-
- News
- Books
Featured Books
- pcb007 Magazine
Latest Issues
Current IssueInventing the Future with SEL
Two years after launching its state-of-the-art PCB facility, SEL shares lessons in vision, execution, and innovation, plus insights from industry icons and technology leaders shaping the future of PCB fabrication.
Sales: From Pitch to PO
From the first cold call to finally receiving that first purchase order, the July PCB007 Magazine breaks down some critical parts of the sales stack. To up your sales game, read on!
The Hole Truth: Via Integrity in an HDI World
From the drilled hole to registration across multiple sequential lamination cycles, to the quality of your copper plating, via reliability in an HDI world is becoming an ever-greater challenge. This month we look at “The Hole Truth,” from creating the “perfect” via to how you can assure via quality and reliability, the first time, every time.
- Articles
- Columns
- Links
- Media kit
||| MENU - pcb007 Magazine
Estimated reading time: 5 minutes
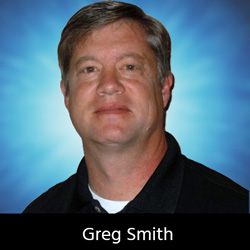
A Brief History of Solder Stencil Manufacturing
Surface-mount technology (SMT) was developed in the 1960s and became widely used in the mid-1980s. I made my first SMT stencil in the '80s, and although I’m not as old as that statement makes me feel, I remember those stencils as if it were yesterday. The first SMT stencils were made of brass and manufactured using a chemical etching process. There were no frames. The customer aligned the stencil to the PCB, taped down one side to the board or fixture, used a rubber squeegee to apply the paste, lifted the stencil, and continued until all the boards were complete. Chemical etching, also known as photochemical milling (PCM), used a photographic process to apply an etching resist to the top and bottom of the brass. Then, the PCB passed through a conveyorized etching machine to etch away the unwanted metal from the top and bottom at the same time, thus creating apertures.
During the late '80s, the chemical etching process was the primary method to manufacture SMT stencils. Stainless steel replaced brass in the early '90s. New SMT printing equipment entered the market and stencils were mounted in aluminum frames with polyester mesh, much like they are today. Electropolishing was also introduced in the '90s as components became smaller and the industry realized that smoother apertures produced better, more uniform solder paste deposits.
The late '90s to early 2000s saw the introduction of laser-cutting equipment produced strictly for cutting thin stainless steel SMT stencils. These yttrium aluminum garnet (YAG) lasers changed the dynamics of SMT stencils by allowing them to be produced faster and more accurately than ever before. The change from chemically etched stencils to laser-cut stencils was a paradigm shift that supported the move toward smaller components and the SMT industry’s continued growth. As components continued to shrink, post-processes—such as electropolishing—were still required on laser-cut stencils producing smooth aperture sidewalls to achieve the best possible paste release.
Fiber laser systems were introduced in the late 2000's and early 2010's. These new systems along with improved linear motion systems brought us into the modern age of surface mount assembly supporting the advancement of product miniaturization. These fiber laser systems continue to be the workhorse of the SMT stencil industry and continue to be improved with higher accuracy motion systems, new laser controls, and more intuitive software. Apertures cut with these laser systems release paste as well or better than any other stencil manufacturing process with location accuracy outperforming all other manufacturing methods. Improvements to these systems throughout the 2010s eliminated the need to perform post-processes, such as electroforming. More recently, nanocoatings were introduced to support the push to product miniaturization demanded by wearables and mobile electronics.
Along with changes in manufacturing methods used to create the actual SMT stencil foil, there have also been many changes to the way stencils are designed, the materials used to make SMT stencils, and the frames they are mounted to. Stencil design has always started with Gerberfiles, which are the same files used to design and manufacture PCBs. Initially, Gerber files were supplied in a standard 274-D format. This included a file that contained a list of D-codes and the X and Y location of each along with an aperture wheel describing the shape and size of each D-code. When loaded, the software would place the specific shape and size at the X and Y location. The size of apertures could be adjusted by changing the shape and/or size. One issue was some components shared the same D-code, and changes made to one component D-code would also change others. This result was not always intended.
Extended Gerber or RS-274X files came to the market in the late '90s. These files combined the aperture or D-code list into the same file as the X and Y coordinates. The software no longer needed a separate aperture wheel to load the data. Files were loaded and manipulated much easier and manipulating aperture shapes to eliminate print issues became more commonplace.
Today, we still use extended Gerber files to design SMT stencils. One of the new features current software includes is the use of intrinsic apertures. These aperture types include rounded rectangles, square thermals, thermal reliefs, and more. Another function of modern Gerber editing software is the ability to create libraries of parts made of a group of apertures. Once a group of apertures is taught as a specific component, the software looks for other identical groups and applies specific changes to each of the apertures within that group saved in the library. This ability speeds up the stencil design process and improves accuracy by removing human interaction and the need to repeat previous design changes.
Materials used in the manufacture of SMT stencils have also changed over the years. The move from brass to stainless steel was a big improvement early on, but changes to the way stainless steel is milled and post-treatments used in the manufacturing process of the foil have greatly improved the release characteristics of the modern-day SMT stencil. Primarily, companies manufacturing these new foils focused on reducing the grain structure in the alloys, and it was proven that smaller grain structure in the stainless steel produced a smoother cut with fiber lasers. Recently, these grain structures have been reduced even further and provide extremely smooth aperture walls for mainstream SMT assembly.
The frames and frame systems that keep the foil taught in the printer during the printing process have also improved. Several "frameless" systems have been offered. The early years saw many of these systems released where tensioning was done in only one or two directions. These foils were less expensive than standard stencils, but as technology advanced, these systems did not apply enough tension in all directions and were eventually obsoleted.
Other systems were developed and released in the last 10–15 years that applied tension in all directions. These systems still produce good results, take up less space on the production floor, and can be less expensive than standard framed stencils. Framed stencils have also been improved. Space-saving frames only half an inch instead of one and a half inches were introduced years ago to save storage space on the manufacturing floor. Recently, the process of using adhesive to attach the foil to the mesh has been replaced by some suppliers with a mesh welding process where a polymer strip is used to weld the foil to the mesh and eliminate the possibility of the adhesive holding the foil to the mesh from failing.
Conclusion
From chemically etching brass stencils in the '80s, to laser cutting fine grain stainless steels with modern fiber laser cutting systems today, this industry—like all others—has seen dramatic improvement. As we all know, electronics are here to stay, and product miniaturization will continue with consumer demand. In response, nanocoatings and new materials and processes will continue to develop and change to support this challenging and ever-changing industry.
More Columns from SMT Stencils 101
SMT Stencils 101: Root-cause Stencil Design, Part 3—Tearing Down BridgesSMT Stencils 101: Root-cause Stencil Design, Part 2—Tombstones
SMT Stencils 101: Root-cause Stencil Design, Part 1—Solder Balls
SMT Stencils 101: What Are Industry-standard Stencil Designs?
Overcoming the Challenges of Miniaturization with New Stencil Technologies–Solder Paste Release, Pt. 2
Overcoming the Challenges of Miniaturization with New Stencil Technologies, Part 1: Solder Paste Release