Atotech at HKPCA on Announcements and Advancements
January 21, 2019 | Edy Yu, I-Connect007Estimated reading time: 4 minutes
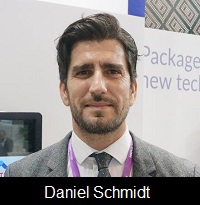
Edy Yu, managing editor for PCB007 China, caught up with Daniel Schmidt, Atotech’s director of global marketing, during the 2018 HKPCA and IPC Show in December. Edy and Daniel discussed Atotech’s new announcements at the show including their new solutions for 5G, high-speed, and high-frequency applications, and more.
Edy Yu: Atotech hosted a technical conference here at HKPCA on new products with a focus on 5G high-frequency applications. Can you tell us about the conference?
Daniel Schmidt: As every year we bring together the industry during our technical conference that is typically organized during HKPCA show in Shenzhen. One of the highlight topics was on 5G and its impact on PCB manufacturing. Today, technological progress is happening at an unprecedented speed. To comply with new requirements for more demanding PCBs, package substrates, and interconnect technologies, we have launched a series of new products during the conference that were specifically developed for 5G.
Let me give you some examples. BondFilm EX is Atotech's new solution for bonding enhancement providing low signal loss for high-frequency PCB applications. This new product can fit into existing horizontal or vertical lines, and is fully compatible with a wide range of substrates (e.g., Megtron 6, Megtron 7, TU 933, DS-7409D, etc.) and delivers a much better signal integrity compared to standard oxide replacement solutions.
Another product highlight for 5G is our new electroless copper bath called Printoganth P2. This product provides our customers with excellent throwing power, outstanding adhesion, non-blistering, and highest reliability performance even on challenging substrates such as polyimide and BT resin. We developed a drop-in solution for existing copper-plating infrastructure.
I’d also like to mention Cuprapulse IN, our new conformal copper pulse plating process for use in an insoluble anode system in hoist or VCP equipment. This process gives excellent throwing power in high aspect ratio through holes and excellent surface appearance; for example, there are no signs of a two-tone effect over a wide working range. Customers can reach an increased uniformity, process higher yield, and rely on excellent physical properties.
Last but not least, let me highlight PallaBond—Atotech's novel and new high-end finish that deposits direct palladium on copper as a universal finish. This new finish was developed to comply with finer lines and spaces (below 15 µm) and cope with high-frequency applications. It’s also lead-, nickel-, and thiourea-free.
Yu: Atotech is cooperating with GreenSource Fabrication, a U.S.-based quick-turn PCB shop, which gave the PCB world an example of future factories. Is this also a growth path for Chinese PCB fabricators?
Schmidt: Smart manufacturing, including automation and optimal waste management, have become more and more important within our industry, especially here in China. Our achievement in the U.S. at GreenSource is a great example of what is possible already today. At this moment, we are working on solutions to bring the latest achievements to China where environmental regulations continue to become stricter, and the need to manage waste, use of water, raw materials, and energy must be more efficient. How can Chinese fabricators adapt these available solutions? Our recommendation is to contact us and engage early on when planning a new production plant, so we can be a strategic partner and suggest the latest systems solutions to meet future requirements.
Yu: How can Atotech support Chinese PCB manufacturers who are entering the high-frequency and high-speed PCB segment?
Schmidt: I appreciate this question. There is no doubt 5G is on its way, and it’s all about high-frequency applications. There are still quite a few challenges and impacts on 5G implementation versus the current technology available. First, you need enhanced adhesion promotion to reduce signal loss to fulfill signal integrity requirements. Then, you need an optimized electroless copper for high-speed signal transmission followed by a higher plating uniformity impacting warpage. Finally, your reliability and thermal heat dissipation need to improve by an advanced through hole and copper filling.
Today, Atotech is already very active in working with customers and developing new processes to meet the very stringent requirements for high-frequency applications. How can we support domestic PCB manufacturers? We assist with consultancy on challenges and requirements for 5G high-frequency and high-speed PCBs, and offer our new process chemicals and systems solution and guide Chinese manufacturers to fully utilize the new market opportunities that come with 5G networks and servers.
Yu: In the future, what will be your next focus?
Schmidt: This year has been very productive with the overall PCB market expected to grow for the second year in a row. The growth has been driven primarily by multilayer PCBs and package substrates, while 2017 was driven by HDI and flex PCBs. For next year, 2019, several market researchers expect the market to soften slightly. Some segments will grow regardless, for instance, 5G infrastructure (base stations, access points, servers and data storage), automotive, mobile devices, wearables, and medical applications. However, we can only fully participate in this growth if we provide the most advanced technical solutions, which we do through a combination of innovative chemistry and world-class equipment. Our focus lies on solutions for the next-generation HDI (mobile devices), flex and rigid-flex PCBs (automotive and mobile devices), package substrate (computer and server) and advanced packaging (automotive and mobile devices).
Yu: Congratulations on the technical conference, and thank you for your time.
Schmidt: Thank you!
Testimonial
"In a year when every marketing dollar mattered, I chose to keep I-Connect007 in our 2025 plan. Their commitment to high-quality, insightful content aligns with Koh Young’s values and helps readers navigate a changing industry. "
Brent Fischthal - Koh YoungSuggested Items
How Good Design Enables Sustainable PCBs
08/21/2025 | Gerry Partida, Summit InterconnectSustainability has become a key focus for PCB companies seeking to reduce waste, conserve energy, and optimize resources. While many discussions on sustainability center around materials or energy-efficient processes, PCB design is an often overlooked factor that lies at the heart of manufacturing. Good design practices, especially those based on established IPC standards, play a central role in enabling sustainable PCB production. By ensuring designs are manufacturable and reliable, engineers can significantly reduce the environmental impact of their products.
50% Copper Tariffs, 100% Chip Uncertainty, and a Truce
08/19/2025 | Andy Shaughnessy, I-Connect007If you’re like me, tariffs were not on your radar screen until a few months ago, but now political rhetoric has turned to presidential action. Tariffs are front-page news with major developments coming directly from the Oval Office. These are not typical times. President Donald Trump campaigned on tariff reform, and he’s now busy revamping America’s tariff policy.
Global PCB Connections: Understanding the General Fabrication Process—A Designer’s Hidden Advantage
08/14/2025 | Markus Voeltz -- Column: Global PCB ConnectionsDesigners don’t need to become fabricators, but understanding the basics of PCB fabrication can save you time, money, and frustration. The more you understand what’s happening on the shop floor, the better you’ll be able to prevent downstream issues. As you move into more advanced designs like HDI, flex circuits, stacked vias, and embedded components, this foundational knowledge becomes even more critical. Remember: the fabricator is your partner.
MKS’ Atotech to Participate in IPCA Electronics Expo 2025
08/11/2025 | AtotechMKS Inc., a global provider of enabling technologies that transform our world, announced that its strategic brands ESI® (laser systems) and Atotech® (process chemicals, equipment, software, and services) will showcase their latest range of leading manufacturing solutions for printed circuit board (PCB) and package substrate manufacturing at the upcoming 17th IPCA Show to be held at Pragati Maidan, New Delhi from August 21-23, 2025.
MKS Showcases Next-generation PCB Manufacturing Solutions at the Thailand Electronics Circuit Asia 2025
08/06/2025 | MKS Instruments, Inc.MKS Inc, a global provider of enabling technologies that transform our world, today announced its participation in Thailand Electronics Circuit Asia 2025 (THECA 2025), taking place August 20–22 at BITEC in Bangkok.