Super Dry Storage Options to Manage Intermetallic Growth
February 11, 2019 | Kelly DackEstimated reading time: 5 minutes
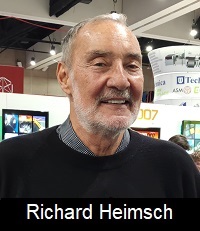
Guest Editor Kelly Dack speaks with Richard Heimsch, director of Super Dry, about some of the differences between storing components and other materials for assembly floor storage versus long-term storage, and how Super Dry can help combat intermetallic growth.
Kelly Dack: I’m sitting with Richard Heimsch, director of Super Dry, at IPC APEX EXPO 2019. Super Dry is a moisture-management, humidity-control system specialist. The job of the day, every day, is to help customers eliminate or control the humidity in their storage environments for components and other materials, correct?
Richard Heimsch: That’s right, which is particularly significant with electronic components. All of the components are hygroscopic. Once they absorb a certain amount of moisture, they pass their available floor life because they become susceptible to microcracking during reflow. So, managing the floor life and even resetting the floor life are the two fundamental tasks of the equipment sets that we manufacture.
Dack: For your equipment or services, what is the size of your customer’s requirements?
Heimsch: The storage volumes would go from 150 liters on a bench top to thousands of square feet of walk-in rooms and everything in between.
Dack: And your equipment scales to fit?
Heimsch: Correct. There are different challenges with very large warehouse-sized rooms maintaining below 5% than a bench top dry cabinet of course, but we have both extremes and lots in between.
Dack: Specifically, what are the challenges? Do you use larger equipment and more equipment, and does the cost increase?
Heimsch: Well, you need a different level of dehumidification. And when you have people working in the room, they’re bringing moisture in with them and raising the relative humidity. Thus, 5% is the critical threshold for moisture-sensitive devices. At 5% and below, you have unlimited safe storage. Above 5%, you are consuming floor life.
Dack: Are your customers throughout the U.S. or worldwide?
Heimsch: We’re a worldwide company, but I specialize in North and South America.
Dack: And is there any differences in requirements for a customer that lives in a high-humidity environment like Louisiana versus somewhere like Arizona?
Heimsch: No, it’s not a contributing factor whatsoever because in all cases, the working environment is going to be above 5% humidity; therefore, you’re consuming floor life.
Dack: How about any customer special requirements? Do you have any stories or anecdotes for customers that gave you a difficult challenge such as a niche situation?
Heimsch: Very long-term storage is a niche area that is growing in significance. Automotive and military people have had the requirement to store electronic parts for five, 10, or 15 or more years, which is well beyond any guidelines from their component manufacturers. That need has worked its way into some other electronic assembly areas. With component shortages and reduced product life cycles, the need to buy forward and store components has increased the demand and the requirement for long-term storage beyond just the extreme examples I gave before of the military and automotive segments.
So, the issues are different than assembly floor storage. Even though the low-humidity storage environment can stop oxidation—which is the principal purpose of it—there are other issues that need to be considered during long-term storage including embrittlement and especially intermetallic growth, which can also render the components useless. There is really no solution to overcome that in the way there might be if there had been oxidation and we could use a more aggressive flux. The ultra-low humidity storage will completely and totally take care of the oxidation problem, but intermetallic growth is a different situation and has been for many years.
Within the past couple of years, we had a breakthrough in that area and proved that by lowering the ambient temperature during long-term storage, we could significantly inhibit the growth of intermetallics. So, what had been one of the simpler product offerings has moved into one of the more complex solutions. We actually do long-term storage as a service, which gives us the opportunity to collect a lot of data on the situation. You need to periodically test components for integrity in many different categories over a quarterly, yearly, or bi-yearly basis, etc.
We recently published new data about the fact that dry storage is at least as effective as nitrogen if not better in terms of preventing oxidation. This has been an age-old, ongoing debate about the need for nitrogen to prevent oxidation. In fact, it’s the loose oxygen atom in the water molecule that’s the problem. You must have an electrolyte to create the corrosion. And it’s that loosely bonded oxygen atom in the water molecule, not the tightly bonded O2 molecules, that are triggering the oxidation.
