-
- News
- Books
Featured Books
- smt007 Magazine
Latest Issues
Current IssueSupply Chain Strategies
A successful brand is built on strong customer relationships—anchored by a well-orchestrated supply chain at its core. This month, we look at how managing your supply chain directly influences customer perception.
What's Your Sweet Spot?
Are you in a niche that’s growing or shrinking? Is it time to reassess and refocus? We spotlight companies thriving by redefining or reinforcing their niche. What are their insights?
Moving Forward With Confidence
In this issue, we focus on sales and quoting, workforce training, new IPC leadership in the U.S. and Canada, the effects of tariffs, CFX standards, and much more—all designed to provide perspective as you move through the cloud bank of today's shifting economic market.
- Articles
- Columns
- Links
- Media kit
||| MENU - smt007 Magazine
What is ESD and Why Should We Worry About It?
December 10, 2018 | Pete Starkey, I-Connect007Estimated reading time: 8 minutes
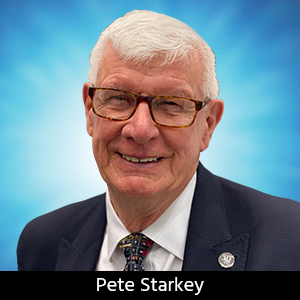
Stroke the cat or walk on the carpet on a dry day in winter, then touch the door handle. Ouch! If electrostatic discharge (ESD) can make us jump, imagine the effect it could have on microelectronics. The realities of ESD, how static charges are generated, how they can be transferred to electronic components and the damage they can do, and what practical controls are required to protect components, assemblies and equipment from damage—these topics were explored and clearly explained in a webinar on beginners' guide to ESD, presented by SMTA Europe Technical Committee members Dr. Jeremy Smallwood of Electrostatic Solutions and Charles Cawthorne of MBDA.
Why worry about ESD? Dr. Smallwood began by describing how static electricity resulted from the transfer of electrons as one material came into frictional contact with another, and could build up a charge at high voltage. Using the analogy of snow resting on a mountain top before crashing down as an avalanche, he explained how charge moving quickly from place to place resulted in a high electrical current that could do a lot of damage very quickly! He commented that although a person would not feel an ESD shock until the voltage was of the order of 4000, some components could be damaged at voltages less than 100.
He showed photographs of ESD damage to conductors in integrated circuits, remarking that there was no easy way of telling that damage had occurred, that expensive analysis was required to identify it, and that in the worst case assemblies with ESD-damaged components could pass test then fail later in the field, costing not just money, repair time and delays, but resulting in loss of confidence in the reliability of the product. "Assume that the assembly is as ESD sensitive as its most sensitive component!" And the main source of ESD damage was people!
Examining in more detail the origin of the static charge, Dr. Smallwood explained that every material was naturally composed of electrostatic charges: negative electrons and positive atomic nuclei. When those charges were present in equal numbers, their electrostatic effects cancelled out. When two materials touched, charge moved between them, and when the materials were separated, they took their new charge with them; one positive and the other equally negative. And the charges would try to move to return to balance if they were not stopped from doing so.
Explaining why there was not always a build‐up of static charge, Dr. Smallwood used the analogy of a water tap running into a sink. If the plug hole was open, the water could escape faster than it was coming in. But if the plug was in, or the drain was partially blocked, the water level would continue to rise. And a sink with the plug in was the equivalent of a charged insulator. Electrical insulators prevented charge from moving away and encouraged the build‐up of static charge, resulting in high voltages, high electrostatic fields and the risk of ESD.
Obviously the ideal situation would be to keep insulators away from ESD-sensitive devices (ESDS), but because some insulators were an essential part of the product or build process, appropriate precautions were needed to minimise the ESD risk. He explained that conductors, effectively anything that was not an insulator, including people, allowed charge to move around quickly enough to avoid charge build-up, but could be a strong source of ESD unless they were grounded to provide an electrically conducting path for the charge to move to earth.
