Estimated reading time: 3 minutes
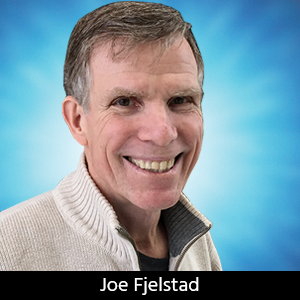
Flexible Thinking: Ways to Conserve Flex Circuit Material in the Design Process
As the reader has likely already determined, flexible circuits are an excellent technology for making electronic products that are bendable, shapeable, lighter, and smaller than those made using rigid materials. However, flexible circuit materials also tend to be a bit more costly than rigid materials. To save money on the product, it is necessary to conserve material in design.
In this regard, the flex circuit designer is arguably the most important person in the entire flex circuit manufacturing process in meeting this objective.
The decisions made by the flex circuit designer are going to carry over to every other part of the process and can have a significant impact on the ultimate or overall cost of the assembly.
To that end, it is essential that the flex circuit designer be attentive to any features that are likely to impact the cost. One should aim to reduce overall material use, which can help keep manufacturing costs down. Good enough, but what can the designer do specifically? One of the first things the flex circuit designer can do is to design circuits that can be closely spaced on the processing panel. While panelization is not something the circuit designer is normally tasked with, the choices the designer makes will have a definite effect on how closely the circuits can be spaced relative to one another on the panel. Close spacing and maximum utilization of the material is accomplished by carefully arranging the circuit on the panel to ensure the greatest use of material.
This important technique of optimizing the number of circuits per panel is called nesting. While it is a goal to use the maximum material, there are other forces in play. Sometimes, it is more important to optimize the layout rather than maximize material use to meet critical engineering needs that might affect performance or reliability. For example, when laying out a flex circuit, one must know the end use.
In some cases, the circuit may be called upon to serve a dynamic interconnection circuit. In such circumstances, there may (or should) be a demand that portions of the flex circuit be properly oriented relative to the grain direction of the foil—such as is required for dynamic flexing. When addressing this need, the result may be that there is a less than maximum material use for circuit construction.
However, when this concern is absent, the opportunity to lay out the circuit to get the most out of the material should not be missed. While nesting is routinely performed by the flex circuit manufacturer to conserve material and increase internal productivity, the designer can aid in this process by taking advantage of the fact that flex circuits can be bent and folded.
An example of how this might be accomplished can be seen in Figure 1. Note that by adding a small additional length to a circuit “arm,” the circuit can be nested more efficiently and allow the flex circuit to be more economically produced. There are some issues that must be considered when taking this approach, however, as the terminations are flipped. There is also the prospective provisional concern that the circuit must go through a second operation to fold it; therefore, the economics of folding must be evaluated.
In addition, if the circuit is to be dynamically flexed, this step may be precluded for reasons related to mechanical reliability—a topic that will be discussed in a future column. In short, this general technique requires that the entire manufacturing and assembly process be given some consideration before progressing.
In summary, the decisions made by the flex circuit designer when laying out a flex circuit will have an impact that lasts the entire process. By considering how the circuit might fit onto a panel before submitting the design to a manufacturer, it may be possible to save a considerable amount of material and money. Not all designs will allow such freedom, but it is worth keeping in mind for those applications where the benefit can be secured.
Proper circuit nesting can greatly improve panel yield and lower overall cost. If folding can be tolerated as an assembly operation, yield can be maximized. For dynamic flex circuit designs, the grain direction requirement may impact layout.
More Columns from Flexible Thinking
Flexible Thinking: The Key to a Successful Flex Circuit Design TransferFlexible Thinking: Flexible Circuit Technology—Looking Back and Forward
Flexible Thinking: Mind-tapping into January
Flexible Thinking: Another PCB Design Paradigm Shift in the Works
Flexible Thinking: Rules of Thumb—A Word to the Wise
Flexible Thinking: Musings on High Density Interconnections
Flexible Thinking: Integrated Passive Devices—Design Solutions With Many Benefits
Flexible Thinking: Mechatronics in a Flex World