ESI’s Chris Ryder: There’s More to Choosing a Laser Than You Think
January 16, 2019 | Barry Matties, I-Connect007Estimated reading time: 11 minutes
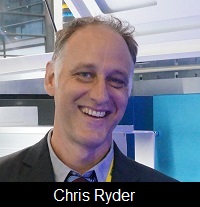
At the recent HKPCA show, I sat down with ESI’s Chris Ryder, director of product management—HDI—to discuss considerations for choosing a new laser system, and how ESI uses its decades of flex and rigid-flex drilling experience to help guide customers in their decision-making process. We also discussed ESI’s newest, granite-less, Geode CO2 laser drilling system for the rigid HDI PCB manufacturing market.
Barry Matties: First, can you talk a little bit about your role at ESI and what ESI offers?
Chris Ryder: My role at ESI is to develop our HDI platform. ESI is a big player in the flex and rigid-flex market with our UV products. Several years ago, we started some product development on the rigid board manufacturing side of things. My job is to support continuous development into the HDI, substrate-like PCB and ICP space.
Matties: HDI is obviously an area that is growing. We're seeing HDI in more and more places. I think I was at a conference not long ago where Lee Ritchey, an iconic designer and instructor, said, "If you're not doing HDI now, you're about to be."
Ryder: That's a fair statement. It’s one of the reasons why the market is so attractive to us. Having come from HDI manufacturing myself, I've watched the market mature over the past decade and a half, and I've seen the HDI process demonstrate its merits—commercial and technological, as well as applications outside of just the handset market. This is where the technology got its initial foothold. Watching HDI develop into the automotive and industrial applications market, as well as being an element of the packaging market, has been a very interesting process.
And you're absolutely right, it's becoming very commonplace now, which is clearly reflected in the upshot of companies we're seeing across Asia and other markets. These are companies that start and upgrade to HDI; the base is rapidly growing.
Matties: When we look at HDI, there's a lot of conversation. You have a lot of experience, so what's your take on if HDI costs more or less generally speaking?
Ryder: Ultimately, you have to understand what the most important focus of your product is. Is it performance, size, cost? What is going to sell your product? For example, it’s relatively straightforward and obvious why miniaturization that you get from HDI would be a clear winner in a smartphone. When you look at other areas of application, it's not always as obvious. Especially when you talk about PC or automotive electronics, sometimes they have space for a PCB that doesn't have that dense of a fan-out or via structure.
But then when you look at material and real estate costs, as well as the utilization in panel manufacturing, these numbers start to change. Again, it depends on the overall product scope that you have. How much HDI do you have in your stack-up? Do you have a 1-n-1 or a 3-n-3? How much advantage can you take of that real estate reduction?
The major new drivers right now are areas like IoT and automotive. You have high-frequency applications calling for very specialized chipsets that fundamentally need to be fanned out through HDI-type structures. To some degree, your limitation is coming from the chipset or applications manufacturers. In essence, you're being forced into HDI design rules. Maybe that's what Lee Ritchey means when he talks about, "If you're not doing it now, you will be very soon.”
Matties: When we look at the definition of HDI, there are some evolving definitions.
Ryder: That’s true. It's an intriguing dynamic. Having been in the HDI industry for a while, it used to be just synonymous with laser vias. In the meantime, even in our own company at ESI, when I talk with management, customers, and suppliers, we try to reach an understanding of the product differentiation in that market. You end up having to apply different terminology such as HDI, SLP, ICP, or FCCSP, etc. to distinguish the design rules and materials necessary for those products.
With those distinctions come a host of other things that apply to us in the laser drilling industry such as via size, via quality, accuracy demands, and automation demands. It’s interesting to follow and see how the nomenclature has developed into these submarkets. It helps us to orient ourselves as to where our systems are being used, but like anything, it's a constant motion.
Matties: And the rate of change is accelerating.
Ryder: The rate of change accelerates with the rate of acceptance of HDI or the laser via as a nominal construct for an interconnect.
Matties: As a circuit board fabricator looking at HDI as a new market space, there's an investment of technology that they'd need to make—laser drill being one of those. What advice do you have for those people?
Ryder: The best advice I could give is to understand precisely what you want. I know that sounds trivial, but what you want comes down to what is ultimately going to earn you money. Is it going to be speed, yield, a diversity of materials, or a focus on one specific product type? Coming in from the laser drilling perspective, one of the things that we try to do is guide customers in that decision-making process. There are many different lasers and ways to guide and steer that beam. Further, many different platforms mechanically manipulate the product that you're cutting and drilling, so there are many options to explore.
Talking with your supplier about the options that you have is going to help optimize your return. Is it going to be yield focused? Yield focus might not be the primary driver for a prototype shop, for example. Meanwhile, relevancy might be more determined by the diversity of base materials that you're seeing. An HVM manufacturer clearly is going to focus on the highest amount of throughput they can get and the highest degree of automation. Again, understanding what you want and what's going to make you money will help us facilitate that need.
Page 1 of 2
Suggested Items
Copper Price Surge Raises Alarms for Electronics
07/15/2025 | Global Electronics Association Advocacy and Government Relations TeamThe copper market is experiencing major turbulence in the wake of U.S. President Donald Trump’s announcement of a 50% tariff on imported copper effective Aug. 1. Recent news reports, including from the New York Times, sent U.S. copper futures soaring to record highs, climbing nearly 13% in a single day as manufacturers braced for supply shocks and surging costs.
I-Connect007 Editor’s Choice: Five Must-Reads for the Week
07/11/2025 | Andy Shaughnessy, Design007 MagazineThis week, we have quite a variety of news items and articles for you. News continues to stream out of Washington, D.C., with tariffs rearing their controversial head again. Because these tariffs are targeted at overseas copper manufacturers, this news has a direct effect on our industry.I-Connect007 Editor’s Choice: Five Must-Reads for the Week
Digital Twin Concept in Copper Electroplating Process Performance
07/11/2025 | Aga Franczak, Robrecht Belis, Elsyca N.V.PCB manufacturing involves transforming a design into a physical board while meeting specific requirements. Understanding these design specifications is crucial, as they directly impact the PCB's fabrication process, performance, and yield rate. One key design specification is copper thieving—the addition of “dummy” pads across the surface that are plated along with the features designed on the outer layers. The purpose of the process is to provide a uniform distribution of copper across the outer layers to make the plating current density and plating in the holes more uniform.
Trump Copper Tariffs Spark Concern
07/10/2025 | I-Connect007 Editorial TeamPresident Donald Trump stated on July 8 that he plans to impose a 50% tariff on copper imports, sparking concern in a global industry whose output is critical to electric vehicles, military hardware, semiconductors, and a wide range of consumer goods. According to Yahoo Finance, copper futures climbed over 2% following tariff confirmation.
Happy’s Tech Talk #40: Factors in PTH Reliability—Hole Voids
07/09/2025 | Happy Holden -- Column: Happy’s Tech TalkWhen we consider via reliability, the major contributing factors are typically processing deviations. These can be subtle and not always visible. One particularly insightful column was by Mike Carano, “Causes of Plating Voids, Pre-electroless Copper,” where he outlined some of the possible causes of hole defects for both plated through-hole (PTH) and blind vias.