-
- News
- Books
Featured Books
- smt007 Magazine
Latest Issues
Current IssueWhat's Your Sweet Spot?
Are you in a niche that’s growing or shrinking? Is it time to reassess and refocus? We spotlight companies thriving by redefining or reinforcing their niche. What are their insights?
Moving Forward With Confidence
In this issue, we focus on sales and quoting, workforce training, new IPC leadership in the U.S. and Canada, the effects of tariffs, CFX standards, and much more—all designed to provide perspective as you move through the cloud bank of today's shifting economic market.
Intelligent Test and Inspection
Are you ready to explore the cutting-edge advancements shaping the electronics manufacturing industry? The May 2025 issue of SMT007 Magazine is packed with insights, innovations, and expert perspectives that you won’t want to miss.
- Articles
- Columns
- Links
- Media kit
||| MENU - smt007 Magazine
More Than Inspection: It’s Process Improvement
January 9, 2019 | Barry Matties, I-Connect007Estimated reading time: 10 minutes
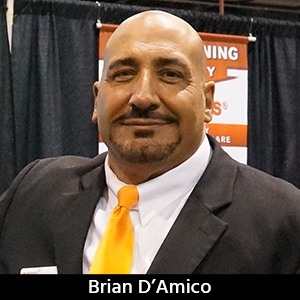
Barry Matties speaks with Brian D’Amico, president of MIRTEC, about the current state of machine-to-machine communication in the industry, and how the inspection company is interfacing with the different manufacturing languages currently available to gather predictive data and feedback from every inspection step to eliminate future defects.
Barry Matties: First, can you tell our readers a little bit about MIRTEC?
Brian D’Amico: Certainly, Barry. MIRTEC is a leading global supplier of inspection equipment to the electronics manufacturing industry. Our company is basically comprised of three separate divisions serving the SMT, LED, and semiconductor industries. We also own a camera division—ISVI Corporation—which manufactures cameras for all of the various systems across these divisions.
Matties: Let’s start with SPI. In the SPI realm, what challenges or trends do you see from your customers?
D’Amico: In terms of the SPI machine, there is a trend toward closed-loop feedback. In other words, the SPI system must be capable of communicating upstream with the screen printer/dispenser as well as downstream with the pick-and-place machine. The goal is to provide actionable data to the screen printer and pick-and-place systems that may be used to reduce defects and maximize efficiency. Industry 4.0 is a topic of much discussion within the electronics manufacturing industry. Manufacturers and vendors are trying to come to terms with what that means. In the most simplistic of terms, Industry 4.0 is a trend toward automation and data exchange within the manufacturing process. This requires connectivity and communication from machine to machine within the manufacturing line. The challenge is to collect data from each of the systems within the line and make that data available to the rest of the machines.
Matties: When you mentioned communicating, are machines upstream and downstream making adjustments and fine tuning to that particular panel?
D’Amico: Yes; however, these adjustments are typically based on trends within the inspection data. For example, let’s say that the SPI machine detects an offset trend in solder depositions with regard to pad location. Under these circumstances, the SPI machine would report the trend to the screen printer. The screen printer, in turn, may then use this data to adjust the location of the stencil to the pads to eliminate the offset. Please keep in mind that the goal is not to control the screen printer, but to provide actionable data that may be used to eliminate the offset trend and potential defects.
Matties: Does the machine do this without human intervention?
D’Amico: Yes and no; it’s really up to each vendor to determine whether adjustments are to be made manually or autonomously. Most vendors will provide a means of selecting between manual and automatic mode.
Matties: This is a big deal in yield performance.
D’Amico: Agreed.
Matties: Is there a proprietary or a universal language that people can tap into their data models?
D’Amico: That is a very good question. There's a trend towards standardization right now. Keep in mind that there are two basic requirements for machine-to-machine communication. The first is connectivity, and the second is data sharing from machine to machine. The goal is to format the available process data from each respective machine in a manner which is usable by other machines within the line.