So how to prevent ESD damage? Dr Smallwood’s guidelines provided a basic code of good practice in awareness of ESD threats, recognition of ESDS devices, correct ESD procedures and where to get help on ESD control. He began by describing what was meant by an ESD Protected Area (EPA), within which ESDs components could be safely handled. “Never take an ESDS out of its protective packaging unless you are in an EPA!”
An EPA was an area in which static electricity was controlled to a low level. It was essential that it had a clearly defined boundary, and that equipment and processes used within the EPA had been designed to prevent ESD damage. He described how static electricity was controlled by ensuring that all people handling ESDS were grounded with wrist straps or footwear and flooring, by grounding all conductors, by avoiding unnecessary insulators or static-generating materials, and by using only ESD packaging. It was necessary to check and test wrist straps and footwear before starting work, and especially to wear a wrist strap whilst seated—even on an EPA-rated chair on an EPA conductive floor—when handling ESDS components.
EPA bench surfaces were made of conductive or static-dissipative material and grounded. It was normal for them to have a high resistance so that any charge was taken away gently, rather than suddenly, from any conducting item placed on them such as tools, tote boxes and other packaging. If ESD coats were worn to prevent electrostatic fields from charged clothing reaching ESDS, it was essential that they were fastened correctly and made good contact with the body, usually at the wrist. And of course it was also essential that any visitor to the EPA should comply with ESD prevention measures.
Dr. Smallwood described the various forms and functions of ESD packaging: those which protected against electrostatic fields, those which protected against direct electrostatic discharge, and those which did not charge up much, adding that some could exhibit combinations of these properties. For example, pink polythene bags did not give ESD protection to ESDS, although they helped reduce charge build‐up. Black polythene bags shielded against electrostatic fields, but not ESD. Metallised shielding bags gave protection against direct ESD.
If an ESDS was required to go outside the EPA, then it should be in ESD-shielding packaging, or as defined by a company’s ESD control programme, or as agreed with the company’s supplier or customer. Only ESD-protective packaging materials should be allowed in an EPA—ordinary packaging should be kept out of the area. And when ESDS devices were received at Goods Inwards, the packages should be unwrapped as far as the ESD-protective packaging, and no further until they were in an ESD-protected area.
And then to the practical bit! Having defined the terminology and outlined the basics of ESD good practice, Dr Smallwood handed over to Charles Cawthorne, Circuit Card Assembly Technologist with MBDA Missile Systems, to describe some of the ESD control procedures adopted by a manufacturer of high-reliability milaero electronics.
Cawthorne began by describing the basics of setting-up an EPA, with the primary objective of controlling static voltages to below 100V, commenting that some industries had local procedures that specified tighter limits. The fundamental requirements were to ensure the grounding of personnel and to provide special bench surfaces and flooring where appropriate. The boundaries of the EPA needed to be clearly defined and marked, with clear signage. In MBDA, ESD-protective coats were preferred, although not mandatory, and special ESD-safe chairs were provided. There were specific procedures for the management of equipment, processes and items that presented a risk of charge generation.
With photographs, he illustrated the features of a typical small-scale EPA: a grounded work-bench with a dissipative surface, standing on a dissipative floor-mat, the boundaries of which were clearly marked with yellow “ESD Protected Area” tape. The primary means of grounding the operator was by wrist-strap; heel-grounders were also provided, although some operators wore ESD shoes. Wrist straps and ESD shoes or heel-grounders were required to be tested and the results recorded at the beginning of each shift or before first entering the EPA. MBDA had strict procedures for quarterly testing of ground to earth-bonding points, work surfaces point-to-point and to EPA ground, ESD flooring to EPA ground or ESD floor mat to earth-bonding point, and ESD chairs to EPA ground. BS EN 61340-5-1 was the reference standard, and work-benches were labelled to signify correct functionality. Cawthorne commented that an EPA could be any size from a single work-station to an entire assembly shop.
Training was a fundamental part of ESD control, and training plans were mandated by BS EN 61340-5-1. Everyone entering an EPA was required to abide by ESD disciplines, and training was carried out for all personnel, irrespective of level or seniority—in MBDA there was even a training plan for cleaners entering EPAs. And it was essential that training records were maintained—they were typically the first thing that auditors asked to see!
