NIST’s Electro-Optic Laser Pulses 100 Times Faster Than Usual Ultrafast Light
September 28, 2018 | NISTEstimated reading time: 3 minutes
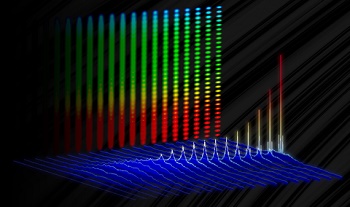
Physicists at the National Institute of Standards and Technology (NIST) have used common electronics to build a laser that pulses 100 times more often than conventional ultrafast lasers. The advance could extend the benefits of ultrafast science to new applications such as imaging of biological materials in real time.
Image caption: Illustration depicting how specific frequencies, or colors, of light (sharp peaks) emerge from the electronic background noise (blue) in NIST’s ultrafast electro-optic laser. The vertical backdrop shows how these colors combine to create an optical frequency comb, or “ruler” for light. Credit: D. Carlson/NIST
The technology for making electro-optic lasers has been around for five decades, and the idea seems alluringly simple. But until now researchers have been unable to electronically switch light to make ultrafast pulses and eliminate electronic noise, or interference.
As described in the Sept. 28 issue of Science, NIST scientists developed a filtering method to reduce the heat-induced interference that otherwise would ruin the consistency of electronically synthesized light.
“We tamed the light with an aluminum can,” project leader Scott Papp said, referring to the “cavity” in which the electronic signals are stabilized and filtered. As the signals bounce back and forth inside something like a soda can, fixed waves emerge at the strongest frequencies and block or filter out other frequencies.
NIST’s ultrafast electro-optic laser relies on this aluminum “can” to stabilize and filter the electronic signals, which bounce back and forth inside until fixed waves emerge at the strongest frequencies and block or filter out other frequencies. Credit: D. Carlson/NIST
Ultrafast refers to events lasting picoseconds (trillionths of a second) to femtoseconds (quadrillionths of a second). This is faster than the nanoscale regime, introduced to the cultural lexicon some years ago with the field of nanotechnology (nanoseconds are billionths of a second).
The conventional source of ultrafast light is an optical frequency comb, a precise “ruler” for light. Combs are usually made with sophisticated “mode-locked” lasers, which form pulses from many different colors of light waves that overlap, creating links between optical and microwave frequencies. Interoperation of optical and microwave signals powers the latest advances in communications, timekeepingand quantum sensing systems.
In contrast, NIST’s new electro-optic laser imposes microwave electronic vibrations on a continuous-wave laser operating at optical frequencies, effectively carving pulses into the light.
“In any ultrafast laser, each pulse lasts for, say, 20 femtoseconds,” lead author David Carlson said. “In mode-locked lasers, the pulses come out every 10 nanoseconds. In our electro-optic laser, the pulses come out every 100 picoseconds. So that’s the speedup here—ultrafast pulses that arrive 100 times faster or more.”
“Chemical and biological imaging is a good example of the applications for this type of laser,” Papp said. “Probing biological samples with ultrafast pulses provides both imaging and chemical makeup information. Using our technology, this kind of imaging could happen dramatically faster. So, hyperspectral imaging that currently takes a minute could happen in real time.”
To make the electro-optic laser, NIST researchers start with an infrared continuous-wave laser and create pulses with an oscillator stabilized by the cavity, which provides the equivalent of a memory to ensure all the pulses are identical. The laser produces optical pulses at a microwave rate, and each pulse is directed through a microchip waveguide structure to generate many more colors in the frequency comb.
The electro-optic laser offers unprecedented speed combined with accuracy and stability that are comparable to that of a mode-locked laser, Papp said. The laser was constructed using commercial telecommunications and microwave components, making the system very reliable. The combination of reliability and accuracy makes electro-optic combs attractive for long-term measurements of optical clock networks or communications or sensor systems in which data needs to be acquired faster than is currently possible.
The research is supported by the Air Force Office of Scientific Research, Defense Advanced Research Projects Agency, National Aeronautics and Space Administration, NIST and the National Research Council.
Suggested Items
I-Connect007’s Editor’s Choice: Five Must-Reads for the Week
07/04/2025 | Marcy LaRont, I-Connect007For our industry, we have seen several bullish market announcements over the past few weeks, including one this week by IDC on the massive growth in the global server market. We’re also closely watching global trade and nearshoring. One good example of successful nearshoring is Rehm Thermal Systems, which celebrates its 10th anniversary in Mexico and the official opening of its new building in Guadalajara.
Driving Innovation: Direct Imaging vs. Conventional Exposure
07/01/2025 | Simon Khesin -- Column: Driving InnovationMy first camera used Kodak film. I even experimented with developing photos in the bathroom, though I usually dropped the film off at a Kodak center and received the prints two weeks later, only to discover that some images were out of focus or poorly framed. Today, every smartphone contains a high-quality camera capable of producing stunning images instantly.
United Electronics Corporation Advances Manufacturing Capabilities with Schmoll MDI-ST Imaging Equipment
06/24/2025 | United Electronics CorporationUnited Electronics Corporation has successfully installed the advanced Schmoll MDI-ST (XL) imaging equipment at their advanced printed circuit board facility. This significant technology investment represents a continued commitment to delivering superior products and maintaining their position as an industry leader in precision PCB manufacturing.
Orbel Corporation Integrates Schmoll Direct Imaging
06/04/2025 | Schmoll AmericaOrbel Corporation in Easton, PA, proudly becomes the first PCM facility in the U.S. equipped with Schmoll’s MDI Direct Imaging system. This installation empowers Orbel to support customers with greater precision and quality.
Key Insights on Photoresist for Defect Reduction
05/21/2025 | I-Connect007 Editorial TeamIn PCB manufacturing, understanding the intricacies of the photoresist process is crucial for achieving high-quality results. Industry experts Josh Krick, a technical service engineer at IEC, and Tim Blair, a PCB imaging specialist at Tim Blair LLC, share their knowledge on the essential stages of photoresist application, highlight critical advancements in materials, and discuss common defects encountered during production. They share best practices and innovative solutions to enhance the manufacturing process, reduce defects, and ensure efficiency and reliability in high-tech applications.