-
- News
- Books
Featured Books
- design007 Magazine
Latest Issues
Current IssueCreating the Ideal Data Package
Why is it so difficult to create the ideal data package? Many of these simple errors can be alleviated by paying attention to detail—and knowing what issues to look out for. So, this month, our experts weigh in on the best practices for creating the ideal design data package for your design.
Designing Through the Noise
Our experts discuss the constantly evolving world of RF design, including the many tradeoffs, material considerations, and design tips and techniques that designers and design engineers need to know to succeed in this high-frequency realm.
Learning to Speak ‘Fab’
Our expert contributors clear up many of the miscommunication problems between PCB designers and their fab and assembly stakeholders. As you will see, a little extra planning early in the design cycle can go a long way toward maintaining open lines of communication with the fab and assembly folks.
- Articles
- Columns
Search Console
- Links
- Media kit
||| MENU - design007 Magazine
Estimated reading time: 2 minutes
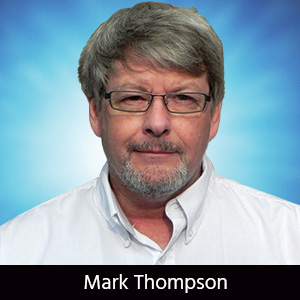
The Bare (Board) Truth: Getting on the Same Page—A Data Story
In this month’s column, I will discuss what makes a great incoming dataset for PCB fabrication.
Drawings and README Files
The overall part thickness should be expressed as the desired thickness measured between two points, including tolerances. For example:
- 0.062” ±10% metal-to-metal including surface finish
This description tells us the part will be 0.062” nominal with an allowed variance of ±10% measured over the finished plated metal and surface finish. If the drawing or README file merely states 0.062”, the fabricator must establish whether or not this is a maximum thickness or if a tolerance is associated with it. The note also says nothing about what distance 0.062” refers to. Is it 0.062” glass-to-glass over the material, or is it metal-to-metal? Does this include plate-up and surface finish, or is it an overall dielectric with a tolerance, such as ±10%?
Thickness callouts for single-sided or double-sided orders are even more critical. As a fabricator, we can control the thickness of the multilayer by using different combinations of prepregs/cores. If a customer calls out a single-sided or double-sided job as 0.008”, is this the core dielectric or an overall dielectric? If 0.008” represents the core dielectric callout on a 2-ounce finished part, the final thickness would be closer to 0.013”. If the callout for 0.008” pertains to the overall finished thickness, we would need to start at a 0.004” core to finish at approximately 0.009” after plate, surface finish, and mask. Again, notes about thickness should ideally describe what the overall thickness is to be and the points from which they should be measured.
Another example of drawing callouts that can require clarification is copper callouts. If the drawing or README file expresses the copper merely as 2-ounce copper, this leaves the fabricator with more questions. Is it a starting or finished copper callout? If the part is a multilayer board, is it 2-ounce inners and 2-ounce finished outers? If that’s the case, a fabricator will start on 1-ounce copper clad outers and plate to a 1-ounce finish. IPC dictates that there be a minimum of 0.0008” copper in the barrels of the holes for conductivity concerns. Fabricators typically plate up in whole ounce increments to ensure this minimum requirement is met, so a part that started on half-ounce copper foil would finish at 1.5 ounces after plate.
If a note merely reads 1-ounce finish, the fabricator must call the customer to clarify their intentions because starting on 0.05-ounce foil and plating to 1 ounce does not meet IPC minimum requirements for hole wall thickness.
To read this entire column, which appeared in the October 2018 issue of Design007 Magazine, click here.
Visit I-007eBooks to download your copies of Prototron Circuits' micro eBook today:
The Printed Circuit Designer's Guide to...Producing the Perfect Data Package
More Columns from The Bare (Board) Truth
The Bare (Board) Truth: My Top Six Design ChallengesThe Bare (Board) Truth: Via Basics
The Bare (Board) Truth: 5 Questions About Improving Thermal Management
The Bare (Board) Truth: Teaching the Next Generation—An Overview of Today’s University Courses
The Bare (Board) Truth: Fabrication Starts With Solid Design Practices
Board Negotiations: Design Rules and Tolerances
The Bare (Board) Truth: Eliminate Confusion
The Bare (Board) Truth: Refining Output Data Packages for Fabricators