Cawthorne gave some examples of ESD pitfalls, often a consequence of poor housekeeping. Clear plastic packaging and bubble wrap were definitely materials to be kept out of the EPA. ESD-safe chairs were not designed to be used as a primary means of grounding personnel, and it was recommended always to use a wrist-strap when seated. Conventional adhesive tapes would build-up a charge as they were withdrawn from the reel, although ESD-safe tapes and tape dispensers were available.
Regarding the packaging, transportation and storage of electrostatic sensitive equipment, Cawthorne described four types of ESD packaging as already mentioned by Dr Smallwood, and the labelling associated with each type: Shielded packaging, designated “S”, was the preferred primary means for the containment of any electronic components or assembly, and should completely enclose the items to be effective. Lower-cost dissipative packaging, designated “D” could be used for non-electronic components within an EPA. Dedicated conductive boxes, designated “C”, containing circuit cards separated by conductive foam, were useful as a means of combining ESD protection with robust material handling. Low-charging packaging like the familiar pink polythene bags, designated “L” were only useful for documentation. ESD compliant trolleys could be used to transport assemblies within an EPA.
The webinar was rounded-off with a lively Q&A session, moderated by Bob Willis. Topics included discussion of practical limitations on re-use of shielded packaging, and certification programmes based on industry standards BS EN 61340-5-1, IEC 61340-5-1 and ANSI/ESD S20.20-2014.
Dr. Smallwood summed it all up with the assertion that ESD control should be viewed as an investment with a good ROI, and not a cost. And he implored companies not to waste money by making unsound economies in their ESD investments.
I thank Jeremy and Charlie for a most informative webinar. Although some SMT professionals might dismiss it as "ESD for tiny tots," it certainly clarified a lot of points for me personally and I am sure that many of our readers will benefit from the clearly-presented information and knowledge they were happy to share. Thanks to SMTA Europe for providing the vehicle, and to Bob Willis for his first-rate management of the event.
Editor's Note: Feature photo courtesy of Rockwell Automation.
Testimonial
"The I-Connect007 team is outstanding—kind, responsive, and a true marketing partner. Their design team created fresh, eye-catching ads, and their editorial support polished our content to let our brand shine. Thank you all! "
Sweeney Ng - CEE PCBSuggested Items
KYZEN Cleaning Experts to Provide Insights at SMTA High Reliability Cleaning and Coating Conference
07/29/2025 | KYZEN'KYZEN, the global leader in innovative environmentally responsible cleaning chemistries, announced today that three members of the KYZEN team of cleaning experts will present technical presentations as part of KYZEN’s participation at the 2025 SMTA High Reliability Cleaning and Conformal Coating Conference scheduled to take place Aug. 12-14, 2025 at the Westin DFW Airport.
HyRel’s Brian Watson Named Candidate for SMTA Board of Directors
07/25/2025 | HyRelHyRel Technologies, a global provider of quick turn semiconductor modification solutions, is proud to announce that its Founder, Brian Watson, has been named a 2025 candidate for the SMTA Board of Directors.
Weller Tools Supports Future Talent with Exclusive Donation to SMTA Michigan Student Soldering Competition
07/23/2025 | Weller ToolsWeller Tools, the industry leader in hand soldering solutions, is proud to announce its support of the upcoming SMTA Michigan Expo & Tech Forum by donating a limited-edition 80th Anniversary Black Soldering Set to the event’s student soldering competition.
SMTA International Technical Conference Program Announced
07/22/2025 | SMTAThe SMTA announced that the technical program of their annual conference, SMTA International, is finalized and registration is now open. The event will be held October 19 - 23, 2025 at the Donald E. Stephens Convention Center in Rosemont, IL, USA.
INSPECTIS AB ‘Makes it a Meal’ with Series U50s Advanced Kit
07/18/2025 | INSPECTIS ABFamous chefs the world over maintain that an entrée doesn’t make a great meal without side dishes. At INSPECTIS, we call those ‘sides’ an Advanced Kit.