Gold 'Micro Jewels' from 3D Printer Printing Pure Metal Microparts
October 30, 2018 | University of TwenteEstimated reading time: 2 minutes
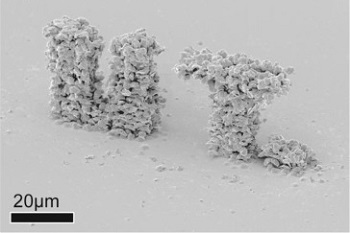
Thanks to a laser technique that ejects ultra-tiny droplets of metal, it is now possible to print 3D metal structures, not only simple ‘piles’ of droplets, but complex overhanging structures as well: like a helix of some microns in size, made of pure gold. Using this technique, it will be possible to print new 3D micro components for electronics or photonics.
By pointing an ultra-short laser pulse onto a nanometer thin metal film, a tiny metal droplet melts, it is ejected to its target and solidifies again after landing. Thanks to this technique, called laser-induced forward transfer (LIFT), the UT researchers are able to build, drop by drop, a structure with copper and gold microdroplets. The copper acts as a mechanical support for the gold. In their paper in Additive Manufacturing the researchers show, for example, a printed helix: this could act as a mechanical spring or an electric inductor at the same time. This helix is printed with copper around it: together with the helix, a copper ‘box’ is printed. In this way, a droplet that is meant for the new winding that is printed, is prevented from landing on the previous winding. After building the helix, drop by drop and layer by layer, the copper support box is etched away chemically. What remains is a helix of pure gold, no more than a few tens of microns in size.
The laser printing technique: by printing copper and gold in turn, the gold helix initially is surrounded by a copper box. Etching the copper away, results in a free standing helix of pure gold.
Top view (c) of the helix shows that it is threedimensional with a center void. In (b), it is still in the copper box
No Mixing
The volume of the metal droplets is a few femtoliters: a femtoliter is 10-15 liter. To give an impression, a femtoliter droplet has a diameter of little over one micrometer. The way the droplets are made, is by lighting the metal using an ultrashort pulse of green laser light. In this way, the copper and gold structure is built. A crucial question for the researchers was if the two metals would mix at their interface: this would have consequences for the quality of the product after etching. Research shows that there isn’t any mixing. The way a structure is built, drop by drop, results in a surface roughness, which is only about 0.3 to 0.7 microns.
Biomedical
The LIFT technique is a promising technique for other metals and combinations of metals as well. The researchers expect opportunities for materials used in 3D electronic circuit, micromechanic devices and sensing in, for example, biomedical applications. It therefore is a powerful new production technique on a very small scale: an important step towards ‘functionalisation’ of 3D printing.
The research published now, has been done by the departments of Mechanics of Solids, Surfaces and Systems (MS3) and Design, Production and Management (DPM), both part of the Engineering Technology faculty of the University of Twente. The researchers collaborated with DEMCON corporation, a spinoff company of the University of Twente.
Suggested Items
I-Connect007 Editor’s Choice: Five Must-Reads for the Week
07/11/2025 | Andy Shaughnessy, Design007 MagazineThis week, we have quite a variety of news items and articles for you. News continues to stream out of Washington, D.C., with tariffs rearing their controversial head again. Because these tariffs are targeted at overseas copper manufacturers, this news has a direct effect on our industry.I-Connect007 Editor’s Choice: Five Must-Reads for the Week
Digital Twin Concept in Copper Electroplating Process Performance
07/11/2025 | Aga Franczak, Robrecht Belis, Elsyca N.V.PCB manufacturing involves transforming a design into a physical board while meeting specific requirements. Understanding these design specifications is crucial, as they directly impact the PCB's fabrication process, performance, and yield rate. One key design specification is copper thieving—the addition of “dummy” pads across the surface that are plated along with the features designed on the outer layers. The purpose of the process is to provide a uniform distribution of copper across the outer layers to make the plating current density and plating in the holes more uniform.
Trump Copper Tariffs Spark Concern
07/10/2025 | I-Connect007 Editorial TeamPresident Donald Trump stated on July 8 that he plans to impose a 50% tariff on copper imports, sparking concern in a global industry whose output is critical to electric vehicles, military hardware, semiconductors, and a wide range of consumer goods. According to Yahoo Finance, copper futures climbed over 2% following tariff confirmation.
Happy’s Tech Talk #40: Factors in PTH Reliability—Hole Voids
07/09/2025 | Happy Holden -- Column: Happy’s Tech TalkWhen we consider via reliability, the major contributing factors are typically processing deviations. These can be subtle and not always visible. One particularly insightful column was by Mike Carano, “Causes of Plating Voids, Pre-electroless Copper,” where he outlined some of the possible causes of hole defects for both plated through-hole (PTH) and blind vias.
Trouble in Your Tank: Can You Drill the Perfect Hole?
07/07/2025 | Michael Carano -- Column: Trouble in Your TankIn the movie “Friday Night Lights,” the head football coach (played by Billy Bob Thornton) addresses his high school football team on a hot day in August in West Texas. He asks his players one question: “Can you be perfect?” That is an interesting question, in football and the printed circuit board fabrication world, where being perfect is somewhat elusive. When it comes to mechanical drilling and via formation, can you drill the perfect hole time after time?