-
- News
- Books
Featured Books
- pcb007 Magazine
Latest Issues
Current IssueInventing the Future with SEL
Two years after launching its state-of-the-art PCB facility, SEL shares lessons in vision, execution, and innovation, plus insights from industry icons and technology leaders shaping the future of PCB fabrication.
Sales: From Pitch to PO
From the first cold call to finally receiving that first purchase order, the July PCB007 Magazine breaks down some critical parts of the sales stack. To up your sales game, read on!
The Hole Truth: Via Integrity in an HDI World
From the drilled hole to registration across multiple sequential lamination cycles, to the quality of your copper plating, via reliability in an HDI world is becoming an ever-greater challenge. This month we look at “The Hole Truth,” from creating the “perfect” via to how you can assure via quality and reliability, the first time, every time.
- Articles
- Columns
- Links
- Media kit
||| MENU - pcb007 Magazine
Estimated reading time: 6 minutes
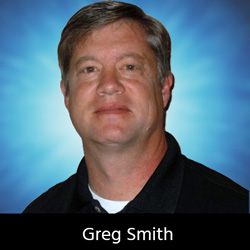
Overcoming the Challenges of Miniaturization with New Stencil Technologies, Part 1: Solder Paste Release
To maintain a successful and profitable assembly process, first-pass defects must be reduced to minimize cost, reduce assembly time, and maximize reliability. In recent years, product miniaturization continues to challenge capabilities in both design and manufacturing in the surface-mount assembly process and has the potential to increase first-pass defects more than ever. When looking at these first-pass defects, time and time again, the solder paste printing process is identified as the largest contributor. This two-part column will address the defects of insufficient paste release related to product miniaturization, and how new stencil technologies can reduce first-pass defects.
One of the largest print challenges related to product miniaturization is solder paste release. As 0201 imperial components become mainstream, 01005 imperial (0402 metric) components are being used more and more and 03015 metric components are being introduced into new products; thus, the challenge to release solder paste from these very small openings in the stencil is becoming more difficult. Obviously, this challenge includes several aspects of the print process. The printer itself and the alignment accuracy it is capable of, solder paste powder size and flux technology used in the paste, and the stencil all influence the final solder paste deposit. In this column, I want to focus on new technologies currently used in the stencil manufacturing process.
When a customer places an order for a stencil, the first step in the manufacturing process is the design phase. PCB Gerber files are the primary data type used for stencil design. In some cases, customers will supply just the solder paste layer when ordering their stencil. What they do not realize is there is no standard for designers when creating the paste layer. Some designers create the paste layer one-to-one with the outer copper layer SMT pads and some add reductions to the paste layer based on their design criteria. If only the paste layer is submitted with the stencil order, the stencil design engineer does not know if reductions have already been applied, and in some cases, may apply additional reductions based on specific customer information. This design can result in insufficient paste and increase first-pass defects.
I always recommend the customer submits, at a minimum, the outer copper layers, solder mask layers, silkscreen layers to reference specific components, and the paste layers. This will provide the stencil design engineer with the information needed for the best possible design. The drill layers are also used many times in stencil design when open vias in ground pads need to be avoided at the print process to prevent solder thieving and decrease voiding. The ability to know if the SMT pad is mask or copper defined as well as how much the mask is oversized can influence the way the stencil apertures are designed. This information is extremely important when designing stencils to print emerging technologies.
The actual Gerber editing software used in the stencil design phase is perhaps one of the most critical inputs for stencil manufacturing. New software technologies use intrinsic apertures such as rounded rectangles and diamonds, homeplates, inverted homeplates, MELF shapes, as well as odd shapes such as flashes. They can accurately calculate the area and aspect ratios of these intrinsic apertures and report if these ratios fall under a given threshold. The ability of these new software technologies to make these calculations and report them are key when designing stencils for packages challenging the stencil printing process. This feedback allows the design engineer to determine the foil thickness needed or if a step stencil is needed based on area ratio.
