shaughnessy: So, they need to be in communication from the start. Because I don’t think they put this thought in the cleaning process; I don’t hear many designers talking about that.
Camden: You’ll see a group of four or five supercaps right next to four or five QFNs. You a disruption of the water flow where it can’t get repeatably underneath those QFNs, which are already hard to clean. So, those types of things just aren’t thought of. This is the circuit that needs to go on, but when you look at the placements—that’s something that needs to be thought of if you’re going to clean your boards.
Solis: Layout is extremely important. Here’s an example. There are QFNs very close to plated through-hole. Now, in our analysis, we were able to detect the through-hole flux that’s flowing underneath the via under the QFN. Because the organic acids are so different in the surface mount versus the through-hole flux, we were able to detect and verify that they are getting cross contamination from the through-hole process into the surface-mount QFN.
Shaughnessy: That’s interesting. I am sure people will be surprised to read that because I really don’t think they put a whole lot of effort into designing for cleaning.
Barry Matties: You guys focus on reliability, training, process audits. What typical problems you encounter in your audits as you go into these facilities?
Solis: There’s one interesting thing that pops out on, let’s say, a few times that I have walked the line: the conception that brush cleaning for solder balls is a positive, a value-added step. I’ve seen operators dry brushing at the flux in the final architectures. They are taking large paint brushes and dipping them in bowls of alcohol. The problem with that is the flux that is already benign, just because it had the look that there’s a little residue there, they start scrubbing it, and they have no idea that they are breaking down and solubilizing fluxes.
We call it contamination relocation. They are making it much worse, but it is perceived that alcohol cleans things, that alcohol dissolves things. But they just relocate what was good flux, now they basically shove it to the nearest surface mount architecture, so now you have collateral contamination.
Camden: The spot you are working on is clean, and then half-an-inch square around it is extremely dirty.
Solis: Now, you have a super concentration of flux and resin from weeks and weeks, or days and days, of dipping it back and forth, and now they are spreading it on clean boards.
Matties: Why is this a prevalent problem?
Solis: I think a lot of people can’t get to the thought of no-clean, and they just accept that it is a blanket term. In many factories, a lot of engineers really don’t understand what no-clean really is and how it behaves. Often, they don’t even go back and ask their flux suppliers on how they can learn more about this.
Camden: The problem is it is not a repeatable process. If you have a hundred boards and they all fail in the same manner a hundred times, that’s an easy thing to diagnose. When you are looking at rework or repair, they are not part of standard assembly operations, and they aren’t usually documented in the same manner. It’s really because rework is not always a repeatable process, and because you are not doing touch up on 100% of boards. Operator A may be doing a perfect job every time; Operator B may not be doing a perfect job every time; so, of the hundreds of boards that are touched up, even out of those, only a small percentage of failures will have that as the root cause because environments still play a role; how effective Operator A is versus Operator B, how old the cleaning brush is, things like that. There are a lot of little things that come into play to avoid failure when it comes to cleaning.
To read the full article, which appeared in the August 2018 issue of SMT007 Magazine, click here.
Suggested Items
BEST Inc. Introduces StikNPeel Rework Stencil for Fast, Simple and Reliable Solder Paste Printing
06/02/2025 | BEST Inc.BEST Inc., a leader in electronic component rework services, training, and products is pleased to introduce StikNPeel™ rework stencils. This innovative product is designed for printing solder paste for placement of gull wing devices such as quad flat packs (QFPs) or bottom terminated components.
KYZEN to Focus on Aqueous Cleaning and Stencil Cleaning at SMTA Juarez
05/20/2025 | KYZEN'KYZEN, the global leader in innovative environmentally responsible cleaning chemistries, will exhibit at the SMTA Juarez Expo and Tech Forum, scheduled to take place Thursday, June 5 at the Injectronics Convention Center in Ciudad Jarez, Chihuahua.
KYZEN to Spotlight Stencil Cleaning Solutions at SMTA Oregon
05/02/2025 | KYZEN'KYZEN, the global leader in innovative environmentally friendly cleaning chemistries, will exhibit at the SMTA Oregon Expo & Tech Forum, scheduled to take place on Tuesday, May 20 at the Wingspan Event and Conference Center in Hillsboro, OR. KYZEN’s cleaning expert Jeff Deering will be on-site at the expo providing information about stencil cleaning chemistries, including KYZEN E5631J.
KYZEN to Feature Stencil Cleaning and Aqueous Cleaners at SMTA Capital Expo and Tech Form
04/28/2025 | KYZEN'KYZEN, the global leader in innovative environmentally responsible cleaning chemistries, will exhibit at the SMTA Capital Expo and Tech Forum, scheduled to take place Thursday, May 8 at George Mason University – Mason Square in Arlington, VA.
KYZEN Focuses on Aqueous Cleaning and Stencil Cleaning at SMTA Wisconsin
04/24/2025 | KYZEN'KYZEN, the global leader in innovative environmentally responsible cleaning chemistries, will exhibit at the SMTA Wisconsin Expo and Tech Forum, scheduled to take place Tuesday, May 6 at the Crowne Plaza Milwaukee Airport. KYZEN will be on-site to provide attendees with information about aqueous cleaning chemistry AQUANOX A4618 and stencil cleaner KYZEN E5631J.