A lot of people in the plating business, for instance, have known this for a long time. Within electronics, nitrogen was the only solution available 20+ years ago (when standards began to be published). To have any kind of oxidation mitigation, the removal of oxygen was believed to be essential to prevent it, and that has been disproven. Thus, by testing components in three environments over long periods of time or even a couple of years, we have concrete data and proof.
Dack: Again, what are the three environments?
Heimsch: Nitrogen, ambient, and a dry cabinet or low-humidity environments. In an ambient environment, you have oxidation running wild, but nitrogen and low-humidity environments are virtually equal in those results. And though it’s still very niche, the reduction of temperature to manage the intermetallic growth is significant and further extends the useable life of the components.
The elimination of nitrogen is an objective because it’s expensive and wasteful, and it doesn’t do as good a job as an ultralow-humidity environment will do. Getting nitrogen that’s less than 5% relative humidity is not a simple thing to do, and IPC/JEDEC specifications require a less-than-5% environment for unlimited safe storage. The additional issue that an assembly house wouldn’t necessarily need to deal with because their components are being utilized on a short-term basis is the intermetallics. And that’s where the long-term situation introduces or enlarges the need for an additional controlled solution.
In summary, for decades, military and automotive companies have needed to store parts for very long periods of time—10 years and longer as well as for avionics and trains as additional examples—but now, long-term storage is an issue even for more mainstream OEMs because of component shortages and very short product life cycles. This is forcing people to buy volumes of components ahead of time and understand how to store them safely because the storage time far exceeds anything that their component manufacturers have recommendations for.
Dack: Very good. Thanks so much for your time today, Richard.
Heimsch: Absolutely.
Suggested Items
Top Tech in Taiwan: IPC's Blueprint to Advance Smart Manufacturing
06/04/2025 | Sydney Xiao, IPCRenowned as a global hub of innovation and a cornerstone of the electronics industry, Taiwan is leading advancements in technology and manufacturing. A decade ago, IPC established an office in Taiwan, embedding itself deeply in this innovative ecosystem. Now with nearly 200 member companies in the region, IPC remains dedicated to driving standardization, education, and technological progress in Taiwan’s electronics manufacturing sector.
IPC Releases Latest Standards and Revisions Updates
06/05/2025 | IPCEach quarter, IPC releases a list of standards that are new or have been updated. To view a complete list of newly published standards and standards revisions, translations, proposed standards for ballot, final drafts for industry review, working drafts, and project approvals, visit ipc.org/status. These are the latest releases for Q1 2025.
IPC Launches New Wire Harness Design Course Led by Defense Industry Expert
06/03/2025 | I-Connect007 Editorial TeamIPC is expanding its educational offerings with a new online course designed to provide foundational knowledge in wire harness and cable design. The course, Introduction to Wire Harness Design I, is led by a seasoned mechanical engineer and subject matter expert in military cable systems working at FNSS Defense Systems in Turkey.
Nolan’s Notes: Moving Forward With Confidence
06/03/2025 | Nolan Johnson -- Column: Nolan's NotesWe’re currently enjoying a revitalized and dynamic EMS provider market with significant growth potential. Since December 2024, the book-to-bill has been extremely strong and growing. Starting with a ratio of 1.24 in December, book-to-bill has continued to accelerate to a 1.41 in April. Yet, there is a global economic restructuring taking place. To say that the back-and-forth with tariffs and trade deals makes for an uncertain market is an understatement. While we may be in a 90-day tariff pause among leading economic nations, the deadline is quickly approaching and that leaves many of you feeling unsettled about what to expect.
IPC Issues Call for Participation for IPC APEX EXPO 2026
06/02/2025 | IPCIPC is now accepting abstracts for technical papers with presentations, posters, and professional development courses at IPC APEX EXPO 2026.