-
- News
- Books
Featured Books
- pcb007 Magazine
Latest Issues
Current IssueIn Pursuit of Perfection: Defect Reduction
For bare PCB board fabrication, defect reduction is a critical aspect of a company's bottom line profitability. In this issue, we examine how imaging, etching, and plating processes can provide information and insight into reducing defects and increasing yields.
Voices of the Industry
We take the pulse of the PCB industry by sharing insights from leading fabricators and suppliers in this month's issue. We've gathered their thoughts on the new U.S. administration, spending, the war in Ukraine, and their most pressing needs. It’s an eye-opening and enlightening look behind the curtain.
The Essential Guide to Surface Finishes
We go back to basics this month with a recount of a little history, and look forward to addressing the many challenges that high density, high frequency, adhesion, SI, and corrosion concerns for harsh environments bring to the fore. We compare and contrast surface finishes by type and application, take a hard look at the many iterations of gold plating, and address palladium as a surface finish.
- Articles
- Columns
Search Console
- Links
- Media kit
||| MENU - pcb007 Magazine
Estimated reading time: 2 minutes
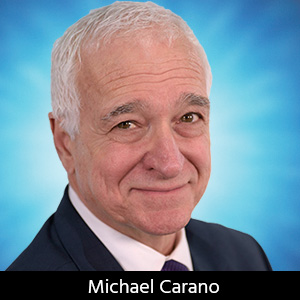
Contact Columnist Form
Trouble in Your Tank: Understanding Resist Lock-in and Extraneous Copper
It happens when you least expect it. You think you have all the process controls in place to prevent issues after etching, but either copper remains where there should be none or photoresist remains on the copper. Regardless, it is a problem and must be fixed; what are some of the causes? Resist lock-in comes in many shapes and sizes. Figure 1 shows an example of extraneous copper.
Figure 1: Extraneous copper.
The root cause of the remaining copper is often resist lock-in. In addition, several causes for the extraneous copper defect can be attributed to:
- Excessive resist lamination temperatures: This can cause thermal cure of some photoresists and difficulties in developing cleanly
- Oxidation of the panels prior to resist lamination
- Wet lamination: A thin layer of water is applied to the copper surface prior to resist lamination and requires resists that are compatible with wet lamination in order to avoid resist lock-in, which will lead to excess copper. According to Dr. Karl Dietz, one must strictly adhere to hold time and its conditions
- Dry lamination issues: This holds especially true if the post-lamination hold time is too long or temperature and humidity are too high during hold time. Such conditions favor copper oxidation. In terms of oxidation, there will be a strong tendency for the laminated resist to strongly adhere
- Exposure of the copper surface to hydrochloric acid fumes: This may cause resist lock-in even if postlamination hold times and conditions are normal. As in often the case, the resist-laminated panels for innerlayer processing may contact acid fumes from the cupric chloride etching process
- Excessive pressure on the hot roll laminators or too high a temperature
- Excessive surface roughness (topography) due to overly aggressive chemical cleaning or scrubbing of the copper surface: If you suspect lock-in due to a non-uniform or over-roughened surface, a profilometry study to measure surface roughness might be in order
- Developer/unexposed resist residues remaining on the copper surface in a random fashion: This happens due to insufficient rinsing or inadequate control of the developing solution. In the latter case, the main culprit is too low a pH in the developer solution. Another cause is partially polymerized resist that was not completely developed away
Of course, extraneous copper can sometimes be linked to obvious causes, but that does not make it any less frustrating (Figure 2). While improper handling is somewhat of a rare occurrence compared to other issues, this must be considered. For example, did the operators wear gloves? It would be a major mistake to think strong cleaners will remove human fingerprints, so tread cautiously. Surface cleanliness is critical to ensure photoresist adhesion. In addition, topography provides a mechanism to enhance adhesion of the resist to the copper surface. However, the critical aspect is to have an overall roughness of the surface area that is uniform and not overly roughened with chemical etchants or mechanical means. A surface that has major deviations from peak to valley along the surface profile will adversely affect resist adhesion. Thus, there is the potential for lock-in on one extreme and resist lifting on the other. Best practice dictates diligence with surface preparation, resist lamination, hold times between process steps (in-process is best due to minimal holds), and all processes associated with the resist exposure and development.
Michael Carano is VP of technology and business development for RBP Chemical Technology.
This column originally appeared in the September issue of PCB007 Magazine.
More Columns from Trouble in Your Tank
Trouble in Your Tank: Yield Improvement and ReliabilityTrouble in Your Tank: Causes of Plating Voids, Pre-electroless Copper
Trouble in Your Tank: Organic Addition Agents in Electrolytic Copper Plating
Trouble in Your Tank: Interconnect Defect—The Three Degrees of Separation
Trouble in Your Tank: Things You Can Do for Better Wet Process Control
Trouble in Your Tank: Processes to Support IC Substrates and Advanced Packaging, Part 5
Trouble in Your Tank: Materials for PWB Fabrication—Drillability and Metallization
Trouble in Your Tank: Supporting IC Substrates and Advanced Packaging, Part 5