-
- News
- Books
Featured Books
- pcb007 Magazine
Latest Issues
Current IssueInventing the Future with SEL
Two years after launching its state-of-the-art PCB facility, SEL shares lessons in vision, execution, and innovation, plus insights from industry icons and technology leaders shaping the future of PCB fabrication.
Sales: From Pitch to PO
From the first cold call to finally receiving that first purchase order, the July PCB007 Magazine breaks down some critical parts of the sales stack. To up your sales game, read on!
The Hole Truth: Via Integrity in an HDI World
From the drilled hole to registration across multiple sequential lamination cycles, to the quality of your copper plating, via reliability in an HDI world is becoming an ever-greater challenge. This month we look at “The Hole Truth,” from creating the “perfect” via to how you can assure via quality and reliability, the first time, every time.
- Articles
- Columns
- Links
- Media kit
||| MENU - pcb007 Magazine
Estimated reading time: 4 minutes
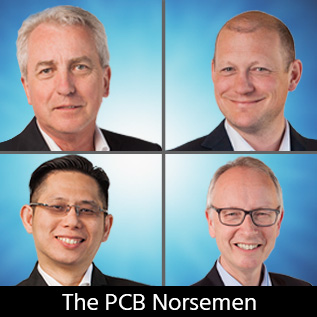
The PCB Norsemen: PCB Standards for Medical Device Applications—A Hard Nut to Crack!
Medical applications must be made by the book with strict standards and can vary in size and technology—from large advanced Xray machines to robotic arms and microscopic hearing devices or sensors. Applications can also be made for both the exterior and interior of the human body. When you think of the variety of environments medical devices must tolerate, it is not hard to understand that finding one standard to embrace them all is a challenge.
Two years ago, Elmatica initiated a task group for medical applications. IPC accepted the challenge and founded the IPC-6012 and IPC-6013 medical device addendums with me as the chair. With experience from similarities in the automotive addendum, the task group quickly discovered the need for a different approach to the medical addendum. The purpose of the medical device addendum working group is to determine enhanced IPC standards, such as 6012 (rigid PCB) and 6013 (flex), for fabrication beyond IPC Class III to demonstrate suitability for medical devices and provide a high degree of assurance of the reliability and durability of the PCB.
Reaching Consensus in the Jungle
The task group, which consists of several members from the entire industry, first met at electronic in 2016 and has continuously developed the standardized PCB requirements for medical device applications since then. Is the work exciting? Yes! And is it challenging? Absolutely.
In an industry where failures can be fatal, the development of rigid standards is necessary. My thoughts the entire way, and the idea behind the addendum, was to find a consensus in the jungle of corporate specifications— a common document describing basic PCB requirements for medical device applications.
We collected all learnings from developing the addendum for the automotive industry and tried to do the same with medical. When developing a new standard, experiences from the complete production chain is vital, which is why it is so important to have product owners in the task group. The task group has met on a regular basis to discuss and solve challenges, discover new ones, and sometimes argue before finally agreeing. Working with standards like this often provides the feeling of one step forward, two steps back. It’s hard work, but it’s important.
When the new standards are approved, manufacturers of PCBs can rely on specific standards for production. The requirements and parameters for building and supplying PCBs for the medical device applications will then increase in reliability and transparency.
In the development of these two standards, we have come to a point where we have agreed on most of the requirements and are ready to write a draft document for each of the two standards for the industry to review. We have recently been working in two subgroups focusing on important segments that soon will be presented for the larger group where a consensus will hopefully be reached.
Rome Was Not Built in a Day
They say that “Rome was not built in a day.” Similarly, developing advanced addendums with several parameters to fulfill is not completed by just snapping your fingers either.
After several webinars and meetings, the task group found that addendums in the industry for medical device applications require a different approach than automotive. The demands and specifications that need to be considered are quite different.
The challenge is to define what specifications can apply and work for PCBs in both small sensors on and under the skin and for larger medical equipment. We have identified that PCBs used in several applications—such as implants and hearing aids—have line widths, thicknesses, hole sizes, and other features below current tolerances and limits in today’s design, performance, and acceptability standard. Imperfections in the material that in a typical PCB would be acceptable may cause application failures in these products. Volume manufacturers of standard PCBs accept a waiver of IPC’s test frequency requirements, while suppliers of these small PCBs must exceed the standards!
IPC Design Producibility Levels
“Micro PCB” is a new term recently used in discussion with members of the IPC TAEC (Technical Activities Executive Committee). We ended up with a completely new terminology, which we now call “design producibility level D.” We are pushing IPC design standards (the IPC-2220 series) to be more up to date. This will take time to implement globally within IPC, but thanks to the miniaturization in some medical device applications, these standards will be the first to use the new term.
In the IPC-2220 series, IPC refers to design producibility levels of features, tolerances, measurements, assembly, testing of completion, and verification of the manufacturing process that reflect progressive increases in the sophistication of tooling, materials or processing, and fabrication cost. These levels are:
• Level A: General design producibility (preferred)
• Level B: Moderate design producibility (standard)
• Level C: Least design producibility (reduced)
The new proposed level that was suggested due to the complexity in the PCBs for medical device applications is:
• Level D: Advanced design producibility (exceedingly reduced)
The producibility levels should not be interpreted as a design requirement, but rather as a method of communicating the degree of difficulty.
Task Group
Today, PCBs are made to customer requirements rather than following IPC standards and we do not want to continue on this page. There are 44 active members in the task group representing the PCB, electronics manufacturing, and medical industries. The task group is still open to new members. Above all, we need more product owners and people from electronics production for medical device applications to join.
Conclusion
With digitalization, AI, and IoT, the traceability and transparency to how a PCB is produced will be even more important. We must separate the PCBs that follow the standards from the ones that do not. The day will come when you or someone you know might need a medical device, and you want to make sure it does its job correctly.
Jan Pedersen is a senior technical advisor at Elmatica.
More Columns from The PCB Norsemen
The PCB Norsemen: New Trends in the PCB Industry at productronica 2019The Laminate Market: What Will the Future Bring?
The PCB Norsemen: Avoid Failures in PCB Production With Compliance Control
The PCB Norsemen: From Wooden Huts to Homemade Go-karts—It All Starts With Design!
What Is Reliability Without Traceability?
The PCB Norsemen: Merging the Best of Both Worlds—Young Superheroes and Knowledgeable Wizards!
The PCB Norsemen: My Flexible Story—Flex Circuit Development Through the Decades
A PCB Broker’s Guide Through the Galaxy of Automation