If we take this one step further, the ultimate goal is to analyze big data. This is where we want to use artificial intelligence (AI) to help determine where the manufacturing process broke down and make recommended corrective actions. That's a while off yet; it requires a lot of data and AI to sort through it and come up with predictions.
Matties: If we can predict it, then the machines can adjust on the fly, which eliminates the need for personnel in line.
D’Amico: That's the key. There's no way to beat a human being right now because humans can evaluate all of the various process information a lot better than a machine can at this time. The goal of any AI engine is to try to approximate the decision-making capability of a good process engineer, but I think that's quite a bit off. It’s going to require a lot of data and processing power to get there, but that's the holy grail—to have the machines communicate with each other and come up with predictive data that eliminates defects at each stage of the manufacturing process.
Matties: How many of your customers or prospects are demanding this, or is this a requirement for doing business with them?
D’Amico: With the movement toward Industry 4.0, I find that a lot of people are asking the same question, “Are these machines Industry 4.0 capable?” I understand the reason for this concern. When a manufacturer invests in a new piece of assembly equipment, they expect to use the equipment for a period of five to 10 years or more. So, it stands to reason that any new piece of assembly equipment must provide the required process data as well as the ability to communicate with other machines within the line. These are the basic requirements for Industry 4.0 capability.
Matties: You started by saying there's this movement toward Industry 4.0, but what does that really mean? How do customers define that or distill it down to something that's meaningful? Do they come with you and say, "We already have this language in our shop, and we want you to adhere to that?"
D’Amico: It’s important to keep in mind that Industry 4.0 is still evolving. Thus, it’s not a matter of somebody saying, "This is what I have now, and you have to adhere to it;" it's more like, "Can you tell me what this is all about?" The bottom line is that all of us are still in the midst of defining Industry 4.0 and how it pertains to the electronics manufacturing industry.
Page 1 of 2
Suggested Items
Driving Innovation: Direct Imaging vs. Conventional Exposure
07/01/2025 | Simon Khesin -- Column: Driving InnovationMy first camera used Kodak film. I even experimented with developing photos in the bathroom, though I usually dropped the film off at a Kodak center and received the prints two weeks later, only to discover that some images were out of focus or poorly framed. Today, every smartphone contains a high-quality camera capable of producing stunning images instantly.
Hands-On Demos Now Available for Apollo Seiko’s EF and AF Selective Soldering Lines
06/30/2025 | Apollo SeikoApollo Seiko, a leading innovator in soldering technology, is excited to spotlight its expanded lineup of EF and AF Series Selective Soldering Systems, now available for live demonstrations in its newly dedicated demo room.
Indium Corporation Expert to Present on Automotive and Industrial Solder Bonding Solutions at Global Electronics Association Workshop
06/26/2025 | IndiumIndium Corporation Principal Engineer, Advanced Materials, Andy Mackie, Ph.D., MSc, will deliver a technical presentation on innovative solder bonding solutions for automotive and industrial applications at the Global Electronics A
Fresh PCB Concepts: Assembly Challenges with Micro Components and Standard Solder Mask Practices
06/26/2025 | Team NCAB -- Column: Fresh PCB ConceptsMicro components have redefined what is possible in PCB design. With package sizes like 01005 and 0201 becoming more common in high-density layouts, designers are now expected to pack more performance into smaller spaces than ever before. While these advancements support miniaturization and functionality, they introduce new assembly challenges, particularly with traditional solder mask and legend application processes.
Knocking Down the Bone Pile: Tin Whisker Mitigation in Aerospace Applications, Part 3
06/25/2025 | Nash Bell -- Column: Knocking Down the Bone PileTin whiskers are slender, hair-like metallic growths that can develop on the surface of tin-plated electronic components. Typically measuring a few micrometers in diameter and growing several millimeters in length, they form through an electrochemical process influenced by environmental factors such as temperature variations, mechanical or compressive stress, and the aging of solder alloys.