-
- News
- Books
Featured Books
- pcb007 Magazine
Latest Issues
Current IssueSales: From Pitch to PO
From the first cold call to finally receiving that first purchase order, the July PCB007 Magazine breaks down some critical parts of the sales stack. To up your sales game, read on!
The Hole Truth: Via Integrity in an HDI World
From the drilled hole to registration across multiple sequential lamination cycles, to the quality of your copper plating, via reliability in an HDI world is becoming an ever-greater challenge. This month we look at “The Hole Truth,” from creating the “perfect” via to how you can assure via quality and reliability, the first time, every time.
In Pursuit of Perfection: Defect Reduction
For bare PCB board fabrication, defect reduction is a critical aspect of a company's bottom line profitability. In this issue, we examine how imaging, etching, and plating processes can provide information and insight into reducing defects and increasing yields.
- Articles
- Columns
- Links
- Media kit
||| MENU - pcb007 Magazine
Estimated reading time: 4 minutes
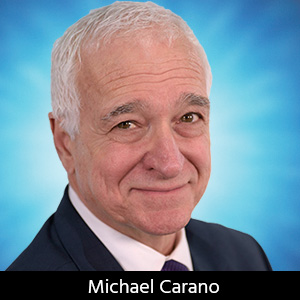
Contact Columnist Form
Trouble in Your Tank: The Art and Science of Resist Stripping, Part 2
In Part 1 of this series on resist stripping, I presented some of the basics related to resist stripping chemistry. The pH curves of the performance of generic resist strippers were used to illustrate stripping behavior during the process as well as the best method to control the stripping process.
In Part 2, I will focus on some additional performance properties of the resist stripping, such as:
- “Cleanliness” of stripping
- Size of stripper skins (i.e., the stripped particles)
- Tarnishing of the copper surface
- Attack/activation of tin or tin-lead etch resists (this will be explored in a future column)
Dry Film Resist Complexities
Before delving into the bullet points listed above, it would be a good idea to get an understanding of resist technology in general. Photoresist is a complex mix of chemicals. Photoresists are commonly composed of acrylic resins, polyvinyl cinnamates, diazo compounds, phenol-formaldehydes, or other similar film-forming materials. Photoresists can be applied dry or wet to a substrate. After the exposure process of step, the photoresist-covered copperclad laminate sandwich goes through the developing step. The entire panel is exposed to carbonate-based chemistry, which reacts with and dissolves the unexposed portions of the photoresist. The exposed portions of the photoresist do not react with the carbonate-based developer chemistry. What is left behind is the desired circuit pattern atop the laminate. Bare (uncovered) copper (foil) remains in the areas where the unexposed photoresist was removed.
Thus, a later step is the not-so-trivial job of removing the exposed resist. This is far from simple and requires a thoughtful evaluation of process parameters and resist stripping formulations.
Cleanliness: Removing All the Exposed Resist
What exactly does that mean? For most, this means an efficient and rapid removal of the exposed resist from the panels. One may conclude that cleanliness and resist stripper particle size are related. This includes dislodging and removing the exposed resist from tight spaces (more critical today for HDI designs) as well as any resist that may be trapped under an over-plated trace or pad.
One performance attribute of resist stripping technology is the ability of the chemistry to break down the exposed resist in small particles. As the resist stripper attacks the backbone, the resist will release from the copper surface and break into particles of various sizes. The particles must be small enough to be dislodged from recessed resist channels between pattern-plated features. This is especially important if the resist pattern is “over-plated” (i.e., the plating has mushroomed over the resist and makes it even more difficult for the resist particle to escape). There is also the notion that the resist should have some degree of solubility in the stripper, so that a thin residue of resist left on the copper after the initial breakup of the resist matrix into flakes will dissolve later in the stripping cycle to leave a clean surface.
It is noteworthy that various resists will react differently when they come into contact with the particular resist stripping formulation.
Size of Stripped Particles
To enable a smooth operating resist stripping operation, remove the resist as small particles or chips. As one may surmise from Figure 1, different photoresist composition strips in various particle sizes at different speeds in numerous resist stripping formulations will lead to varying results. Further, the initial size of the stripped particles reduces under the impact of sprays. However, not all resists have the same propensity to break up under a given spray impact. Fortunately, one can manipulate the particle size (within limits) by selecting the stripper chemistry, temperature, and concentration (Figure 2).
Figure 1: Commercially available resist (L) versus a second (R). Under the same resist stripping conditions, the right resist strips much faster and more completely in the given time.
Figure 2: Same photoresist in each beaker, but two different resist stripper formulations (right shows more effective resist removal).
While attempting to enhance resist stripping for those more difficult to remove resists, here is a word of caution. Manipulating dwell times, concentrations, and operating temperatures will have adverse effects on metal etch resist attack, copper darkening, and potentially higher cost. This is where different resist stripping formulations should be evaluated.
Tarnishing of the Copper Surface
A second part of the cleanliness equation is the stripping process must leave the copper surface free of any staining, tarnishing, or any other cosmetic issues. High-pH resist stripping formulations tend to oxidize the bare copper. It is critical that most resist stripper formulations contain effective compounds to prevent oxidation. In addition, certain additives within the resist formulation itself can leave stains on the copper. These additives are dye precursors used to cause a color change during exposure.
These dyes can form complexes with the copper surface. Thus, these stained complexes are difficult to remove. If this is an issue, the fabricator must ensure that the resist stripping formulation contains solvents to break that bond and leave the copper surface clean.
Conclusion
Yes, there is some art to the resist stripping operation. However, it is more about the science. In a future column, I will present process control methods for resist stripping as well as dive into additional troublesome activities related to the process.
Michael Carano is VP of technology and business development for RBP Chemical Technology.
More Columns from Trouble in Your Tank
Trouble in Your Tank: Can You Drill the Perfect Hole?Trouble in Your Tank: Yield Improvement and Reliability
Trouble in Your Tank: Causes of Plating Voids, Pre-electroless Copper
Trouble in Your Tank: Organic Addition Agents in Electrolytic Copper Plating
Trouble in Your Tank: Interconnect Defect—The Three Degrees of Separation
Trouble in Your Tank: Things You Can Do for Better Wet Process Control
Trouble in Your Tank: Processes to Support IC Substrates and Advanced Packaging, Part 5
Trouble in Your Tank: Materials for PWB Fabrication—Drillability and Metallization