In addition, new technology software packages can recognize groups of apertures (D-codes) as components. For instance, the leads around the perimeter of a quad-flat no-leads (QFN) package are typically made up of two different apertures and the center pad is a separate aperture. New stencil design technology allows the engineer to teach the perimeter leads of the QFN and the center ground pad as one unique component. Specific reductions and/or shapes can be applied to this newly taught group of apertures and saved in a library.
As subsequent stencil orders are placed, the library can be used to identify previously taught groups of apertures and apply predetermined modifications to those apertures automatically. This technology reduces human error by eliminating the need to address these components each time they are used in a stencil design. In addition, if the customer is having an issue with a specific component, the design can be updated one time in the library and all future occurrences of that design will be corrected. Over time, the libraries become mature and stencil design is more consistent from board to board. This consistency improves overall yields for the assembly customer and reduces first-pass yields.
The second most important input of the SMT stencil is the actual foil the stencil is made from. When working to overcome the challenges of miniaturization in SMT assembly, it is important to make sure the stencil supplier evaluates new foil technologies and provides the best technology to minimize first-pass defects. There are several different types of stencil foil materials offered today including fine-grain stainless steels, electroformed nickel, and standard stainless steels.
I was involved in a recent study that looked at different base materials and evaluated their effects on solder paste release or transfer efficiency. The result of the study showed a specific “fine-grain” stainless technology foil released paste better and produced less variation than the other materials tested (Figure 1). In the study, the term “fine grain” was defined as materials with a grain structure of five microns or less. The study also showed that not all fine-grain materials produce the same results, and the technology used to manufacture the actual foil can play a role in paste release, especially in emerging technology printing.
Figure 1: Best performing foil.
The second-best foil in our study of paste release was the electroformed nickel material where the apertures were also formed by the electroforming process (Figure 2). However, when we looked at coefficient of variation in the printed results, it was not in the top three performers (Figure 3). The electroforming process has a wider tolerance window than the laser cutting process affecting overall print variation. For most SMT stencil applications, the laser-cut fine-grain stencil was shown to perform the best, and is what I recommend when customers ask for the best SMT stencil available. Other materials such as laser-cut nickel sheets did not perform as well as the best performing fine-grain stainless alloy.
Figure 2: Electroformed nickel stencil aperture.
Figure 3: Worst performing foil.
Although the complete electroformed nickel stencil showed higher variation in a normal 4-mil SMT stencil application, this technology is very important as product miniaturization evolves. Customer requirements to print modules populated entirely with emerging technology components such as 0.3-mm pitch bottom termination components (BTCs) and 03015 metric or similar components require very thin stencils. For these stencil printing applications, thin foils from 1.5 to 3 mils are being used to maintain proper area ratios. For these applications, the electroforming process is key. Foil thickness can be targeted to 1/10 of a mil, and can be dialed in to maximize a specific thickness while targeting a specific area ratio. This stencil technology is also the primary method used to manufacture wafer-level bumping stencils and other applications with very high aperture counts where laser manufacturing cannot compete.
To conclude this first part of my two-part column, I’d like to stress the importance of making sure the stencil supplier is utilizing the newest Gerber editing technology available. The consistency these software packages produce will reduce first-pass defects as proven aperture libraries are developed. Also, it is extremely important that the stencil manufacturer utilizes the latest and best performing foil materials available to provide the best possible SMT stencils and minimize first-pass defects.
Greg Smith is manager of stencil technology at BlueRing Stencils. To read past columns or contact Smith, click here.
More Columns from SMT Stencils 101
SMT Stencils 101: Root-cause Stencil Design, Part 3—Tearing Down BridgesSMT Stencils 101: Root-cause Stencil Design, Part 2—Tombstones
SMT Stencils 101: Root-cause Stencil Design, Part 1—Solder Balls
SMT Stencils 101: What Are Industry-standard Stencil Designs?
Overcoming the Challenges of Miniaturization with New Stencil Technologies–Solder Paste Release, Pt. 2
A Brief History of Solder Stencil Manufacturing