-
- News
- Books
Featured Books
- smt007 Magazine
Latest Issues
Current IssueSupply Chain Strategies
A successful brand is built on strong customer relationships—anchored by a well-orchestrated supply chain at its core. This month, we look at how managing your supply chain directly influences customer perception.
What's Your Sweet Spot?
Are you in a niche that’s growing or shrinking? Is it time to reassess and refocus? We spotlight companies thriving by redefining or reinforcing their niche. What are their insights?
Moving Forward With Confidence
In this issue, we focus on sales and quoting, workforce training, new IPC leadership in the U.S. and Canada, the effects of tariffs, CFX standards, and much more—all designed to provide perspective as you move through the cloud bank of today's shifting economic market.
- Articles
- Columns
- Links
- Media kit
||| MENU - smt007 Magazine
Estimated reading time: 3 minutes
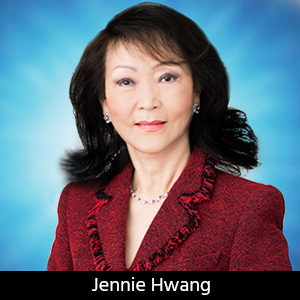
SMT Manufacturing: Why Soldering?
My last column—"Artificial Intelligence: Super-Exciting, Ultra-Competitive" (SMT007 Magazine, September 2018)—described compelling needs of the next generation of hardware in the artificial intelligence (AI) era. Upcoming AI hardware requires advanced semiconductors, packaging approaches, new architectures, increased speeds and capabilities of inference processing, and system design and manufacturing prowess continually developed to reach the interconnect density.
Against this backdrop, packaging and assembly levels—including surface-mount technology (SMT)—will continue to be critical technology and serve as the backbone of manufacturing electronic hardware to deliver desired products with enhanced miniaturization, functionality, and augmented intelligence promptly.
The SMT electronics manufacturing sector with OEMs and EMSs alike has overcome many challenges in the past. I do not doubt that we will tackle new challenges head-on to produce the required hardware in the AI era. Under the established infrastructure, will soldering (reflow, wave, selective, etc.) remain a necessary technique?
Soldering—the process to make solder joints—sounds like an ancient technique and is typically deemed unglamorous. However, substantial innovations and refinements in process and equipment have been made over the last three decades. Soldering offers an array of characteristics that bear both scientific and practical merits that will continue to maintain viability in the electronics industry. Here is my list of top five characteristics:
1. Application flexibility and agility: Solder can be readily made and applied in various physical forms, including bar, ingot, wire, powder, preform, solder sphere, solder column, paste, ink, and in a molten state.
2. Compatibility: Soft solder alloys fit into the process temperature range that electronic components—such as integrated circuits (ICs), passives, and optoelectronic devices—and the internal structure of the PCB are designed for and can withstand. Any other joining techniques (e.g., brazing, welding) need a much higher process temperature that is unsuitable for electronic components and PCBs.
3. Practicality: Solder alloys have the required environmental stability during manufacturing and in service (e.g., not prone to excessive oxidation, not corrosive, not unduly toxic).
4. Performance: A solder alloy—specifically a tin-based alloy with designed compositions—delivers the required physical properties (e.g., melting temperature, thermal and electrical conductivity, wetting ability, surface tension) and mechanical properties (e.g., strength, creep resistance, thermal fatigue resistance).
5. Cost and competitiveness: Solder alloys and soldering processes in the SMT infrastructure can be readily synchronized with intelligence-enabled manufacturing and automation, which is key to the future of electronic hardware manufacturing and producing reliable products economically.
Conclusion
Overall, the flexibility, agility, compatibility, practicality, performance, cost, and competitiveness offered by soldering are crucial to making both today’s electronic products and those anticipated in the future. This collective array of characteristics is unique. There is no better substitute in existence that delivers all of the necessary attributes previously listed.
For example, conductive adhesive and solder material have been studied in parallel when SMT was implemented for manufacturing PCB assemblies in the 1980s. Conductive adhesive worked in some selective applications but did not fill the interconnection role in a broad scope and or in mass production. This does not imply that new materials coupled with advanced techniques are not welcome. Instead, better methods, technologies, and materials should and will always be embraced by the industry.
The role of solder as the electrical, mechanical, and thermal linkage of circuitry is essential to electronic products. Soldering process know-how is closely linked with production defects, yields, and costs of electronic devices. An additional level of performance and reliability of solder joints is required mainly stemming from the confluence of three fronts: powerful chip designs, advanced IC packages, and higher density PCBs. Accordingly, SMT soldering is expected to deliver increased precision and heightened automation using solder materials that possess enhanced properties to make reliable solder interconnections for the new generation of electronic AI hardware.
More Columns from SMT Perspectives and Prospects
SMT Perspectives and Prospects: Warren Buffett’s Perpetual Wisdom, Part 2SMT Perspectives and Prospects: Warren Buffett’s Perpetual Wisdom, Part 1
SMT Perspectives and Prospects: Artificial Intelligence, Part 5: Brain, Mind, Intelligence
SMT Perspectives and Prospects: Artificial Intelligence, Part 4—Prompt Engineering
SMT Perspectives and Prospects: The AI Era, Part 3: LLMs, SLMs, and Foundation Models
SMT Perspectives and Prospects: A Dose of Wisdom
SMT Prospects and Perspectives: AI Opportunities, Challenges, and Possibilities, Part 1
SMT Perspectives and Prospects: Critical Materials—A Compelling Case, Part 3